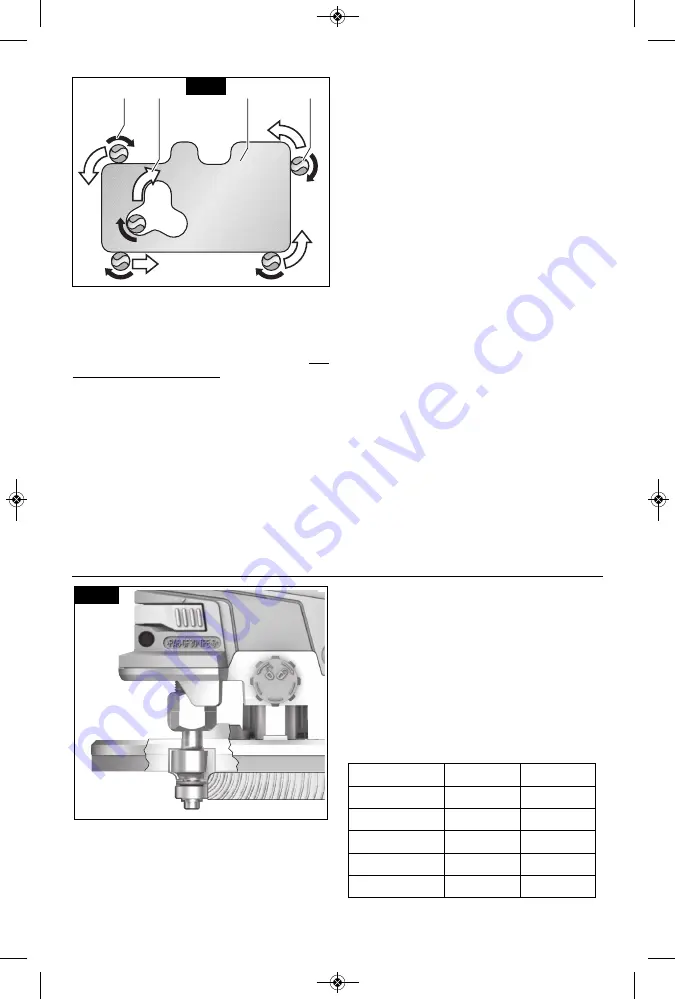
USING SELF-PILOTED BITS
Self-piloted bits have an integral round tip or
ball bearing which rides against the work
surface above or below the cutter to control
horizontal cutting depth (Fig. 12). When using
these bits, neither the roller guide or the
straight guide is required. When guiding
against a laminated surface, use wax or other
lubricant and do not apply excess pressure or
the piloted end may mar the work. Bearing
pilots must be kept clean and free of adhesive
or other residue. Router bit bearings are
sealed and permanently lubricated, and should
be replaced when they no longer turn freely to
avoid damaging the work surface.
The following maximum workpiece dimensions
apply for edge and profile routing operations:
Material
Radius
Chamfer
Hardwood
3/8” / 10mm
1/4” / 6mm
Softwood
1/2” / 12mm 3/8” / 10mm
MDF sheets
1/2” / 12mm 3/8” / 10mm
Plastic
1/2” / 12mm 3/8” / 10mm
Plywood sheets 3/8” / 10mm
1/4” / 6mm
As seen from the top of the router, the bit
17
turns clockwise (
23
) and the bit’s cutting edges
are positioned to best cut into the workpiece
21
. Therefore, the most efficient cut is made by
feeding (
22
) the router so that the bit turns into
the workpiece, not away. Figure 11 shows
proper feed for various cuts. How fast you feed
depends on the hardness of the material and
the size of the cut. For some materials, it is
best to make several cuts of increasing depth.
If the router is hard to control, heats up, runs
very slowly or leaves an imperfect cut,
consider these causes:
1. Wrong direction of feed — hard to control.
2. Feeding too fast — overloads motor.
3. Dull bit — overloads motor.
4. Cut is too large for one pass — overloads
motor.
5. Feeding too slow — leaves friction burns on
work.
Feed smoothly and steadily (do not force). You
will soon learn how the router sounds and feels
when it is working best.
Always hold the router off the workpiece 21
when turning the switch on or off. Contact
the workpiece with the router after the
router has reached full speed, and remove
it from the workpiece before turning the
switch off.
Operating in this manner will
prolong switch and motor life and will greatly
increase the quality of your work.
RATE OF FEED
When routing or doing related work in wood
and plastics, the best finishes will result if the
depth of cut and feed rate are regulated to
keep the motor operating at high speed. Feed
the router at a moderate rate. Soft materials
require a faster feed rate than hard materials.
The router may stall if improperly used or
overloaded. Reduce the feed rate to prevent
possible damage to the tool. Always be sure
the collet chuck is tightened securely before
use. Always use router bits with the shortest
cutting length necessary to produce the
desired cut. This will minimize router bit run-out
and chatter.
It may be necessary to make the cut in more
than one pass with progressively deeper
settings to avoid overloading the motor. If the
bit cuts freely and the motor does not slow
down, the cutting depth is generally correct.
FIG. 12
-12-
17
21
22
23
FIG. 11
160992A400_GKF12V-25 10/9/17 2:58 PM Page 12