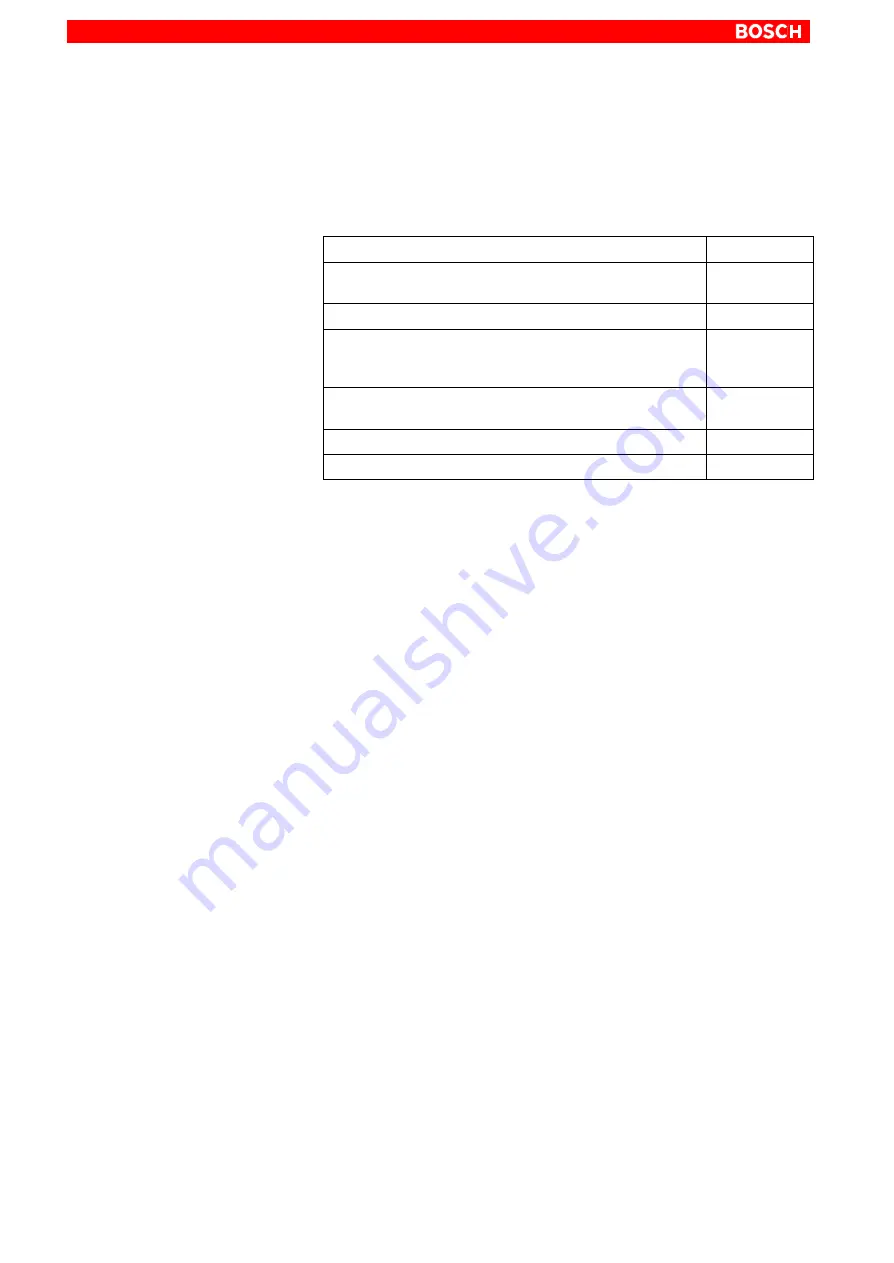
PST 6100.XXX L
8-10
1070 080 058-101 (2001.04) GB
8.9
Ordering accessories
Not
included in shipment:
Designation
Part no.
Insertable profile for pin connectors on small wire sizes, line
connection and welding transformer connection
1070 918 779
Accessories kit for PST 6100.XXX L mounting
1070 078 273
SSR 81.00 current sensor without fixing device,
in the form of a toroid coil;
55 mm internal diameter; with 5-pole sleeve terminal
1070 048 099
SSR 81.01-08 current sensor with fixing device;
e.g. for various electrode makes
on request
Mating connector for SSR 81.0X current sensor
1070 913 489
Sensor cable LiYCY 2x2x0,75 mm
2
shielded
1070 913 494
Summary of Contents for PST 6000 Series
Page 4: ......
Page 28: ...Notes on Rating 3 2 1070 080 058 101 2001 04 GB Notes ...
Page 30: ...Commissioning 4 2 1070 080 058 101 2001 04 GB Notes ...
Page 34: ...Malfunction 6 2 1070 080 058 101 2001 04 GB Notes ...
Page 36: ...Type overview 7 2 1070 080 058 101 2001 04 GB Notes ...
Page 57: ...CE declaration of conformity 10 1 1070 080 058 101 2001 04 GB 10 CE declaration of conformity ...
Page 58: ...CE declaration of conformity 10 2 1070 080 058 101 2001 04 GB Notes ...
Page 62: ...Annex A 4 1070 080 058 101 2001 04 GB ...
Page 63: ...A 1 1070 080 058 101 2001 04 GB 1070 080 058 101 2001 04 GB TI WS AT VWS Printed in Germany ...