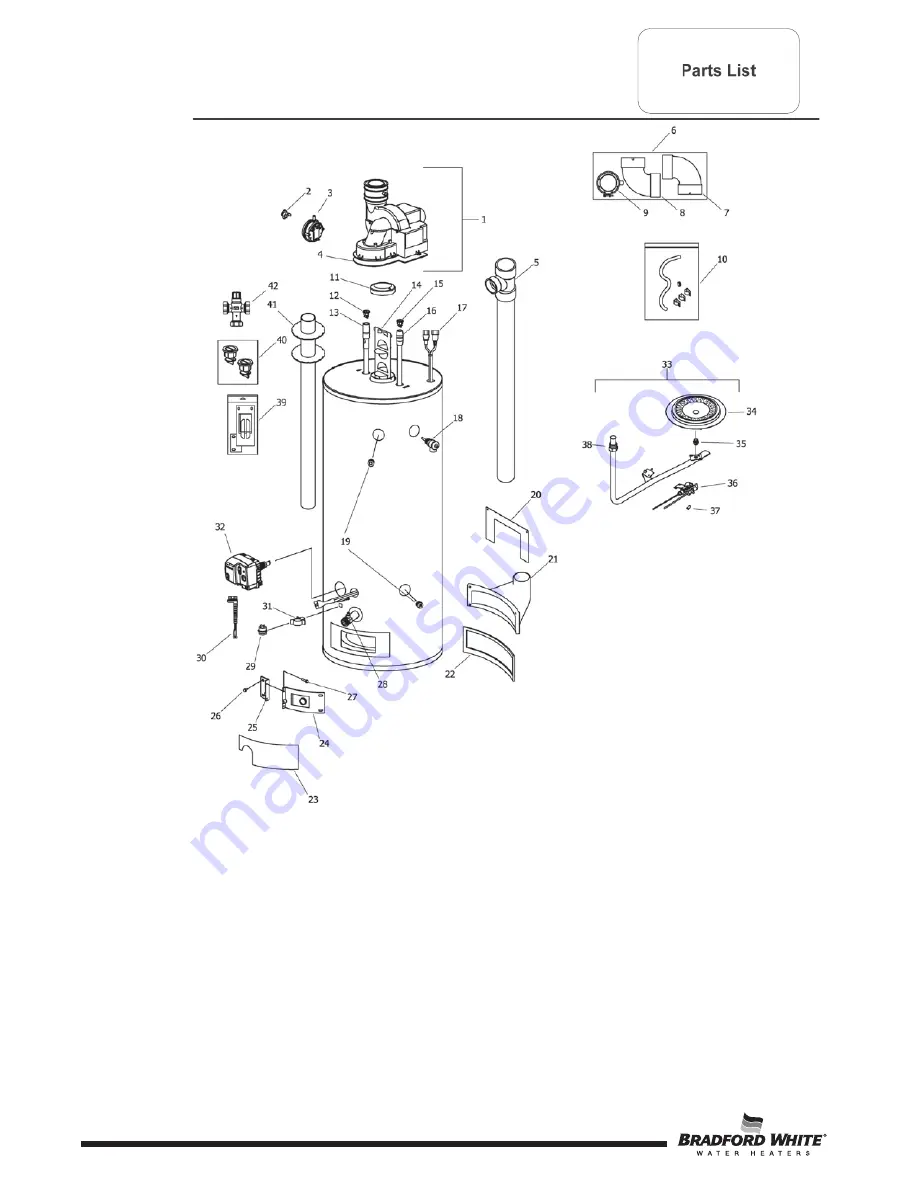
38
PDV Series
38
1. Blower Complete
2. Temperature Switch
3. Pressure Switch
4. Blower Gasket
5. Tee and Vent Pipe Ass’y
6. Vent Adapter w/ Term.
7. Intake Terminal
8. Vent Terminal Elbow
9. Exhaust adapter
10. Condensate Hose Kit
11. Flue Reducer (50H Only)
12. Heat Trap Outlet
13. Hot Water Outlet Anode
14. Flue Baffle (except 75H)
15. Heat Trap Inlet
16. Inlet Dip Tube
17. Wire Harness
18. T&P Valve
19. ¾ NPT Plug
20. Direct Vent boot
escutcheon
21. Air intake boot
22. Air intake boot gasket
23. Outer Door
24. Right side inner door
25. Left side inner door
26. Screw #10-12 x ¾
27. Screw #8-15 x ¾
28. Drain valve
29. FV Sensor
30. FV Sensor harness
31. FV Sensor Clip
32. Gas Control
33. Burner Assy.
34. Main Burner
35. Main Burner Orifice
36. Pilot Assy.
37. Pilot Orifice
38. Feedline
39. Inner Door Gasket Kit
40. Kit-Heat Trap insert
41. Flue core (75H only)
42. ASSE Approved Mixing
Valve