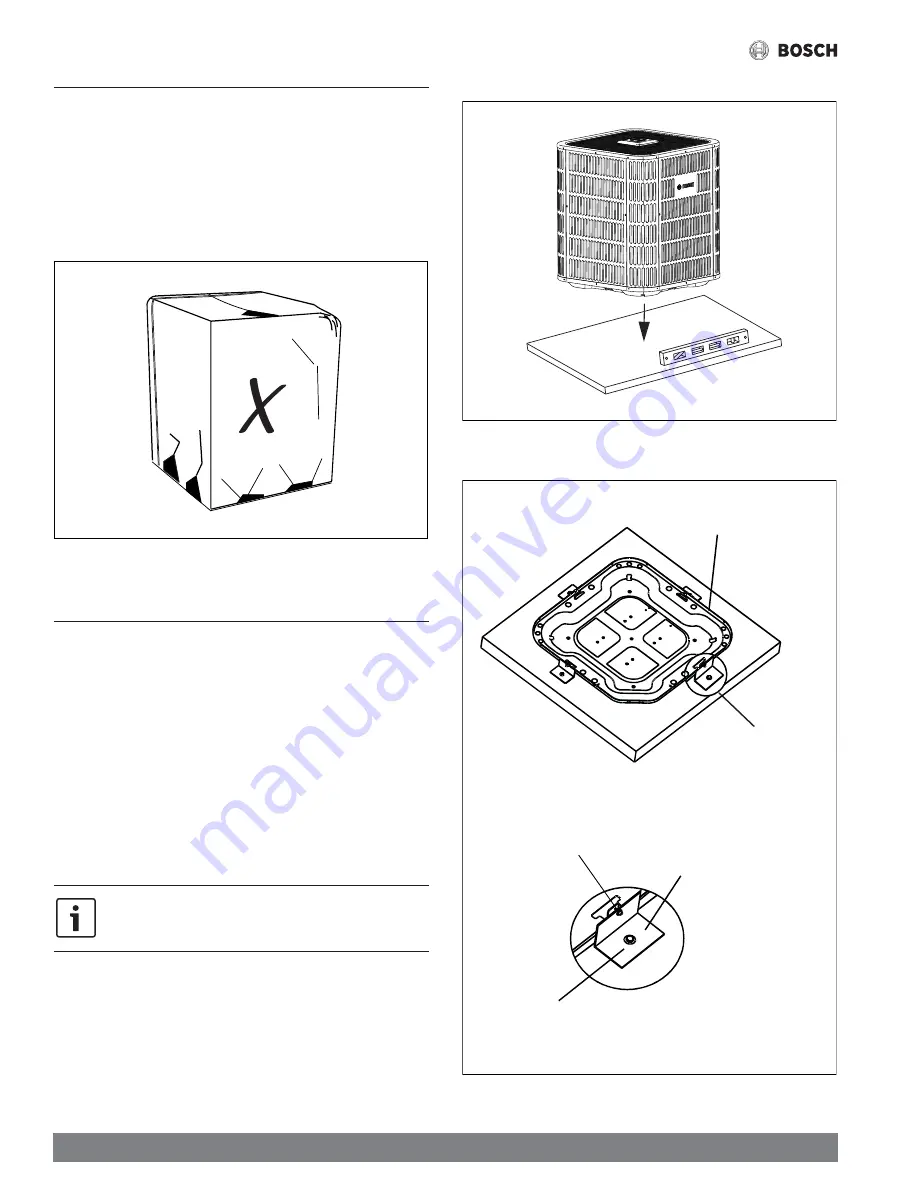
1 0
|
Installation Instructions
Bosch IDS BOVB20 Split System Heat Pump - BTC 761701316 C (02.2022)
4 Unit Preparation
4.1 Prepare the Unit for Installation
Check for damage and report promptly to the carrier any damage found to
the unit (Fig. 6).
The charge port can be used to ensure the refrigerant charge has been
retained during shipment.
Figure 7
5 Setting the Unit
5.1 Pad Installation
When installing the unit on a support pad, such as a concrete slab, consider the
following:
The pad must be at least 1-2” larger than the unit on all sides.
The pad must be separated from any structure.
The pad must be level.
The pad must be high enough above grade to allow for drainage.
The pad location must comply with National, State, and local codes.
These instructions are intended to provide a method to tie-down system
to cement slab as a securing procedure for high wind areas. Check local
codes for tie-down methods and protocols.
Figure 8
Figure 9
#7 X 3/8" Self-tapping screws
(Do not exceed 3/8" length screws!)
Detail A
See Section 2.1
for unit dimensions
See Detail A
Field-supplied brackets:
2" width, 1/16" thickness,
height as required.
1/4” Χ 1-1/2” Hex washer head concrete screws
(3/16” pilot hole needed. Pilot hole should be 1/4” deeper
than the fastener embedment)