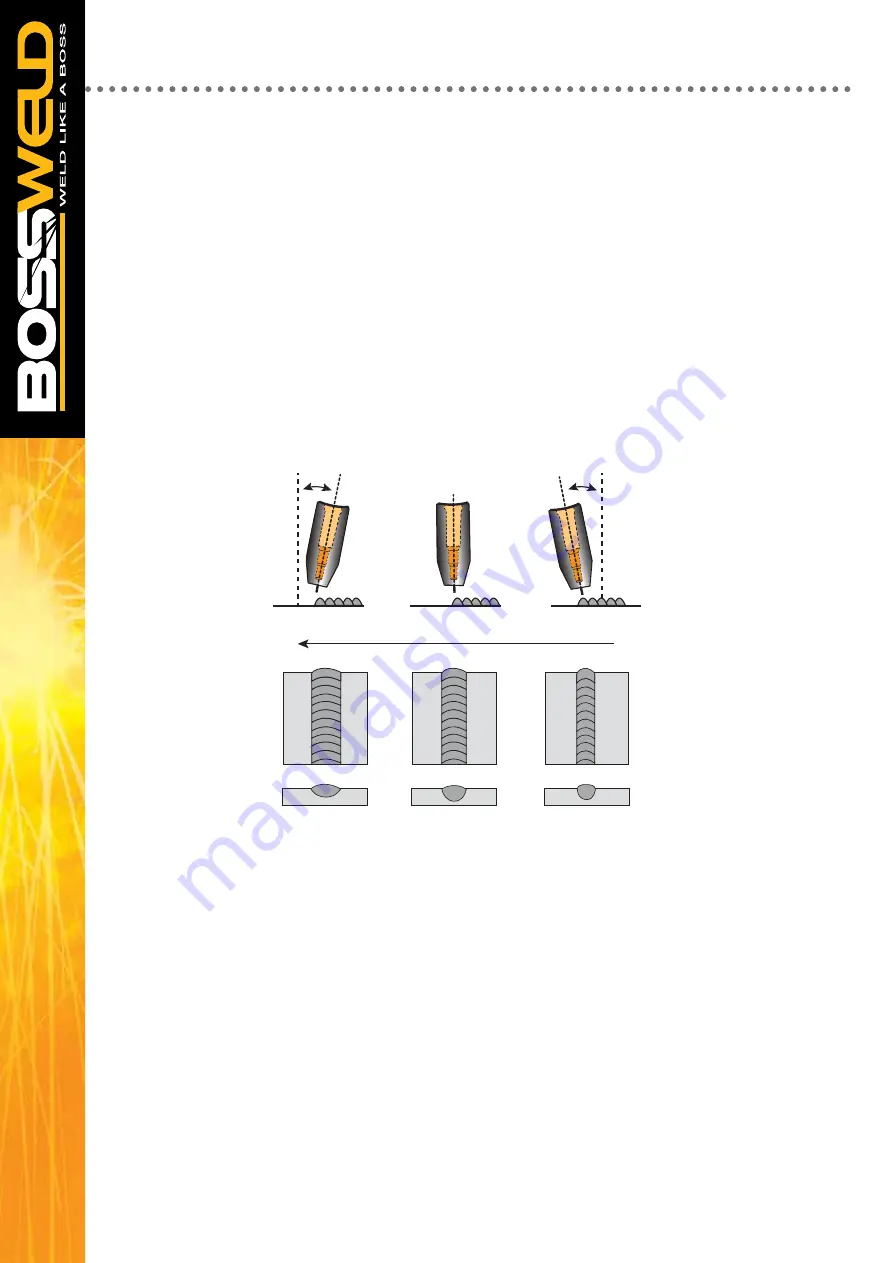
20
BASIC MIG WELDING GUIDE
The welding power supply has two control settings that have to balance. These are voltage control switches
and the wire speed control. The welding amperage is determined by the voltage settings, the wire diameter,
gas selection and the wire feed speed. The amperage will increase with higher voltage selection on the
machine and higher wire feed speed. This is typically used for welding thick sections of steel. When welding
thin sections of steel, a lower voltage selection and lower wire feed speed is required.
• When changing to a different wire diameter different control settings are required. A thinner wire needs
more wire speed to achieve the same current level.
• A satisfactory weld cannot be obtained if the wire speed and voltage switch settings are not adjusted to
suit the wire diameter and thickness of the material being welded.
• If the wire speed is too high for the welding voltage, “stubbing” will occur as the wire dips into the molten
pool. If the wire speed is too slow for the welding voltage, large drops will form on the end of the
electrode wire, causing spatter. Suppose that wire speed is constant, if the welding voltage is too high,
large drops will form on the end of the electrode wire, causing spatter; if the voltage is too low, the wire
will not melt.
POSITION OF MIG GUN
The angle of MIG gun to the weld has an effect on the width of the weld run.
Distance from the MIG Gun Nozzle to the Work Piece
The electrode stick out from the MIG gun nozzle should be between 2.0mm to 5.0mm when welding with
gas shielded wire. An increased distance of 5mm to 10mm is required when welding with Gasless wire. This
distance will vary depending on the type of joint that is being weld. .
Travel Speed
Speed at which a weld travels influences the width of the weld and penetration of the welding run. Welding
thin steel will have a faster travel speed than welding thick steel.
Wire Size Selection
The choice of wire size in conjunction with shielding gas used depends on:
• Thickness of the metal to be welded.
• Type of joint configuration
• Capacity of the wire feed unit and power supply.
• The amount of penetration required.
• The deposition rate required.
• The bead profile desired
• The position of welding and cost of the wire.
• Location of welding
10˚
10˚
Push
Drag
Wire Direction
ahead of bead
Push Technique
Gun Perpendicular
Drag (Pull) Technique
Wire Direction
ahead of bead
Perpendicular
Direction Of Welding