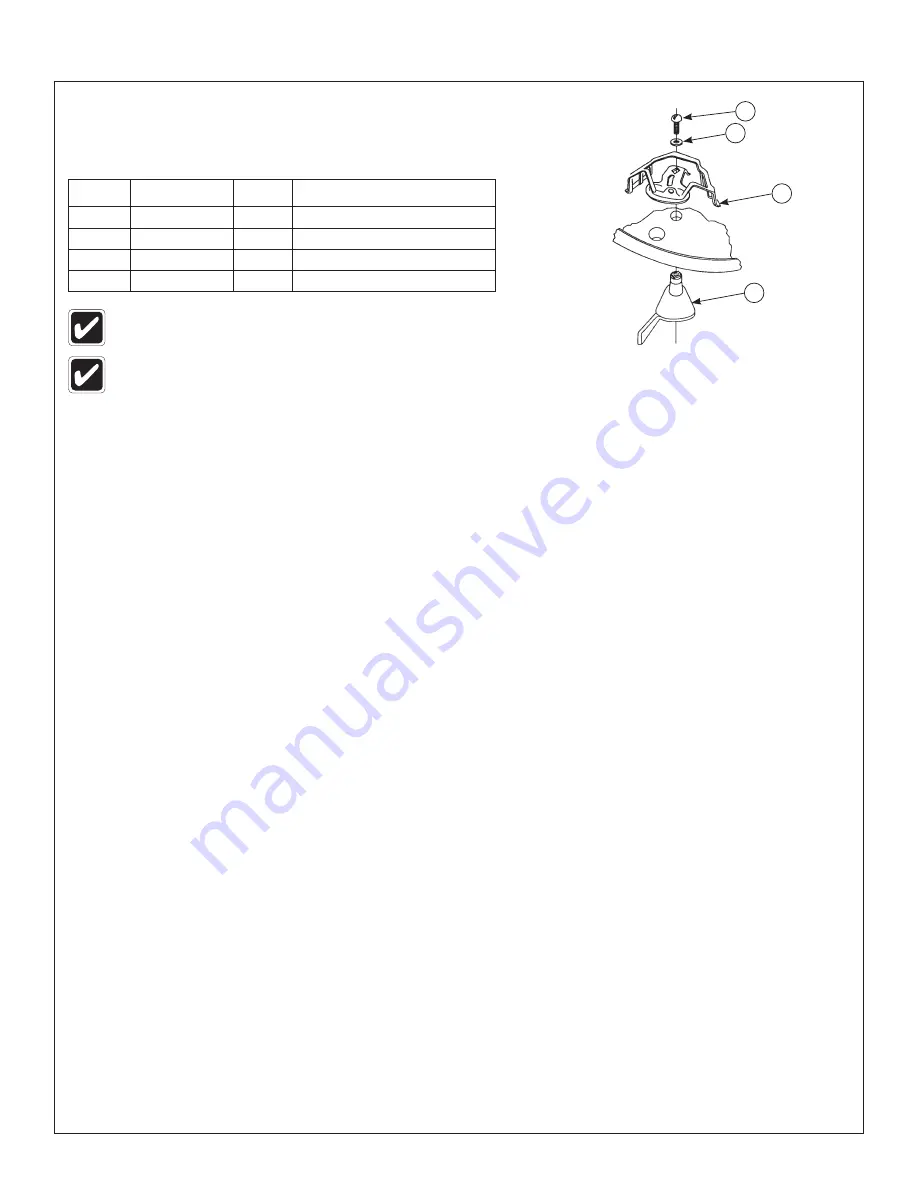
Installation
WF2613
Bradley
•
215-1451 Rev. F; ECN 13-00-001
3/5/2013 15
Soap Valve — Powdered — S09-010A
Parts List
Item
Part No.
Qty
Description
1
160-069
1
Screw, 1/4-20 RD
2
142-002X
1
Washer, 1/4 Split-Lock
3
S62-002
1
Agitator / Slide Assy.
4
192-004
1
Lever - Powdered Soap
Reducer plugs are available for use with fine granulated
soap to reduce the flow.
Valves can be changed from powdered to liquid by plugging the innermost, or “bearing” hole with rubber plug, part
number 125-001AK. To change from liquid to powdered, the plug must be removed. If none is present, it will be
necessary to drill out the bearing hole with a 1/2" or 5/8" drill. The plastic container configuration forms a natural
template for locating the bearing hole.
1
2
3
4
Soap Recommendations
Quality soap dispensers require good quality soap and periodic maintenance to properly operate. Bradley soap dispensers will
provide dependable, consistent operation over the long term when soap with reasonable viscosity and pH levels are used and
when a minimal amount of periodic maintenance is performed on the valves.
Soap thickness is determined by a measurement called viscosity. Soap viscosity should be between 100 cps (centerpoise) and
2500 cps for all Bradley soap dispensers. Thinner soaps are perceived by the users as being “watered down” so users tend to
take more than they need, resulting in waste.
Thick soaps flow slower and inhibit the “flushing” action of the valves, which
allows the soap to congeal in the valve and cause clogs.
The pH (acid) level of the soap should be in the range of 6.5 to 8.5. More acidic soaps (pH levels lower than 6.5) will corrode
metal parts (even stainless steel!!) and degrade rubber and plastic components. They will also cause skin irritation.
Most
inexpensive soaps (typically the pink lotion type) fall into this acidic category and will eventually cause valve failure and
metal corrosion. Base soaps (pH levels higher than 8.5) will cause swelling or degradation of rubber and plastic parts and skin
irritation.
Generally, any quality soap meeting the viscosity and pH guidelines above will work well with Bradley soap dispensers. PCMX
or Isapropanol based antibacterial soaps (within viscosity and pH limits) will also work with Bradley dispensers. Soaps satisfying
these basic guidelines will provide consistent flow and reduce clogs.
Most soap dispenser problems are caused by soap that is too thick or corrosive, or by a lack of maintenance. Many soaps come
in concentrate form which must be diluted with water. Often, the soap is improperly diluted or used straight out of the bottle, which
causes clogging and valve failure. If proper soap is being used, valves that have never been cleaned are usually the source of
dispensing problems. Bradley has entered into an agreement with Champion Brand Products to provide additional customer
service for purchasers of our dispensers regarding soap issues. They are very helpful and can get to the bottom of almost any
soap dispenser related problem. They also sell an excellent “Bradley approved” soap. Please see
Soap Instruction Sheet 215-1286
for details about soap valve cleaning or how to contact Champion. With proper maintenance and soap, Bradley dispensers will
provide long term, trouble free operation.
Soap Dispenser Maintenance Instructions
Bradley soap dispensers will provide dependable, consistent operation over the long term when the proper soap is used and when
a minimal amount of periodic maintenance is performed on the valves. Valves must be maintained (cleaned) to function properly.
To ensure proper operation of your soap dispenser, follow these instructions:
• Once per month, unscrew valve from reservoir and soak it for 30 minutes in hot water.
• Push valve at least 20 times while it is soaking.
• Flush soap reservoir with hot water while valve is soaking.
In cases of extreme clogging, the valve should be disassembled and the parts should be soaked in hot water or cleaning solution
to restore proper functioning. Soap dispensers that will not be used for extended periods of time (schools during summer break,
etc.) should be drained, cleaned and left empty until put back into service. Soap left on the outside of dispensers can cause
discoloration and corrosion of the reservoir (even on stainless steel units). All soap should be wiped or scrubbed off daily, then the
outside of the dispenser should be rinsed with clear water and dried with a soft cloth.
Soap Maintenance Tips