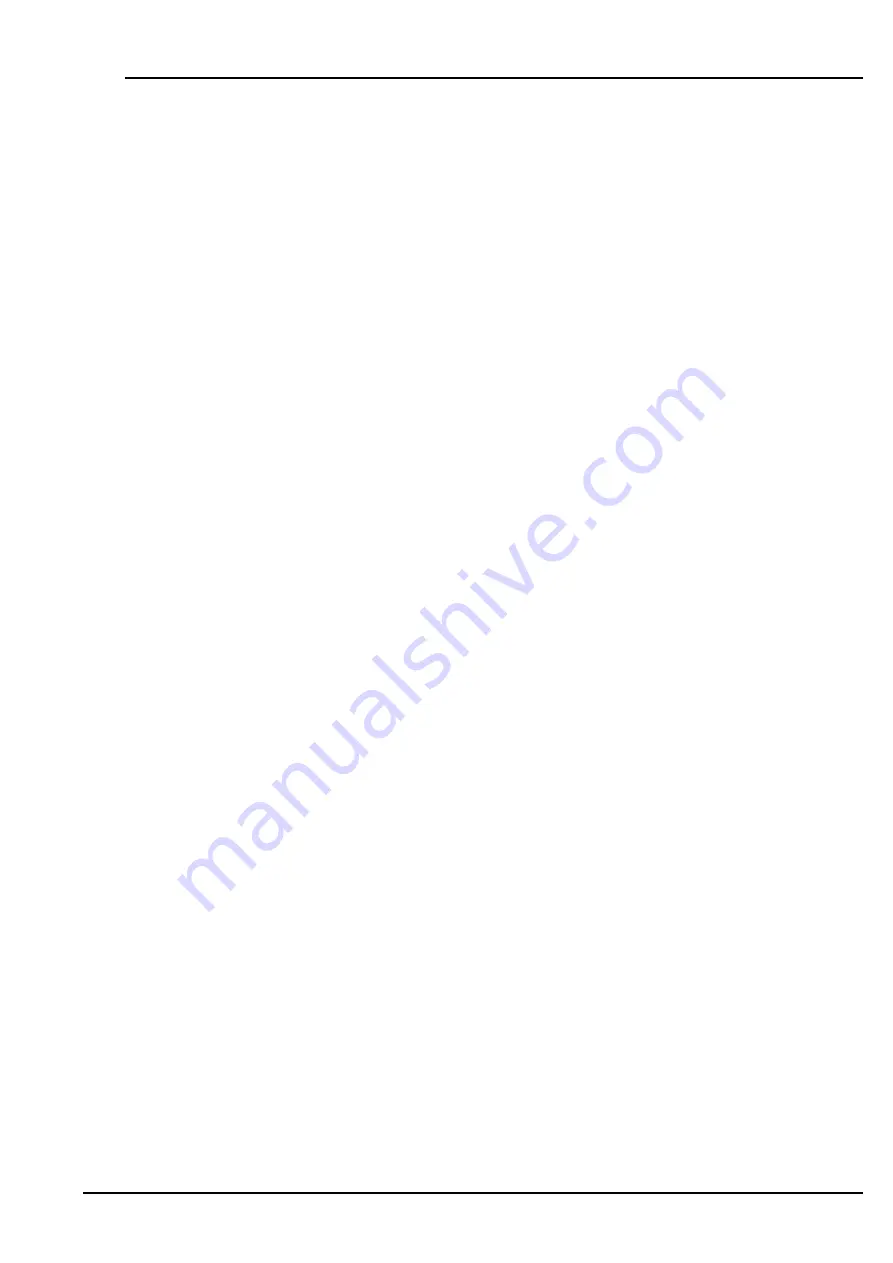
ATTEXOR Clinch Systems SA
User manual
Copyright © 2010 by Bollhoff Attexor S.A. Page 12
Clinching system, end-of-stroke control
Ref. Fig. 2
The force required for a clinching is furnished by a hydraulic piston, fitted in the jaw (A1).
The hydraulic pressure is generated by an oil/air pressure intensifier, booster (C1). Ref. fig.
10, with a compression ratio of 60:1.
The trig and the duration of the cycle are controlled by the trigger (B1) which activates the
main pneumatic valve under the booster cover (C1).
The activation of the booster is only possible by a pneumatic signal given to it.
If this equipment is integrated in an automatic line, the emergency stop of the line must stop
this equipment by switching off the power source.
The clinching process is governed by the end-of-stroke position of the piston, which
determines the final position of the punch and the joint parameter St. This means that the
squeezing of the clinch joint is stable, independent on the pressure set on the regulator
(E2), provided that the set pressure is superior to the minimum required pressure for getting
the joint done. The internal end stop (A8) of the piston can be adjusted and serves not only
as a protection of the tool kit in case of activation without material, but mainly for setting the
optimal joint parameters in regard to the sheet metal to be joined and the selected tool kit.
Refer to chapter “Tooling selection and joint optimization” and Fig. 7 for instructions
about adjusting the end stop.