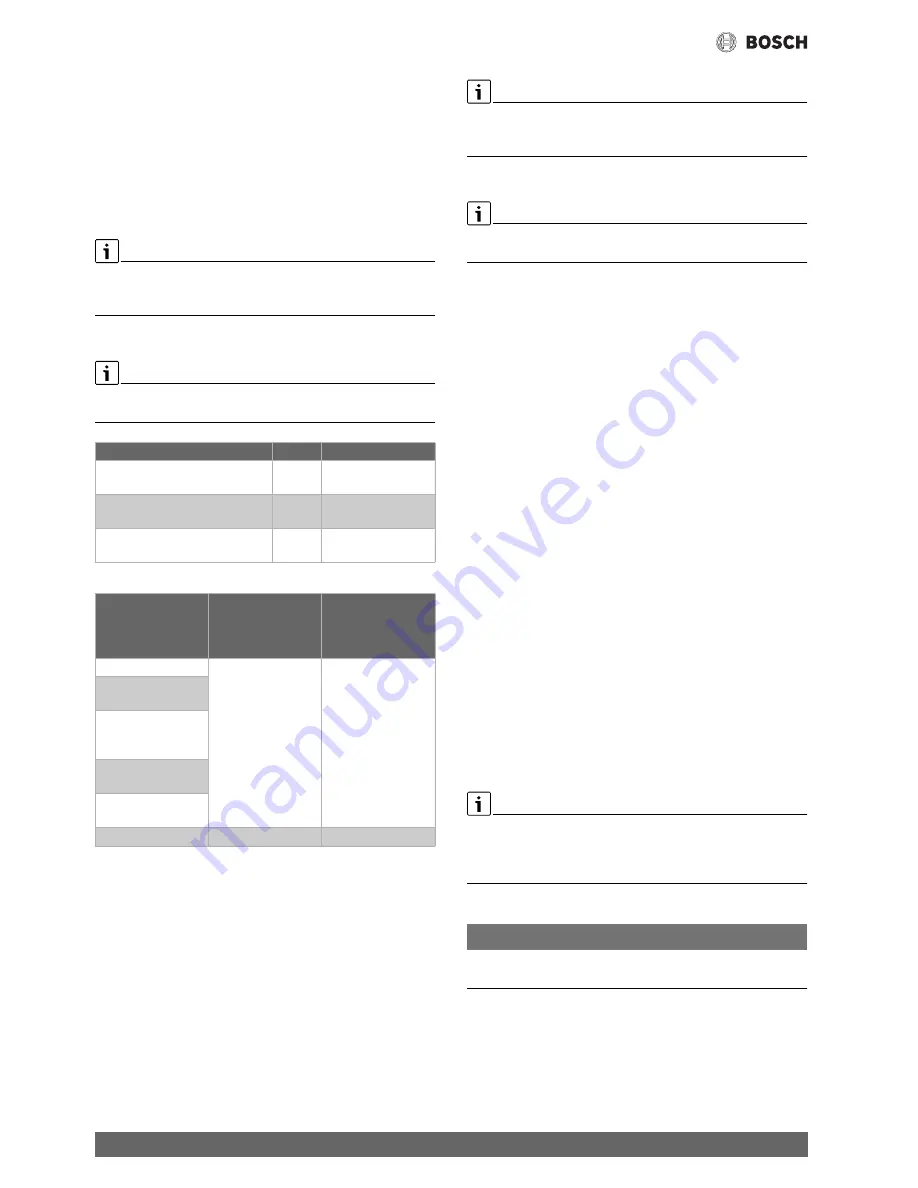
Product Information
Uni Condens 8000 F – 6720867069 (2016/10)
6
Oil burner
Oil burners used must be suitable for low sulphur fuel oil. Observe the
manufacturer's oil burner selection list and the burner manufacturer's
instructions.
Permissible fuels:
• Low-sulphur extra-light fuel oil with a sulphur content < 50 ppm and
a proportion of bio-oil (FAME) ≤ 10 %.
Existing residual amounts of fuel oil with a sulphur content ≥ 50 ppm
must be pumped out and the oil tank cleaned.
Type tested dual burners can also be used. The requirements for the gas
side and the oil side described above also apply here. All products
subsequently described apply equally for the gas side and oil side.
2.7
Operation conditions
Observe the maximum rated heat input Qn (Hi) specified on the data
plate when setting the burner output.
Table 2 Operation conditions
Table 3 Operation conditions
It must be possible to check the number of burner starts, e.g. at the user
interface, third-party control unit, building control system or burner
control unit.
2.8
Requirements for the control unit
We recommend using a control unit from the CFB 800/CFB 900 or
CC 8000 series.
The purpose of optimum control unit settings is to achieve long burner
runtimes and avoid rapid temperature changes in the boiler. Gentle
temperature changes result in a longer service life of the heating system.
The control strategy of the control unit must therefore be prevented from
becoming ineffective, i.e. through the boiler temperature controller
switching the burner on and off.
Observe the following points when selecting the control unit.
• The control unit must ensure that the maximum internal boiler water
temperature and the high limit safety cut-out are at least 5 K apart.
• It must also be ensured that the control electronics rather than the
boiler temperature controller switch the burner on and off.
• The control unit must ensure that the burner is switched to low load
before a controlled shutdown. If this is not observed, the safety shut-
off valve (SAV) in the gas train may lock out.
• Select and adjust the control unit so as to allow a gentle start-up of
the boiler with a time delay when the system is cold. The heat energy
demand must only be switched on with time delay.
• After the burner demand, an automatic timer (for example) should
limit the burner to low load for a period of approx. 150 seconds. A
restricted heat demand will prevent uncontrolled starting and
stopping of the burner.
• It must be possible to show the number of burner starts at the control
unit used (or alternatively at the burner control unit).
• The maximum number of burner starts must be monitored. There
should be a maximum of 6 burner starts per hour (averaged over
burner runtime on one day). If the number of starts is higher, the user
should be notified. The system must be checked to find out whether
the number of burner starts can be reduced. The customer service of
the manufacturer can provide assistance with optimisation of the
system.
2.9
Burner requirements
Only use specified pressure-jet gas burners with floor standing gas
condensing boilers.
Use specified pressure-jet burners or dual fuel burners for floor standing
gas/oil condensing boilers.
The boiler must be equipped with a burner that is suitable for the boiler.
NOTICE:
System damage through the use of an incorrect burner.
▶ Only use burners which meet the technical boiler requirements.
Any pressure-jet gas burner type-tested to EN 676 can be used if its
operating range matches the boiler specifications. Oil burners type-
tested to EN 267 can be used if they have been approved by the
manufacturer for low sulphur fuel oil (s < 50 ppm) and if their operating
ranges match the specification of the boiler. Only burners that have been
tested and approved for electromagnetic compatibility (EMC) may be
used.
Operation conditions
Unit
Value
Maximal permissible temperature of
high limit safety cut-out /(STB)
°C
110
Maximum operating pressure
bar
Dependent on boiler
size
Maximum number of burner starts
per
annum
15 000
Operation conditions Uni Condens 8000 F
800...1200 with
modulating
operation
Uni Condens 8000 F
800...1200 with
constant boiler
temperature
Volumetric flow rate
None –
In conjunction with a
CFB/CC control unit
for modulating
operation (CFB 840;
CFB 810; CFB 830 or
CC 8311; CC 8312).
None
In conjunction with a
CFB/CC control unit
for constant boiler
temperature CFB 810
or CC 8312, or when
supplemented by a
third party control
unit.
Min. boiler water
temperature
Operating Interruption
(complete boiler shut-
down)
Heating circuit control
unit with heating mixer
Minimum return
temperature
Miscellaneous
1)2)
1) Maximum 15,000 burner starts per year. In order not to exceed the number of
burner starts, observe the information on setting the control unit and burner in
the technical guide or installation instructions. If this value is still however
exceeded, please contact the customer service of the manufacturer.
2) The number of burner starts per year is influenced by the boiler system's
operating settings (control parameters in the boiler control and the combustion
setting) and by the design of the boiler system with regard to the consumer's
heat requirement. To avoid exceeding the number of burner starts per year as a
result of operating settings that have not been optimised, the manufacturer
offers complete commissioning and regular system inspections for boilers,
burners and boiler controls (CFB/CC controllers with function modules).
1)