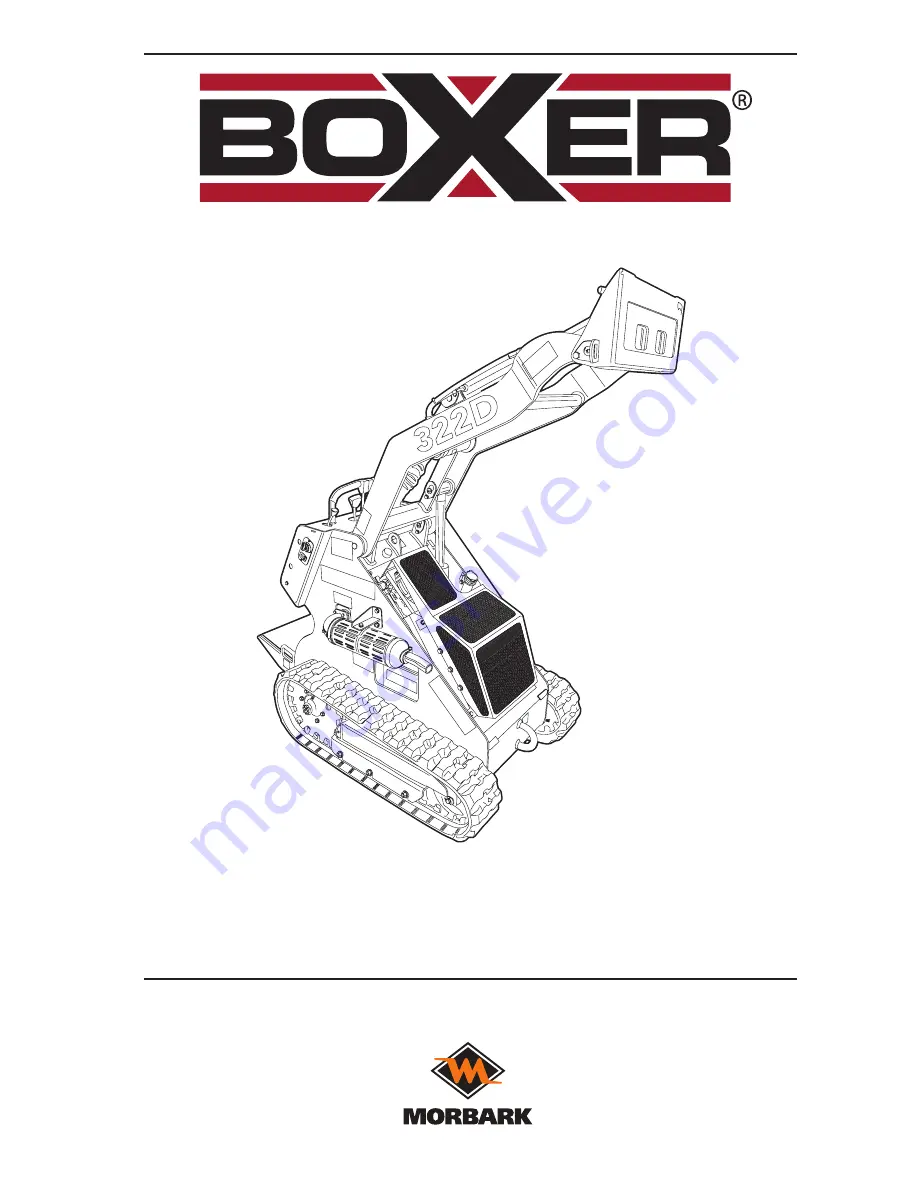
Serial No.s 3631 and Higher
Part No. 76347-293
Manufactured by:
322D Operator’s Manual
Phone: Morbark
®
, LLC
Sales - 800-831-0042
8507 S. Winn. Rd., P.O. Box 1000,
Parts and Service - 800-255-8839
Winn, Michigan 48896
www.boxerequipment.com
www.morbark.com
B I G P O W E R I N A L L P L A C E S
®
Revised: 09/18/2018