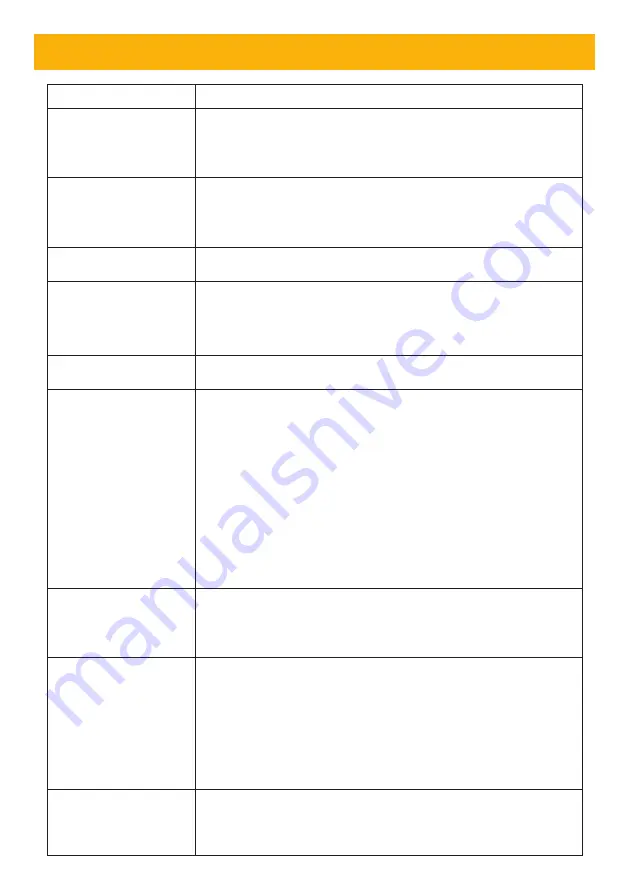
13
bossweld
.com.au
Problem
Suggested Remedy
Power indicator is not lit,
fan does not work and
no output current
1. Check that the welder is plugged into the 240V mains outlet and is
switched on.
2. Check that the mains fuse or breaker has not operated.
3. Check that the main switch on the rear of the unit is in the on position.
Power indicator is lit, fan
works, no output current
1. Check the welding cables are connected correctly.
2. Check the output connectors are not disconnected or damaged.
3. Check that the work clamp is connected securely to the work piece
and that the contact point is clean of paint or rust.
Over temperature indicator
is on, no output current
1. Duty cycle of the unit has been exceeded. Allow the unit to cool.
Output current is not
stable.
1. Check mains voltage is constant.
2. Check the welding cable connectors are tight in the sockets.
3. Check the work clamp connection to the work piece.
4. Check the welding leads are not reversed.
Excessive Spatter
1. Check that the output polarity is correct for the type of electrode or
wire being used
Porosity
(Small cavities or holes
resulting from gas
pockets in weld metal)
1. Check that the correct gas is being used
2. Check the gas is connected; check hoses, gas valve and torch are
not restricted and free of leaks. Set the gas flow between 10 - 15 l/
min flow rate. Protect the welding zone from wind and drafts
3. Remove all moisture from base metal before welding
4. Remove materials like paint, grease, oil, and dirt, including mill
scale from base metal
5. Use clean dry rust free wire. Do not lubricate the wire with oil,
grease etc.
6. Check and tighten connection.
7. Clean or replace the gas nozzle
8. Replace the gas diffuser
Wire stubbing during
welding
1. Bring the torch closer to the work and maintain stick out of
5-10mm
2. Increase the voltage
3. Decrease the wire feed speed
Lack of Fusion − failure
of weld metal to fuse
completely with base
metal or a proceeding
weld bead
1. Remove materials (paint, grease, oil, dirt, mill scale) from base metal
2. Select a higher voltage range and /or adjust the wire speed to suit
3. Keep the arc at the leading edge of the weld pool. Torch angle to
work should be between 5 & 15° Direct the arc at the weld joint
4. Adjust work angle or widen groove to access bottom during welding,
Momentarily hold arc on side walls if using weaving technique
5. Select a lower voltage range and /or adjust the wire speed to suit
Increase travel speed
Lack of Penetration
1. Select a higher voltage range and /or adjust the wire speed to suit
Reduce travel speed
2. Remove materials like paint, grease, oil, and dirt, including mill
scale from base metal
TROUBLE SHOOTING