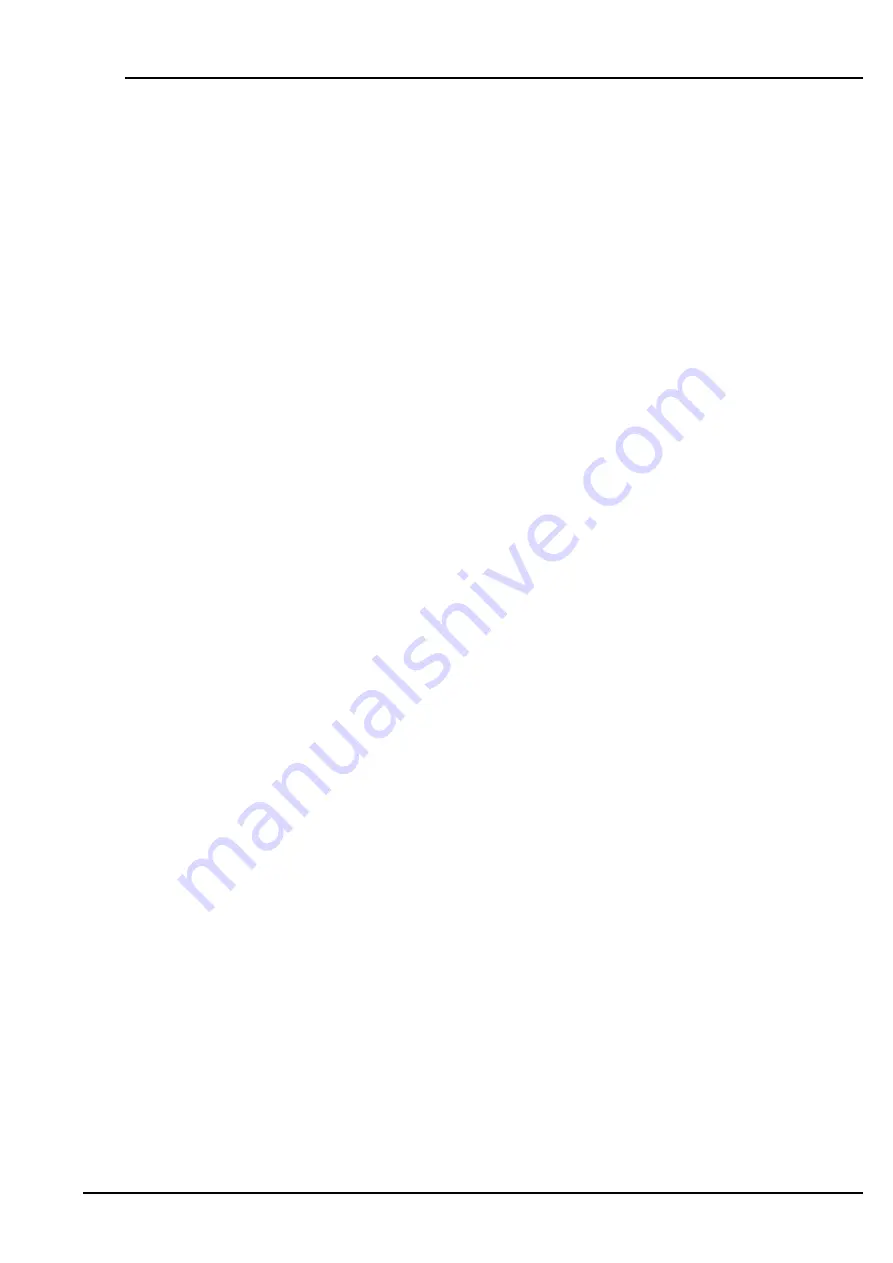
ATTEXOR Clinch Systems SA
User manual
Copyright © 2010 by Bollhoff Attexor S.A. Page 26
The tables from chapter “Tooling selection and joint optimization" only give indicative
values that facilitate the first choice of parameters. Tests on samples are necessary
and so are tests on the real products. It may be necessary to carry out tests with
other tools or opting for other St values than those indicated in the tables.
Quality control
Ref. Tables chapter “Tooling selection and joint optimization".
It is common practice for production control to check the St value at regular interval
during the production process. This is a simple, non-destructive quality control
operation and a deviating St value will signal malfunction of the machine or the tool
kit, changes in the sheet material, non-appropriate handling by the operator or
shortcomings in the air supply.
Alternatively or as a complement to St value, the diameter D
1
of the button (or W
1
for
a rectangular point) can be a good quality control value, despite it is less accurate
than St. in case of using this measurement (D
1
or W
1
) it is necessary to determine
the reference value specific to the application and note it down in this manual.
Samples can be produced at regular intervals, make a cut on the joint and check by
a microscope that the button locking and neck are unchanged compared to the
reference sample
The tooling (punch and die) must be checked at regular intervals. Criteria for tool
changes are:
•
Visible cracks or chipped zone on the punch tip, on the die parts, on the anvil
•
Punch diameter loss exceeding 0.1mm
•
Die spring damaged (can be replaced)
•
Die cage damaged or deformed in such a way that the die blades do not move
properly