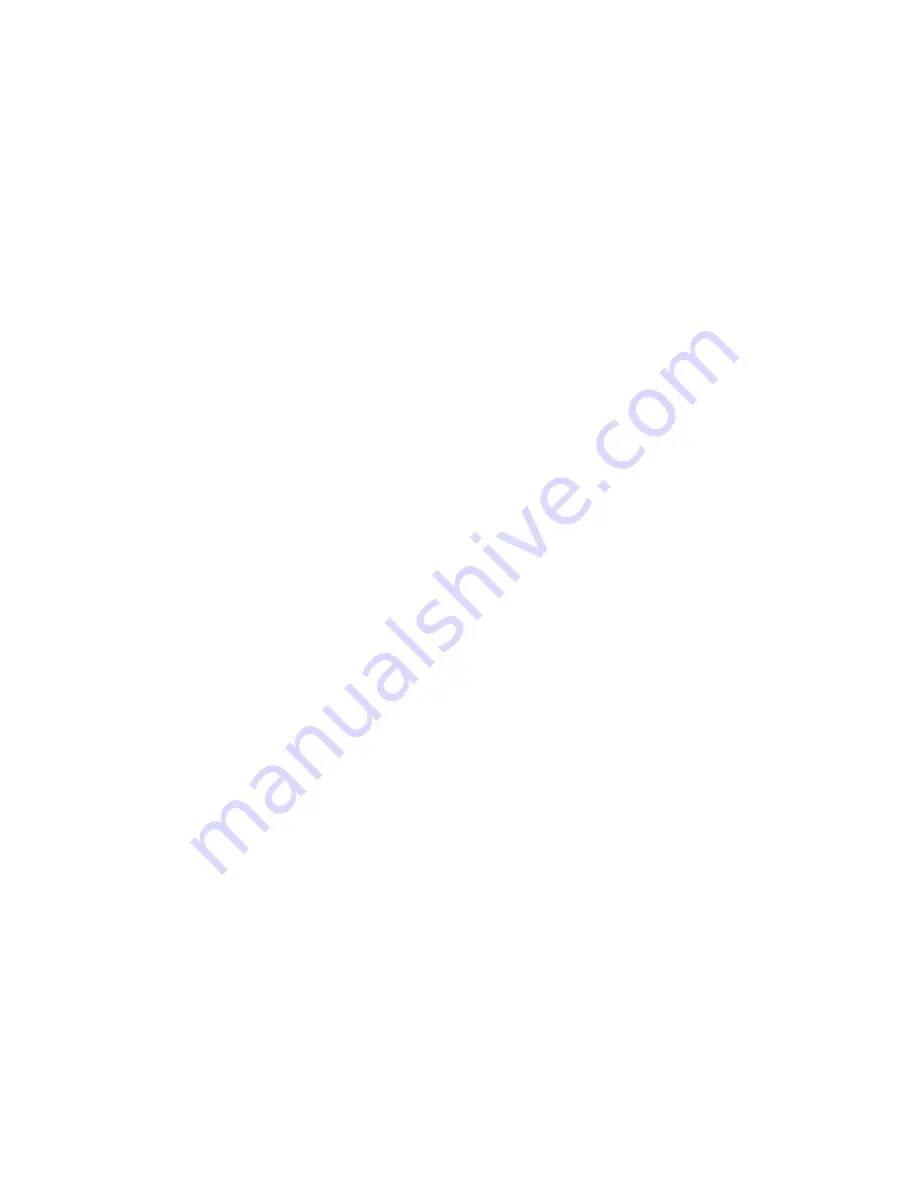
2.2 Control of the Process
The main control parameters for the MMA
process are:
• current and
• operator technique
The current range is determined by the
electrode type and size. Deposition rate
increases with current for a given electrode
diameter but the maximum current is limited by
the coating material and the ability to control
both the weld pool and the molten slag.
Increasing the current also increases the level of
fume and the arc radiation. A high level of manual
dexterity is required to coordinate the movement
of the electrode to match the burn-off rate and
maintain a constant arc length. Some electrodes
are designed for 'touch' or contact welding (the
electrode coating rests on the workpiece during
welding) and this simplifies the production of
fillet welds. Additional skills are required to
control fusion characteristics and bead profile
(electrode angle, travel speed and weave patterns
must be carefully chosen), particularly for
positional welding.
2.3 Features of the Process
The most important characteristic of the
MMAW process is its overall flexibility. The wide
range of electrode types allows the weld metal
to be matched to the application, which may be
particularly useful in repair and jobbing shop
environments. Relatively simple equipment is
required and the capital cost is low.
The quality of the welded joint depends almost
entirely on the welder, and availability of
suitably qualified welders may cause production
bottlenecks. In addition the process is
intermittent, as the electrode must be changed
at regular intervals, placing a natural limit on the
productivity of the process.
2.4 Applications of MMA Welding
The process is applied widely in the fabrication
and repair of plain carbon and low alloy steels.
It has been used in the construction of power
stations, pipelines and offshore structures.
Stainless steel, inconel, nickel and a wide
range of surfacing electrodes are available, and
these may be used in low volume production,
maintenance and repair situations.
2.5 MMA Electrode
Characteristics
The characteristics of the MMAW process are
largely determined by the electrode coating
material that controls the following important
features:
Arc
Certain chemicals may be added to the coating
material to stabilise the arc (e.g. rutile or potassium
silicate), improve metal transfer and reduce spatter.
These additions also provide a useful reduction
in the operating voltage required for the electrode.
Shielding
Shielding is provided by gases generated by the
decomposition of constituents such as calcium
carbonate or cellulose and by liquid slags which
protect the weld pool surface.
Weld pool control
The slag fluidity is usually the factor that
determines the ease of positional welding. Rapidly
freezing slags may be used to provide support
for the weld pool in vertical and overhead welding.
Alloying
The coating material can provide a useful source
of alloying elements or additions that control the
weld metal chemistry (such as deoxidisers). This
enables a wide range of weld metal properties to
be achieved by modifying the coating whilst using
a standard core wire.
7