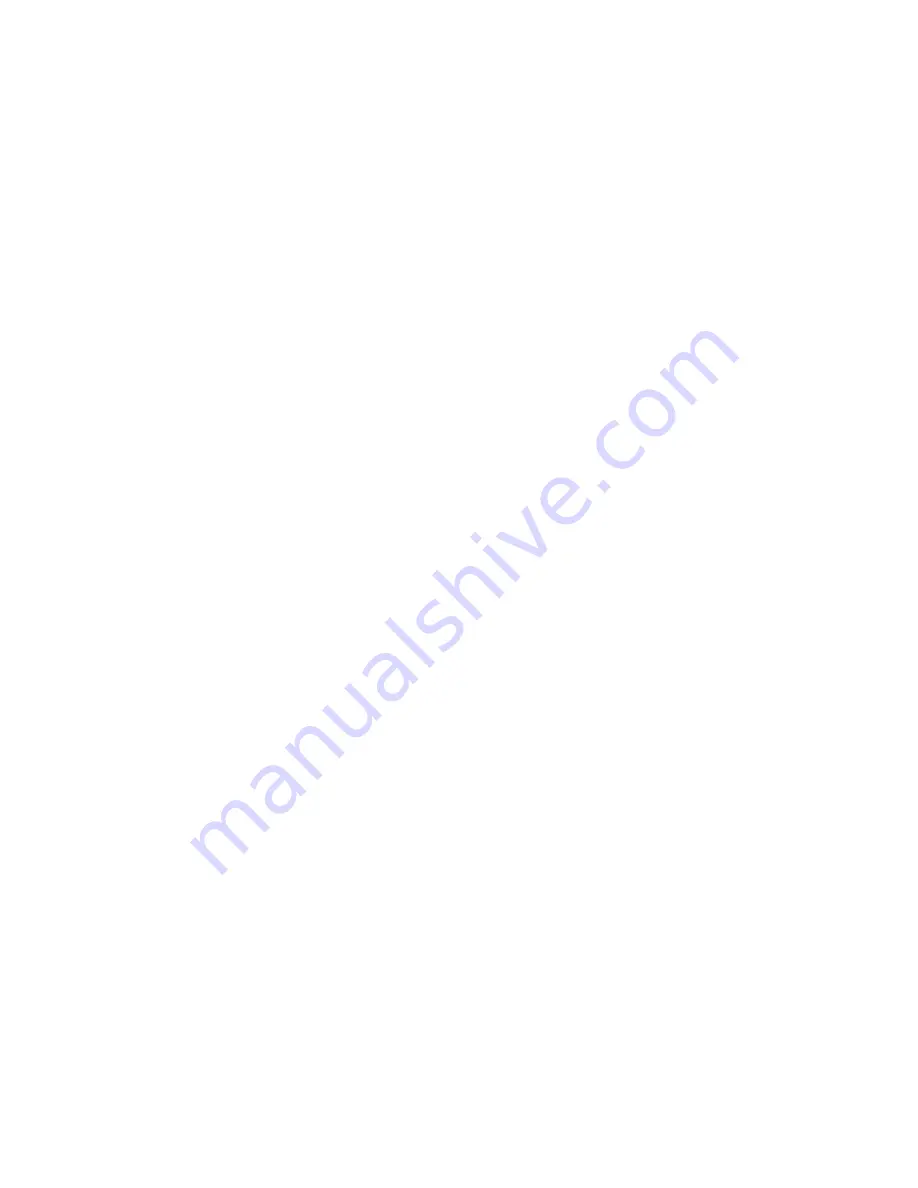
3.0 Gas Tungsten Arc Welding
(TIG) Principle
Gas Tungsten Arc Welding (GTAW) utilises
the heat of an arc that is formed between a
non-consumable tungsten electrode and the
workpiece to fuse the joint material. The arc
area is shrouded in inert gas that protects the
weld pool and the electrode from contamination
while allowing a stable arc to be maintained.
TIG welding applications
• light fabrication
• general engineering
• welds most metals, particularly stainless steel
and other non-ferrous metals
3.1 Equipment Requirements
The basic requirements for the GTAW
process are:
• a welding power source
• TIG torch
• a gas supply system
TIG power sources may have an alternating or
direct current output, and depending on the
application and provision for controlling the gas
flow, initiating the arc is usually required. The
BOC Inverweld has a direct current output.
The torch design will depend on the application
but it is required to provide a uniform shield or
inert gas and is often water cooled to reduce
size and protect the operator.
Equipment set-up
• Install the welding machine as near as possible
to the mains power to keep the primary
power cable short. The primary power cable
carries dangerously high voltages.
• Inspect all cables for damage
• Use welding cables that are fully insulated
• Make sure the electrode holder is insulated
from the bench. Hang it on an insulated hook
• Switch off when not in use
3.2 Modes of Operation
The process may be operated in one of the
following modes
• DC electrode negative
• DC electrode positive
DC electrode negative
In this mode the electrode remains relatively
cool whilst the workpiece is effectively heated.
(The normal estimate of heat distribution in the
GTAW process is 1/3 at the negative (cathode)
and 2/3rds at the positive (anode). This is the
most common mode of operation for ferrous
materials, copper, nickel and titanium alloys.
DC electrode positive
With DC electrode positive there is a tendency
for the electrode to overheat and fusion, of the
workpiece is poor. The advantage of this mode
of operation is the cathodic cleaning effect that
removes the tenacious oxide film from the
surface of aluminium alloys.
9
3. Gas Tungsten Arc Welding (GTAW)