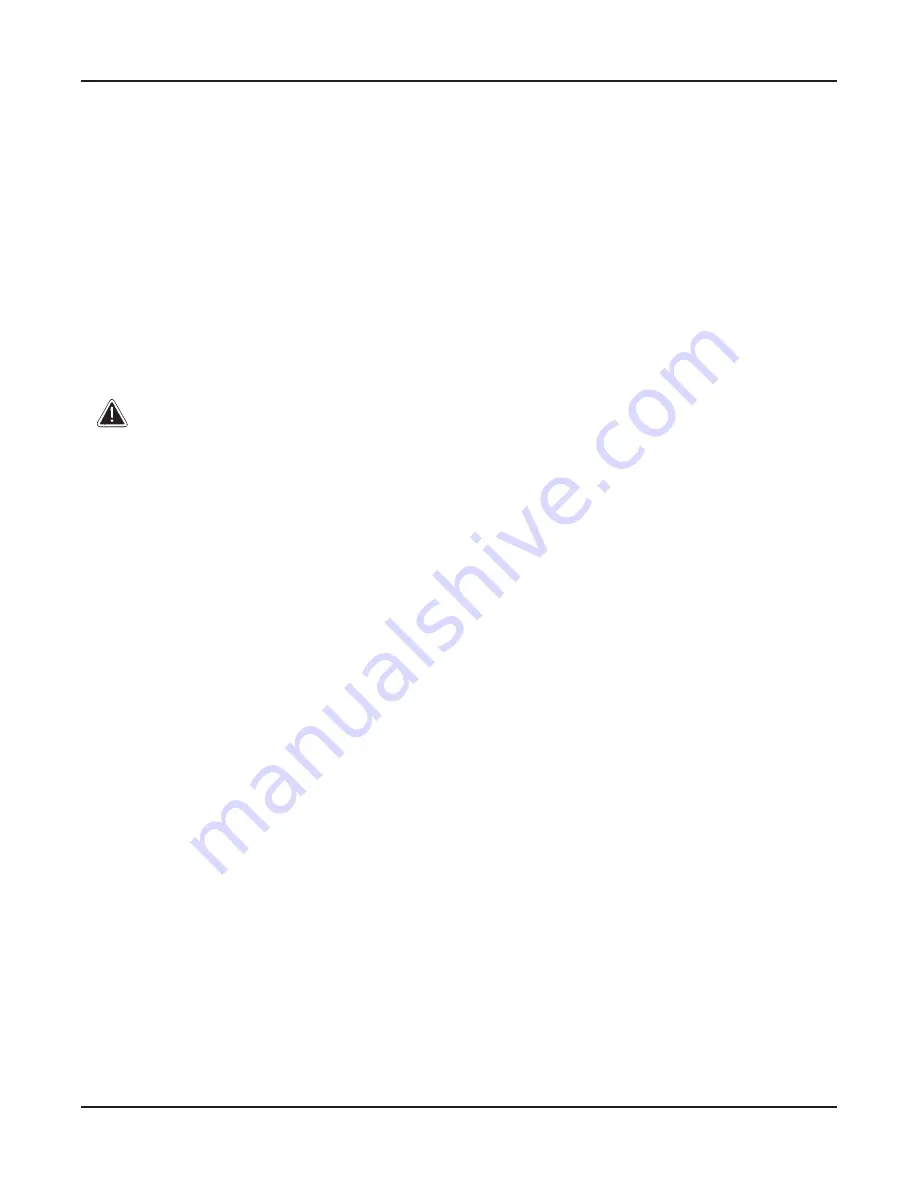
14
Express® Lavatory System SS-Series
SS-2/AST/STD, SS-2/AST/JUV
Installation - Obsolete
4/24/08
Bradley Corporation • 215-1244 Rev. D; EN 08-805
Soap Dispenser Maintenance continued . . .
Step 2: Change soap type
1. Pour out all of the soap from the dispenser.
2. Rinse the soap dispenser with hot water several times until all of the residue is removed, and
pump the valve until clean water appears.
3. Rinse the dispenser with ethyl alcohol and allow to air dry.
4. After the dispenser is dry, pour the new soap into the soap dispenser.
Step 3: Cleaning Instructions
Regular cleaning of the soap dispenser is recommended to ensure optimum performance and
maximum service life. Cleaning the soap dispenser monthly to remove soap residue, dirt, and
other accumulations should become a regular part of your washroom cleaning routine and general
maintenance program.
IMPORTANT: Do not use abrasive cleansers to clean the soap tank. Abrasive
cleaners can mar the surface.
Clean exterior:
Use warm water and soap to clean the exterior of the soap dispenser. Dry with
a soft cloth.
Clean interior:
Inspect the interior of the soap tank for residue or coagulation of soap. If
necessary, clean the soap tank according to the following procedure:
1. Pour out any remaining soap in the tank.
2. Fill the tank half-full of hot water and shake the tank to dislodge the soap residue.
3. Empty the water from the container and repeat steps 1 and 2 until the soap container is clean.
NOTE: If rinsing alone does not remove the soap residue, place a small chain (24 inches long)
into the soap tank with hot water and shake the container until the chain dislodges the residue.
Then remove the chain and rinse out the soap tank.
Clean internal components:
To clean the internal components of the soap dispenser, pump
hot water through the soap dispenser until a clean flow of water comes out of the valve.
Check Valve Troubleshooting
If water just dribbles or does not flow from sprayhead:
1. Close the stops and check the valves that supply water to the lavatory system.
2 Inspect the stop/check valves for proper installation.
3. Remove the flexible hoses from the stop/check valves and clean the strainers, if necessary.
If water sprayhead delivers all hot or cold water:
1. Close the stops and check the valves that supply water to the lavatory system.
2. Inspect the stop/check valves for proper installation.
3. Remove the flexible hoses from the stop/check valves and clean the strainers, if necessary.
4. Inspect mixing valve for proper installation (see Vernatherm valve on page 19).
• A red marking indicates the hot inlet.