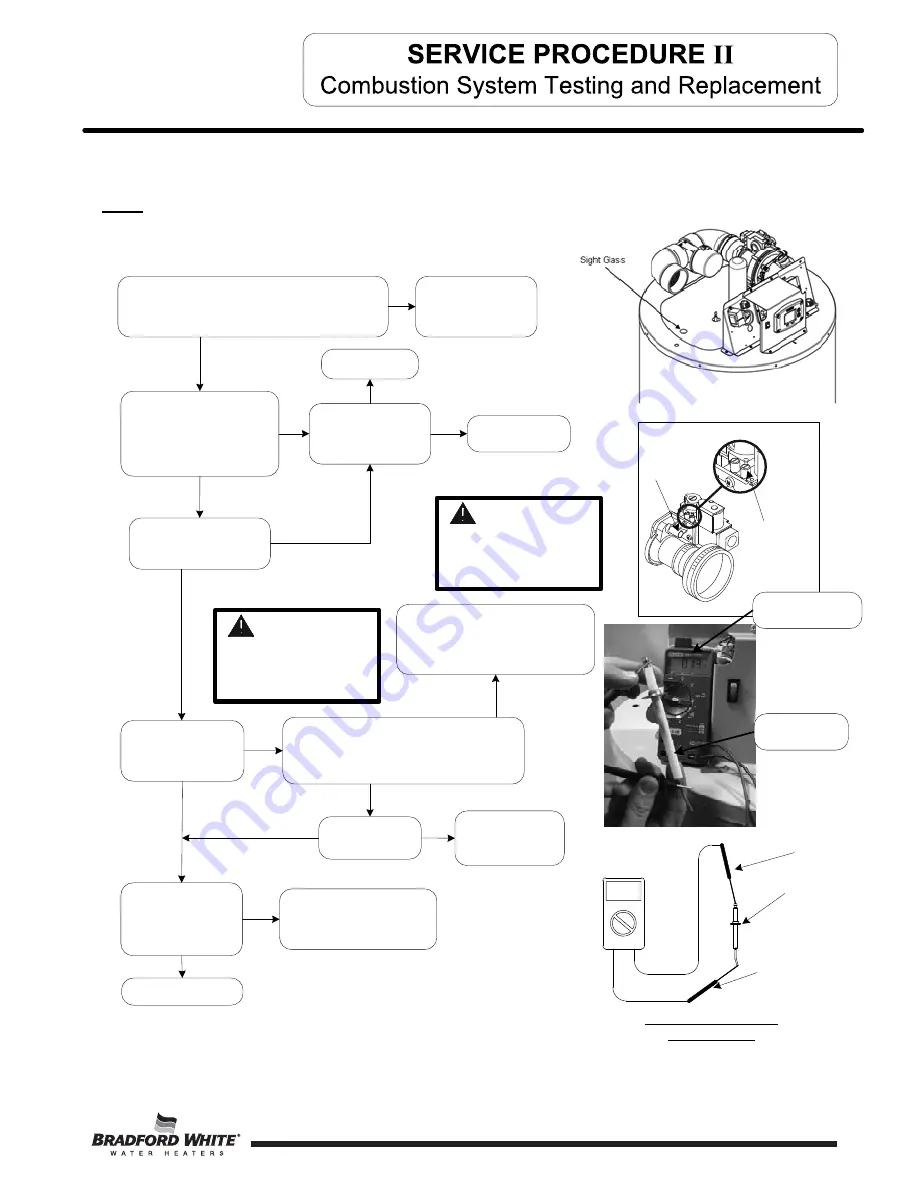
D
oes
in
l
et
gas
pressure
drop
more
than
2
"
W
.
C
.
during
burner
ignition
?
A
d
j
ust
gas
supp
l
y
regu
l
ator
I
nade
q
uate
l
y
si
z
ed
regu
l
ator
.
Y
N
N
Y
N
Y
N
V
erify
M
inimum
G
as
Supp
l
y
Piping
Re
q
uirements
of
:
M
inimum
¾"
N
P
T
.
(Schedu
l
e
4
0
b
l
ac
k
I
ron
Pipe
recommended)
.
Reconfigure
gas
supp
l
y
piping
Y
O
bser
v
e
burner
operation
through
the
sight
glass
located
on
the
combustion
insert
mounting
flange.
N
ormal
burner
operation
should
ignite
smoothl
y
,
without
e
v
idence
of
coughing
or
huffing
upon
ignition.
T
he
burner
flame
should
be
a
blue
flame
near
the
burner
surface
in
a
uniform
flame
pattern.
O
ccasional
y
ellow
or
white
strea
k
s
are
normal.
I
nlet
gas
pressure
tap
V
enturi
ad
j
ustment
D
oes
main
burner
L
ight
?
Remove
high
vo
l
tage
wire
connected
at
the
spar
k
rod
and
ho
l
d
appro
x
imate
l
y
¼"
from
meta
l
ground
with
insu
l
ated
p
l
iers
during
the
ignition
cyc
l
e
(3
second
spar
k
tria
l
period)
.
I
s
there
spar
k
to
ground
?
Y
N
Chec
k
spar
k
gap
to
burner
(see
“Spar
k
Rod
G
ap
I
nspection”)
Chec
k
resistance
of
high
vo
l
tage
cab
l
e
.
Resistance
shou
l
d
be
0
-
1
ohms
.
I
f
resistance
is
high,
rep
l
ace
spar
k
cab
l
e
. I
f
spar
k
cab
l
e
is
good,
rep
l
ace
Contro
l
B
oard
.
N
Y
Can
Spar
k
ing
be
seen
/
heard
at
the
spar
k
rod
to
the
burner
?
Proceed
to
ne
x
t
page
W
ith
manometer,
chec
k
in
l
et
gas
pressure
. I
s
it
stab
l
e
between
7
"
&
1
4"
W
.
C
.
static
?
(heater
not
running)
(see
i
ll
ustrations
at
right)
I
s
gas
supp
l
y
pressure
regu
l
ator
ad
j
ustab
l
e
to
maintain
proper
and
stab
l
e
setting
?
Y
N
W
A
R
NIN
G
120
vo
l
t
potentia
l
exposure
.
Use
caution
making
vo
l
tage
checks
to
avoid
persona
l
injury
.
W
A
R
NIN
G
Removing
screw
from
in
l
et
gas
pressure
tap
wi
ll
immediate
l
y
a
ll
ow
gas
to
f
l
ow
from
pressure
tap
.
N
ote: Mode
l
s
using
meta
l
fiber
mesh
burner
a
red
g
l
ow
from
the
burner
surface
is
norma
l.
3
1
Chec
k
continuity
of
spar
k
rod
. I
s
reading
0
-
1
Ohm
?
Y
N
Rep
l
ace
Spar
k
Rod
(see
“Spar
k
Rod
G
ap
I
nspection
and
Rep
l
acement”
C
HE
C
K
S
P
A
R
K
RO
D
R
E
S
I
S
T
A
N
C
E
M
eter
probe
M
eter
probe
S
par
k
R
od
V
olt
meter
set
to
O
HM
setting
V
oltmeter
set
to
O
HM
setting
S
par
k
R
od
31