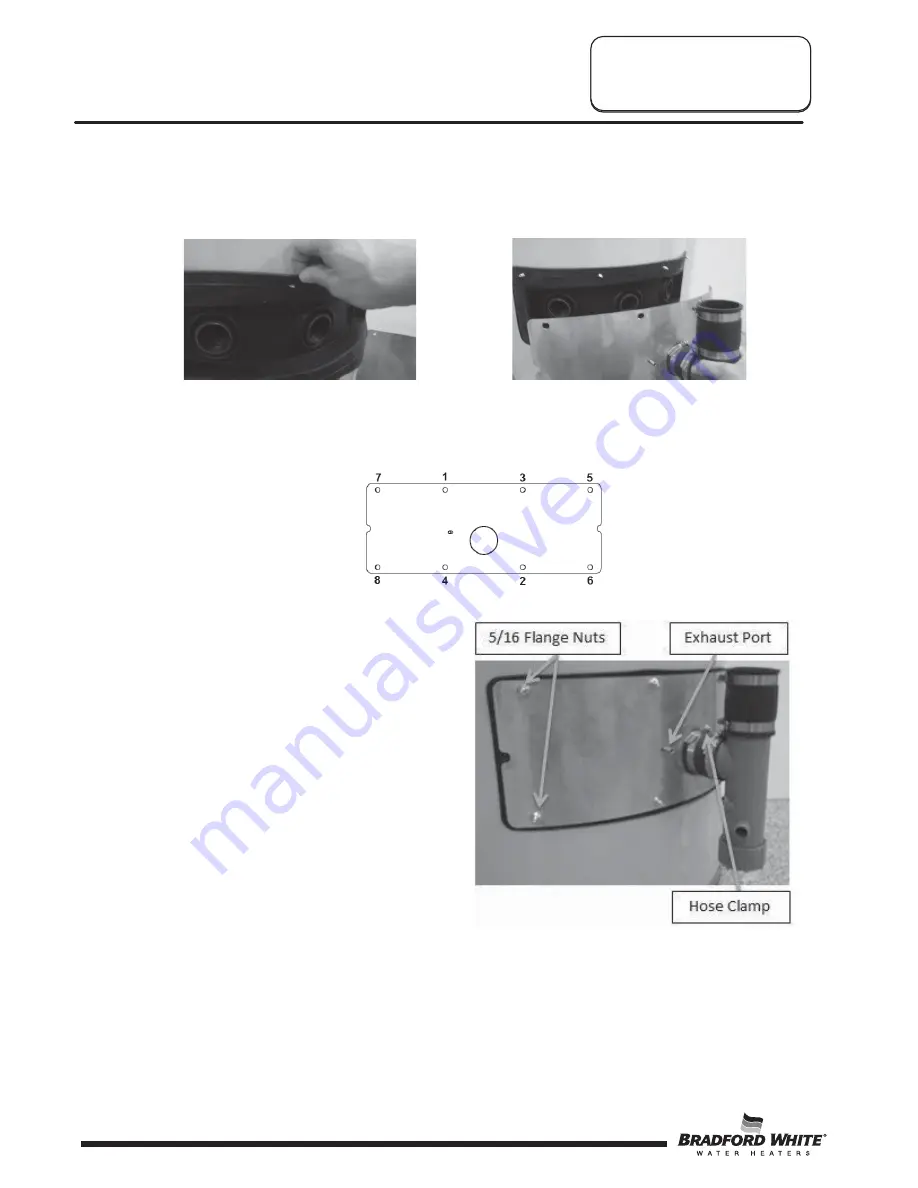
Condensing PDV Series
40
Service Procedure XIV
Condensate Trap Removal,
Inspection, & Replacement
d. Align the gasket flange holes to go over the studs extending through the jacket. After
verifying that the studs are through the flange holes and that the gasket is sealed
around the secondary flue tubes, return the cover such that the studs extend through
the openings.
e. Hand start the nuts that were removed in step 3 onto the studs on all 8 locations to
ensure a proper fit. Begin securing the 5/16” nuts with an wrench or a socket. This
process should be done following the diagram below. Each flange nut should be
tightened to 25 in*lbs.
Step 6. Once all the flange nuts are back in place,
reconnect the ¼” clear tubing onto the port
on the cover.
Step 7. Connect the condensate tee and coupler to
the neck provided on the cover and secure
by tightening the hose clamp.
Service Procedure XV
Exhaust Collector Removal,
Inspection, & Replacement
40