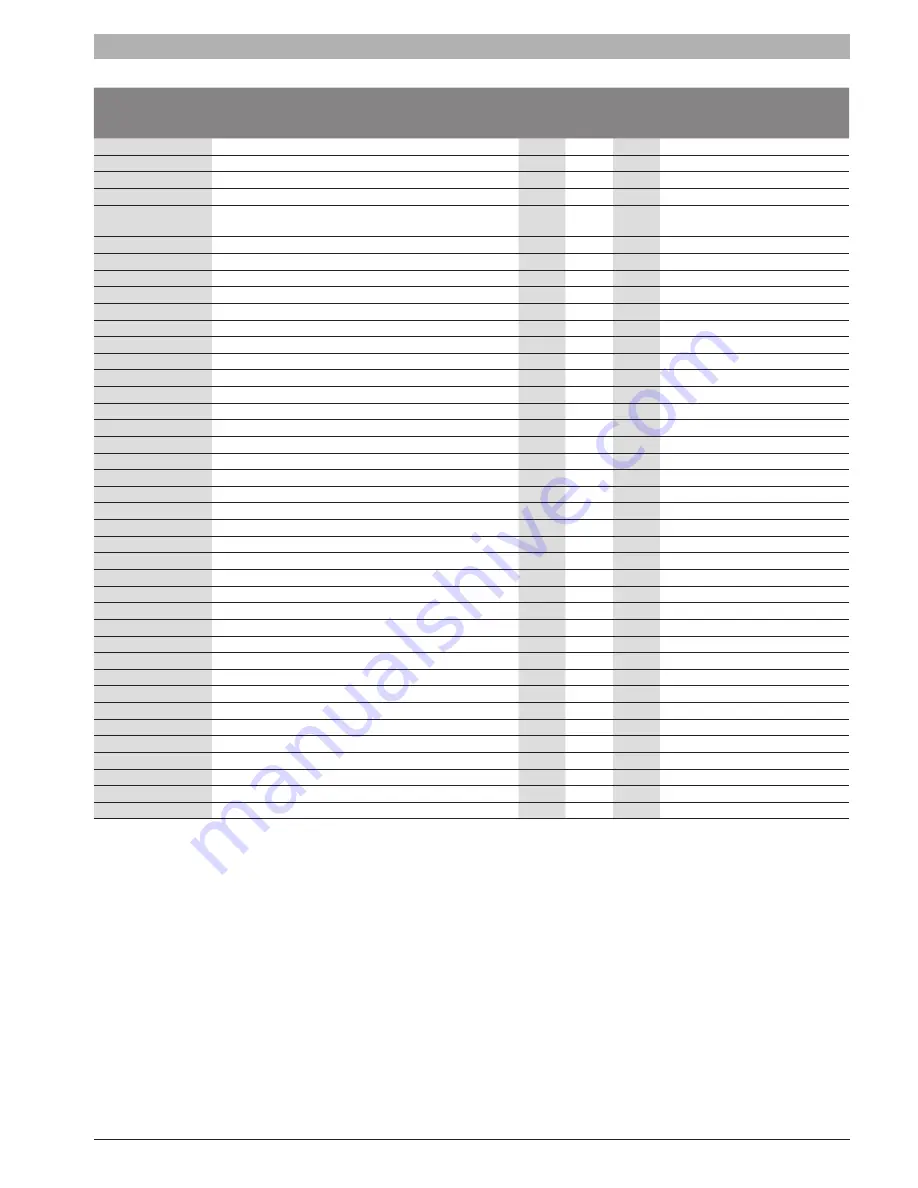
SSB
6720866940 (2017/11) US
Spare parts | 39
Item (→ Fig. 89)
Description
SSB85
SSB120
SSB160
Order number
1
High limit sensor and screws
■
■
■
7-738-004-926
2
Universal temperature detector and washer
■
■
■
7-738-004-930
3
O-ring temperature detector 0.51x0.1in 13x2.62mm
■
■
■
7-738-004-931
4
Automatic air vent 3/8"
■
■
■
7-738-005-385
5
U-clip boiler supply/return manifold 1.67x1.02in 42.5x26mm
AISI302
■
■
■
7-738-005-122
6
Boiler supply manifold
■
■
■
7-738-005-123
7
O-ring on HE connection 1.11x0.07 in 28,3x1,78 mm NBR
■
■
■
7-738-005-386
9
Boiler return manifold
■
■
■
7-738-005-387
10
Washer 3/4"
■
7-738-005-023
10
Washer 1"
■
■
7-738-005-014
11
Pump washer 1"1/2
■
■
7-738-005-388
12
Washer LWCO adapter 3/8”
■
■
■
7-738-004-929
13
LWCO probe
■
■
■
7-738-004-927
14
Boiler supply pipe 0.79in 20mm
■
■
■
7-738-005-135
15
U-clip condensate trap 1.61x0.96in 41x24.5mm AISI302
■
■
■
7-738-005-131
16
O-ring condensate trap 0.71x0.14in 18x3.53mm
■
■
■
7-738-005-129
17
Condensate trap
■
■
■
7-738-005-130
18
Condensate discharge pipe 0.71in 18mm
■
■
■
7-738-005-126
19
Boiler Return pipe 0.79in 20mm
■
7-738-005-144
19
Boiler Return pipe 0.79in 20mm
■
■
7-738-005-145
20
Pump return pipe
■
■
7-738-005-389
20
Pump return pipe
■
7-738-005-390
21
Pump UPS15/58
■
7-738-005-134
21
Pump UPS25-78
■
■
7-738-005-391
22
Adapter 1"1/2 F/ 1" M
■
■
7-738-005-392
23
PP boiler combustion pipe 1.97in 50mm
■
7-738-005-148
23
PP boiler combustion pipe 1.97in 50mm
■
7-738-005-149
23
PP boiler combustion pipe 1.97in 50mm
■
7-738-005-150
24
PP PVC vent / air intake adapter 2in/60 mm
■
■
■
7-738-005-140
25
PP Flue gas reducer 2-1.97in 60-50mm
■
■
■
7-738-005-147
26
Frame support system supply / return adapters
■
■
■
7-738-005-143
27
Flue gas temperature sensor
■
■
■
7-738-005-125
28
System return adapter 1”
■
■
■
7-738-005-141
29
System supply adapter 1”
■
■
■
7-738-005-139
30
T&P Gauge 0 – 105 psi
■
■
■
7-738-004-940
31
Safety relief valve 30psi 2.07bar
■
■
■
7-738-004-946
32
O-ring on pipe HE connection 0.79x0.12 in 20x3 mm NBR
■
■
■
7-738-005-393
33
O-ring 0.86x0.14in 21.82x3.53mm NBR
■
■
■
7-738-005-138
34
Pressure differential switch
■
■
■
7-738-005-410
35
Silicone hose for pressure differential switch
■
■
■
7-738-005-411