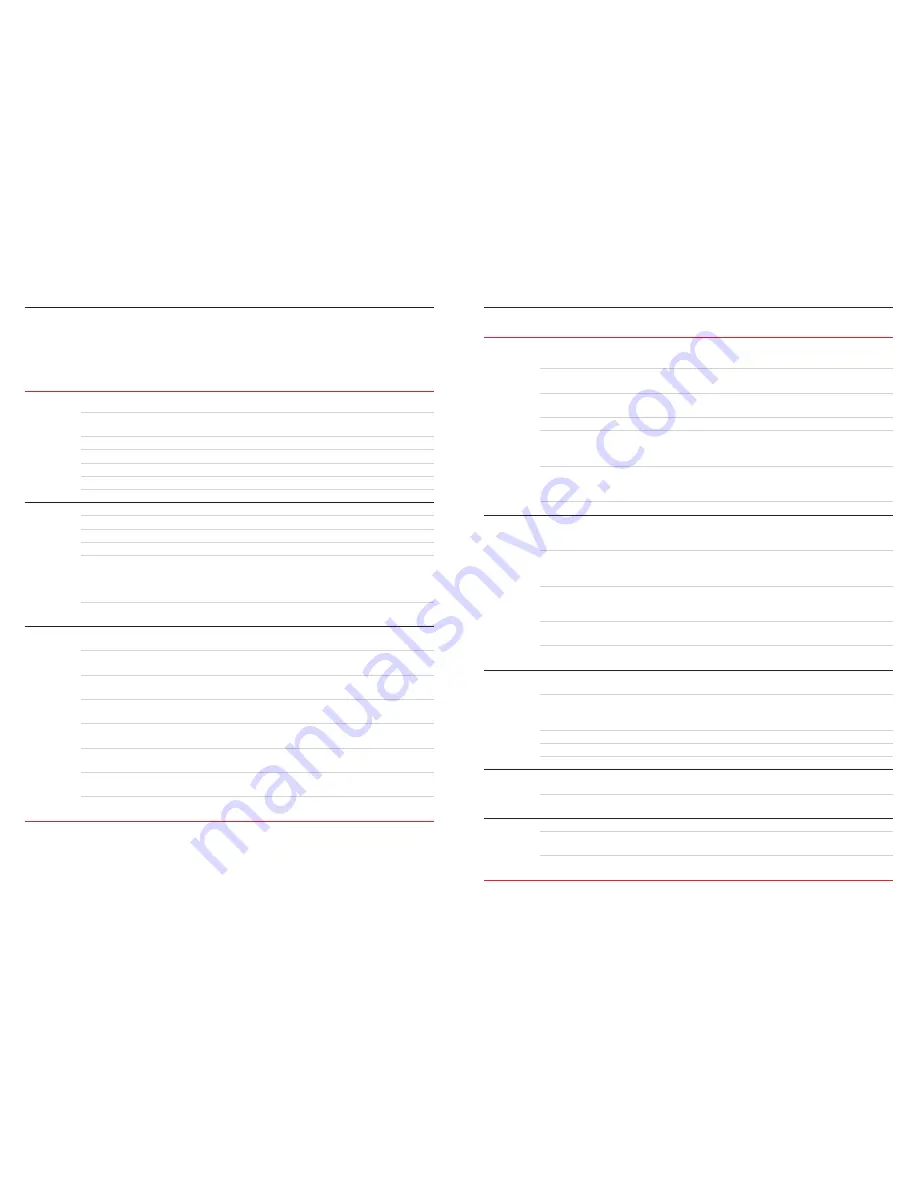
Problem
Cause
Solution
Excessive
electrode
consumption
Inadequate gas flow
Increase gas flow
Improper size electrode for
current required
Use larger electrode
Operating of reverse polarity
User larger electrode or change polarity
Electrode contamination
Remove contaminated portion, then prepare again
Excessive heating inside torch
Replace collet. Try wedge collet or reverse collet
Electrode oxidising during cooling
Increase downslope
Shield gas incorrect
Change to Argon (no oxygen or CO
2
)
Erratic arc
Incorrect voltage (arc too long)
Maintain short arc length
Current too low for electrode size
Use smaller electrode or increase current
Electrode contaminated
Remove contaminated portion, then prepare again
Joint too narrow
Open joint groove
Contaminated shield gas.
Dark stains on the electrode or
weld bead indicate contamination
The most common cause is moisture or aspirated
air in gas stream. Use welding grade gas only.
Find the source of the contamination and eliminate
it promptly
Base metal is oxidised, dirty or oily
Use appropriate chemical cleaners, wire brush,
or abrasives prior to welding
Inclusion
of tungsten
or oxides
in weld
Poor scratch starting technique
Many codes do not allow scratch starts. Use copper
strike plate. Use high frequency arc starter
Excessive current for tungsten
size used
Reduce the current or use larger electrode
Accidental contact of electrode
with puddle
Maintain proper arc length
Accidental contact of electrode
to filler rod
Maintain a distance between electrode and filler
metal
Using excessive electrode
extension
Reduce the electrode extension to
recommended limits
Inadequate shielding or
excessive drafts
Increase gas flow, shield arc from wind,
or use gas lens
Wrong gas
Do not use ArO
2
or ArCO
2
GMAW (MIG) gases for
TIG welding
Heavy surface oxides not
being removed
Use wire brush and clean the weld joint prior
to welding
Problem
Cause
Solution
Porosity
in weld
deposit
Entrapped impurities, hydrogen,
air, nitrogen, water vapour
Do not weld on wet material. Remove condensation
from line with adequate gas pre-flow time
Defective gas hose or
loose connection
Check hoses and connections for leaks
Filler material is damp
(particularly aluminium)
Dry filler metal in oven prior to welding
Filler material is oily or dusty
Replace filler metal
Alloy impurities in the base metal
such as sulphur, phosphorous,
lead and zinc
Change to a different alloy composition which
is weldable. These impurities can cause a tendency
to crack when hot
Excessive travel speed with rapid
freezing of weld trapping gases
before they escape
Lower the travel speed
Contaminated shield gas
Replace the shielding gas
Cracking
in welds
Hot cracking in heavy section or
with metals which are hot shorts
Preheat. Increase weld bead cross-section size.
Change weld bead contour. Use metal with fewer
alloy impurities
Crater cracks due to improperly
breaking the arc or terminating the
weld at the joint edge
Reverse direction and weld back into previous
weld at edge. Use Amprak or foot control to
manually down slope current
Post weld cold cracking due to
excessive joint restraint, rapid cooling
or hydrogen embrittlement
Preheat prior to welding. Use pure or non-
contaminated gas. Increase the bead size. Prevent
craters or notches. Change the weld joint design
Centreline cracks in single
pass weld
Increase bead size. Decrease root opening.
Use preheat. Prevent craters
Underbead cracking from
brittle microstructure
Eliminate sources of hydrogen, joint restraint
and use preheat
Inadequate
shielding
Gas flow blockage or leak in
hoses or torch
Locate and eliminate the blockage or leak
Excessive travel speed exposes
molten weld to atmospheric
contamination
Use slower travel speed or carefully increase the
flow rate to a safe level below creating excessive
turbulence. Use a trailing shield cup
Wind or drafts
Set up screens around the weld area
Excessive electrode stickout
Reduce electrode stickout. Use a larger size cup
Excessive turbulence in gas stream
Change to gas safer parts or gas lens parts
Arc blow
Induced magnetic field from
DC weld current
Rearrange the split ground connection
Arc is unstable due to
magnetic influence
Reduce weld current and use arc length as short
as possible
Short
parts life
Cup shattering or cracking in use
Change cup size or type. Change tungsten position
Short collet life
Ordinary style is split and twists or jams
Change to wedge style
Short torch head life
Do not operate beyond rated capacity. Use water
cooled model. Do not bend rigid torches
6.0 Troubleshooting guide
BOC Smootharc TIG 185 Operating Manual
24
25
BOC Smootharc TIG 185 Operating Manual