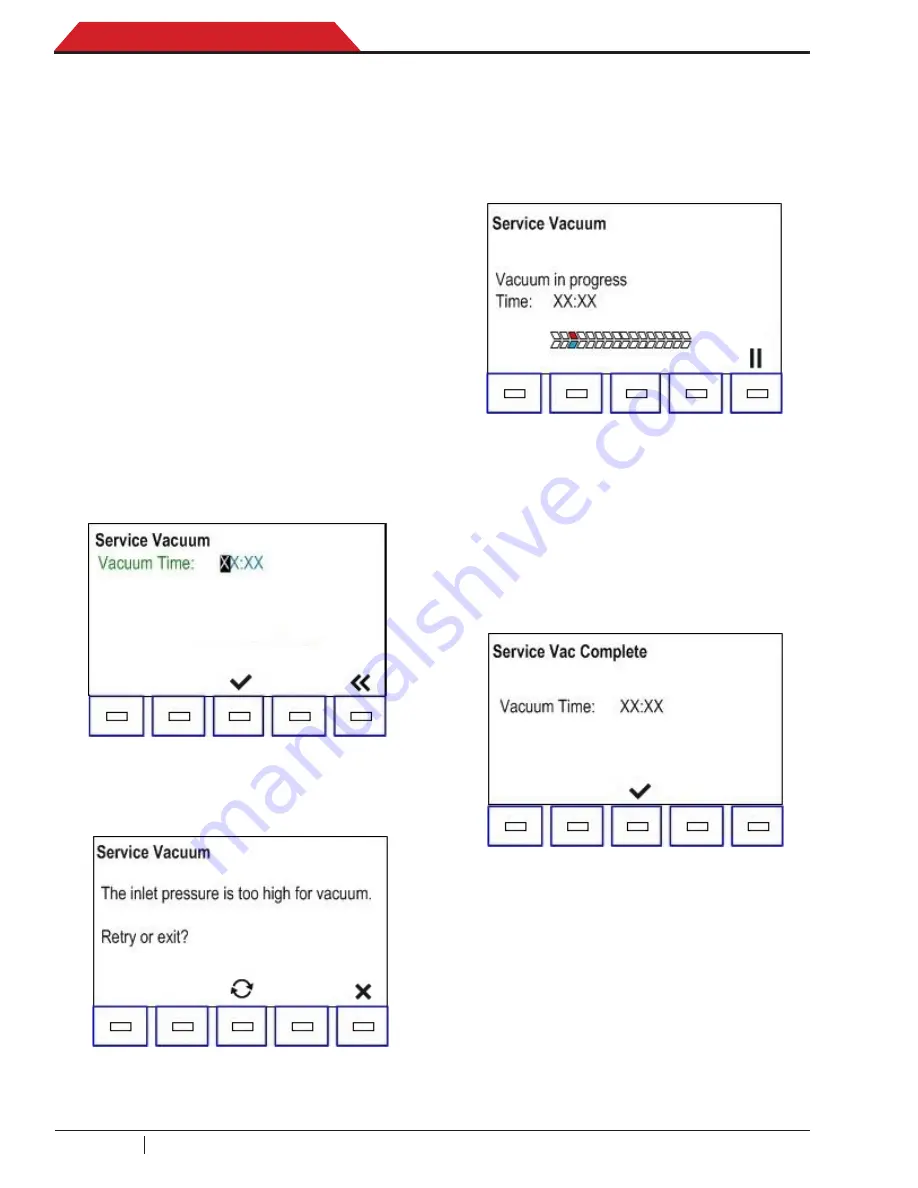
ACS 753, ACS 763, ACS 863 Service Manual
SP00D00609
2018-03-26
Robert Bosch GmbH
34
Diagnostics and Testing
4. Select
RETRY
icon to repeat, or
ESC
icon
to return to the Service Menu.
Service Vacuum
Service vacuum is a manually operated test
used to pull a vacuum on the machine to
remove air from the manifold and ISV prior to
refilling the ISV after service.
1. From the Service Menu, scroll to
Calibrate
air flow
.
2. Select
OK
icon. The following displays:
3. Enter a new time using the keypad and
select
OK
icon to begin the vacuum. If
the pressure is greater than 0.35 bar, this
screen displays:
5. If Ok unit come back to service menu.
6. If failed unit ask to retry.
A/C unit internal clearing
The A/C unit internal clearing is used to
evacuate service hoses, distillator and dryer
filter (after compressor discharge pressure is
still in). Components ON:
1. LS inlet Solenoid S4.
2. HS Inlet Solenoid S5.
3. Recover Solenoid S11.
4. Compressor.
5. The vacuum pump should turn on and the
time begins to count down (5 minutes).
To pause at any point during the process
select
PAUSE
icon. At the Pause function,
the Service Vacuum can either be resumed
or cancelled.
7. Select
OK
icon to return to the Service
Menu.
The inlet pressure should stay below 0.35 bar
throughout the Service Vacuum. The Vacuum
Pump, Vacuum Solenoid, HS Charge Solenoid,
Oil Return Solenoid, LS Inlet Solenoid, Tank
Liquid Solenoid and Recover Solenoid will turn
ON during this test.
6. When the vacuum Time Remaining falls
to 00.00, the outputs will turn OFF and the
following displays: