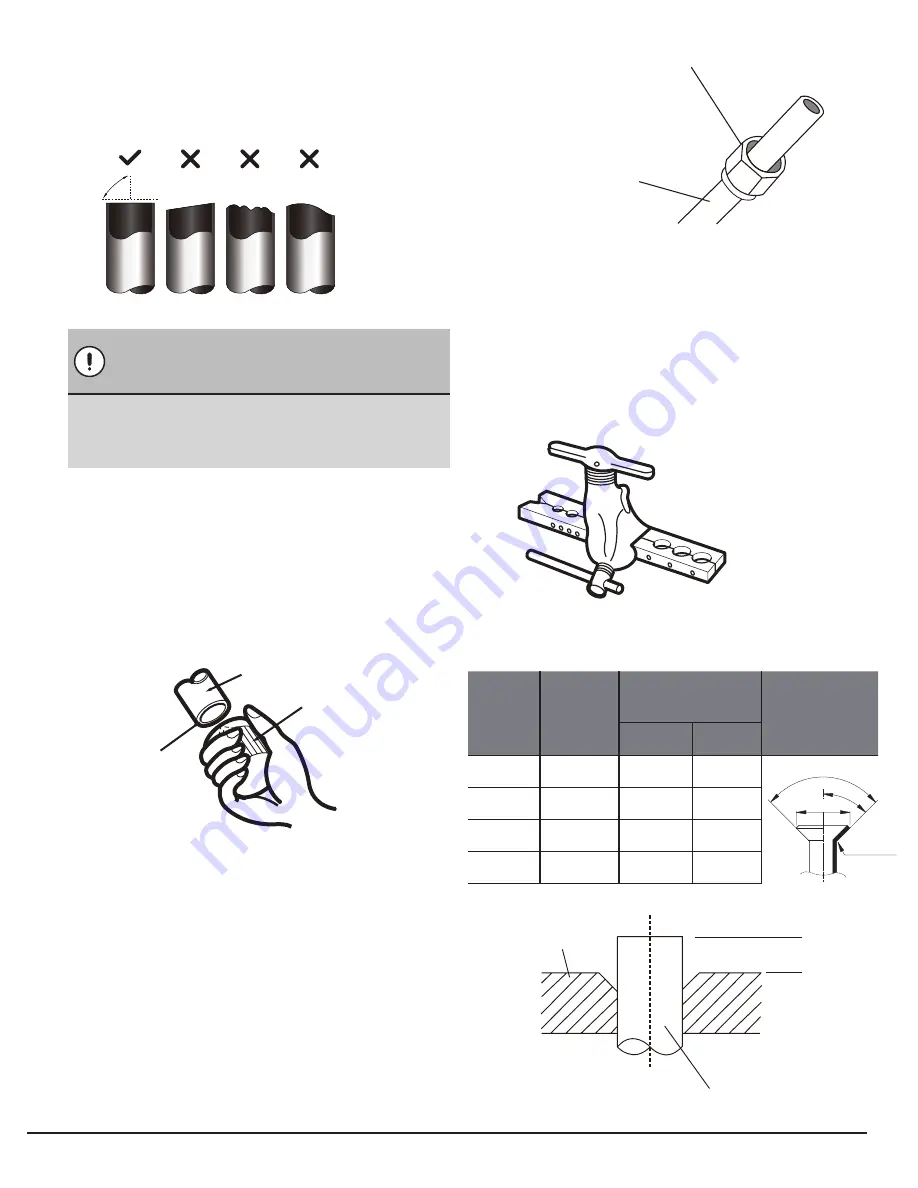
2. Using a pipe cutter, cut the pipe a little longer
than the measured distance.
3. Make sure that the pipe is cut at a perfect 90°
angle. Refer to
Fig. 6.1 for bad cut examples.
Oblique
Rough
Warped
90°
Page 15
Revised 5/14/2020
Fig 6.1
Fig 6.3
Fig 6.5
Fig 6.4
Fig 6.2
Be extra careful not to damage, dent, or deform
the pipe while cutting. This will drastically
reduce the heating efficiency of the unit.
DO NOT DEFORM PIPE
WHILE CUTTING
Step 2: Remove burrs
Burrs can affect the air-tight seal of refrigerant piping
connection. They must be completely removed.
1. Hold the pipe at a downward angle to prevent
burrs from falling into the pipe.
2. Using a reamer or deburring tool, remove all
burrs from the cut section of the pipe.
Step 3: Flare pipe ends
Proper flaring is essential to achieve an airtight seal.
1. After removing burrs from cut pipe, seal the
ends with PVC tape to prevent foreign materials
from entering the pipe.
2. Sheath the pipe with insulating material.
3. Place flare nuts on both ends of pipe. Make sure
they are facing in the right direction, because
you can’t put them on or change their direction
after flaring. See
Fig. 6.3.
Pipe
Reamer
Point down
Flare nut
Copper pipe
4. Remove PVC tape from ends of pipe when
ready to perform flaring work.
5. Clamp flare form on the end of the pipe. The end
of the pipe must extend beyond the edge of the
flare form in accordance with the dimensions
shown in the table below.
Table 7.1: Torque chart and flaring guide
Pipe
gauge
Flaring
torque
Flare dimension
(A) (Unit: Inch)
Flare shape
Min.
Max.
1/4"
14 ft/ lbs
0.33
0.34
3/8"
18 ft/ lbs
0.52
0.53
1/2"
26 ft/ lbs
0.64
0.65
5/8"
34 ft/ lbs
0.76
0.78
R0.4~0.8
45
°±
2
90
°
±
4
A
Flare form
Pipe
A