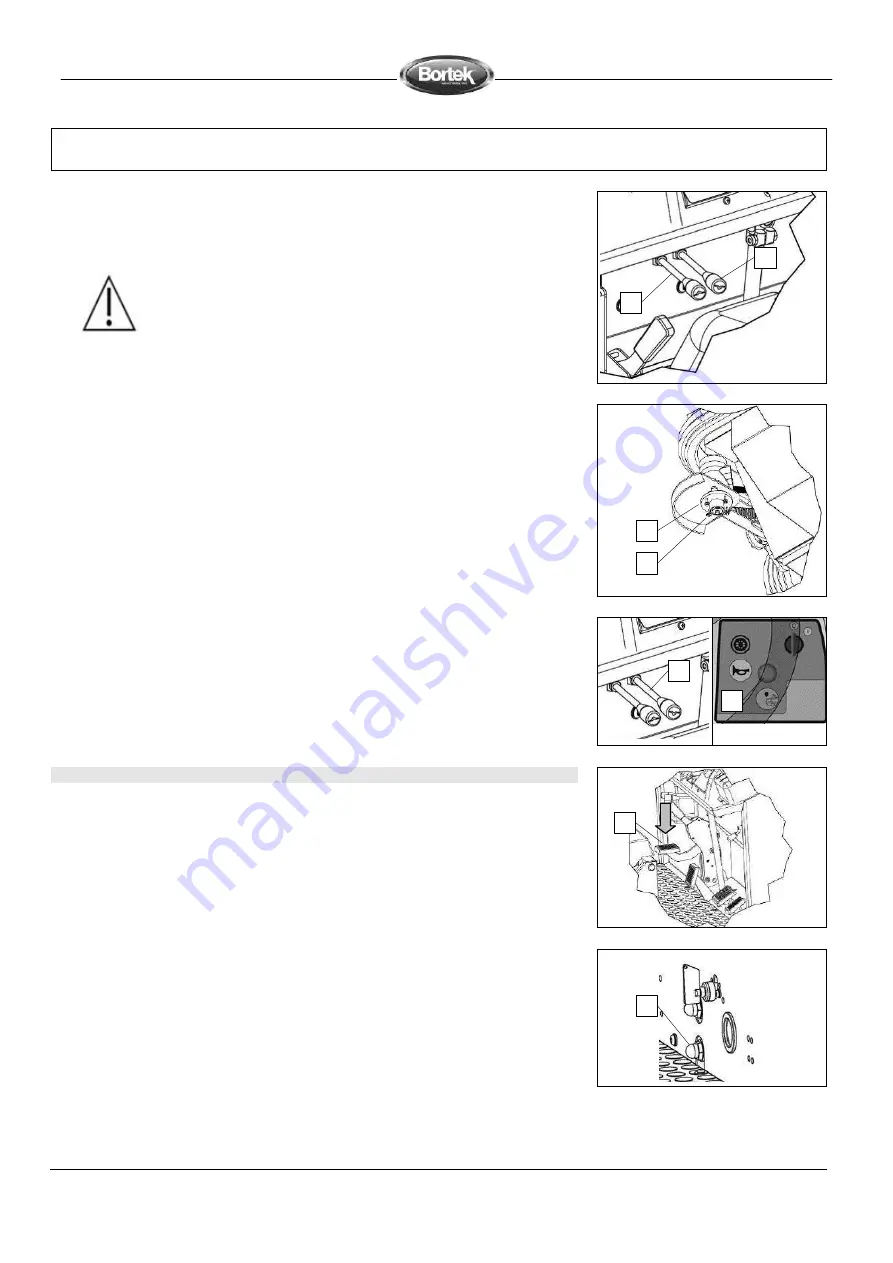
30
MACHINE PREPARATION
3.
Turn the main machine switch to the “ON” position, turn it by a quarter rotation to the right
4.
Make sure that the hopper hatch is closed, if this is not the case not pull the lever (3) upwards
5.
Raise the hopper to its maximum height, pulling the lever (4) up, engage the safety catches supplied
with the machine
WARNING!
The safety catches, supplied with the machine, should be inserted into
the shafts of the pistons controlling the raising of the hopper.
6.
Check the main machine switch is in the “OFF” position, and if this is not the case, turn it by a quarter
rotation to the left
7.
With the proper equipment, remove the screws (5) in the side brush hub
8.
Insert the side brush into the brush hub (6)
9.
With the proper equipment, fix the side brush to the brush hub (6) using the screws (5)
10.
Remove the safety catches
11.
Turn the main machine switch to the “ON” position, turn it by a quarter rotation to the right
12.
Lower the hopper until it is in the work position, pulling the lever (4) downwards, while at the same
time pushing the dead man's button (7) on the instrument panel
36.
CHECKING THE HYDRAULIC SYSTEM OIL
This machine is equipped with a hydraulic system. To ensure optimum machine performance, check the oil
level in the following way:
1.
Block the machine by engaging the parking brake, pressing the pedal (1) down
2.
Check the main machine switch is in the “OFF” position, and if this is not the case, turn it by a quarter
rotation to the left
3.
Check the oil is not below the minimum level, as seen on the transparent cap (2). If necessary, add
more oil by following the instructions in the “MAINTAINING THE HYDRAULIC OIL LEVEL” chapter.
4
3
1
2
4
7
6
5