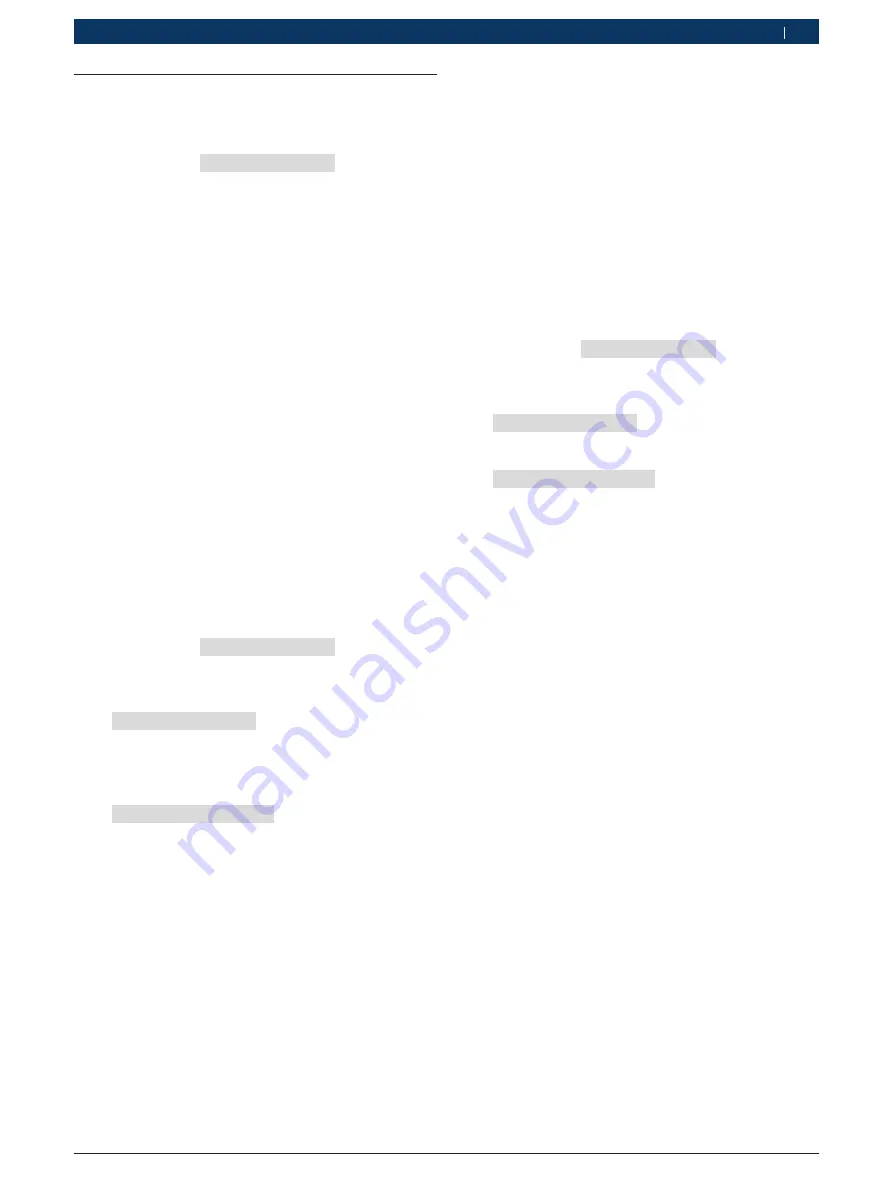
1 689 975 252
2019-05-15
|
Robert Bosch GmbH
Calibration | ACS 511 | 33
en
13.5 Pressure sensor
13.5.1 Checking the adjustment
1.
Call up the start screen.
2.
Press <
3
> and <
Flush
> simultaneously and release.
The message
ENTER CODE 0000
is displayed.
3.
Enter
1515
and confirm with
E
.
4.
Select
"
INPUTS TEST
" with
o
u
and confirm with
E
.
The absolute values of the scales and of the pres-
sure sensor is displayed.
5.
Remove the service hoses on the ACS 511 and open
the HP and LP valves on the front panel so that the
pressure sensor is subjected to the atmospheric
pressure.
6.
Check that the pressure value read is between 0.900
and 1.100 bar (the typical value is 1.000 bar).
13.5.2 Adjusting the pressure sensor
i
The pressure sensor is adjusted on the control PCB
using the simulator, as the pressure sensor has been
officially calibrated in the factory.
i
Pressure sensor 0 bar / 16 bar absolute
-1 bar / +15 bar relative.
1.
Disconnect the pressure sensor from the control PCB.
2.
Connect the simulator to the control PCB.
3.
Connect a multimeter to the simulator.
4.
Call up the start screen.
5.
Press <
3
> and <
Flush
> simultaneously and release.
The message
ENTER CODE 0000
is displayed.
6.
Enter
1111
and confirm with
E
.
7.
Select
"
PRES. CALIBRATION
" with
o
u
and con-
firm with
E
.
ZERO CALIBRATION
is displayed.
8.
Turn the potentiometer on the simulator until a volt-
age of 0 V is displayed.
9.
Enter the value 0.000 on the keypad and confirm
with
E
.
WEIGHT CALIBRATION
is displayed.
10.
Turn the potentiometer on the simulator until a
voltage of 3.00 V is displayed.
11.
Enter the value 4.800 on the keypad and confirm
with
E
.
The menu containing the functions appears on
the display again.
12.
Remove the simulator and re-connect the pressure
sensor.
i
Return with <
Stop
>.
i
If the simulator is not available, a simplified adjust-
ment can be performed. This process definitely guar-
antees that the ACS 511 will function perfectly.
1.
Turn on the ACS 511.
2.
Open the HP and LP valves on the display and con-
trol panel.
3.
Start the vacuum function and maintain the vacuum
in the hoses for 5 minutes (this subjects the pres-
sure sensor to a vacuum).
4.
After 5 minutes, stop the vacuum function and check
on the pressure gages that there are no leaks.
5.
Call up the start screen.
6.
Press <
3
> and <
Flush
> simultaneously and release.
The message
ENTER CODE 0000
is displayed.
7.
Enter
1111
and confirm with
E
.
8.
Select
"
PRESSURE CALIBRATION
" and confirm
with
E
.
ZERO CALIBRATION
is displayed.
9.
Enter the value 0.000 on the keypad and confirm
with
E
.
WEIGHT CALIBRATION
is displayed.
10.
Detach the service hoses and set the pressure sen-
sor to atmospheric pressure.
11.
Enter the value 1.000 on the keypad and confirm
with
E
.
The menu containing the functions appears on
the display again.
i
Return with <
Stop
>.
12.
Perform the adjustment check described above
(see section 13.5.1).