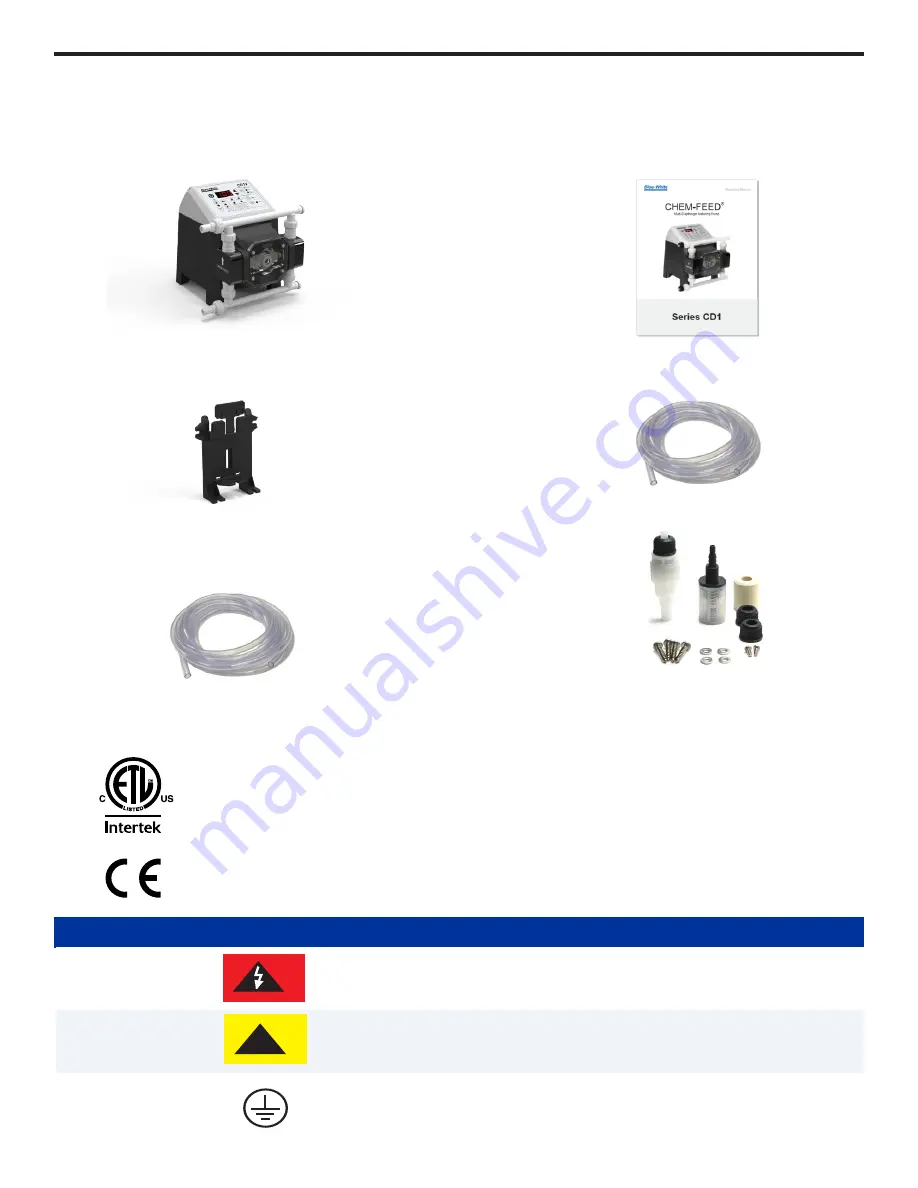
Page 6
4.0
What’s In The Box
>
Smooth chemical dosing, no pulsation dampener needed
>
Diaphragm Failure Detection (DFD) system which senses diaphragm failure
>
Rated for continuous duty.
>
Compatible with Blue-White Industries, Flow Verification Sensor (FVS) system.
>
Remote Start/Stop
>
Relay outputs include a single 250V/3A and a single solid state.
>
Multi diaphragm metering with industry best turndown at 2000:1
>
Built for long life at high pressures up to 150 PSI (10.3 bar)
>
Output rates up to 7.70 GPH (29.2 LPH).
>
Brushless DC motor.
4.1
Agency Listings
This pump complies to the Machinery Directive 2006/42/EC, BS, EN 60204-1, Low Voltage Directive
2014/35/EU BS EN 61010-1, EMC Directive 2014/30/EU, BS EN 50081-1/BS EN 50082-1.
This pump complies to the Machinery Directive 2006/42/EC, BS, EN 60204-1, Low Voltage Directive
2014/35/EU BS EN 61010-1, EMC Directive 2014/30/EU, BS EN 50081-1/BS EN 50082-1.
Symbol
Description
Warning (Risk of electric shock)
Caution (Refer to the user’s guide)
Ground, Protective Conductor Terminal
!
ENCLOSURE RATING
NEMA 4X
Constructed for either indoor or outdoor use to provide a degree of protection to personnel against incidental
contact with enclosed equipment; to provide a degree of protection against falling dirt, rain, sleet, snow,
windblown dust, splashing water, and hose-directed water; and that will be undamaged by external formation
of ice on enclosure.
IP66
No ingress of dust; complete protection against contact. Water projected in powerful jets against enclosure
from any direction shall have no harmful effects.
Page 7
CHEM-FEED CD1
CHEM-FEED CD1
5.1
Mounting Location
1. Choose an area located near the chemical supply tank, chemical injection point, and electrical supply. Also,
choose an area where the pump can be easily serviced.
2. Finding a secure surface and using the provided mounting hardware, mount the pump close to the injection
point. Keep the inlet (suction) and outlet (discharge) tubing as short as possible. Longer discharge tubing
increases back pressure at pump head.
NOTE
: Mounting the pump lower than the chemical container will gravity-feed chemical into it. This “flooded
suction” installation will reduce output error due to increased suction lift. A shut-off valve, pinch-clamp, or
other means to halt gravity-feed to the pump must be installed during servicing.
NOTE
: Install a back flow prevention check valve at the discharge side of the pump to prevent the system fluid
from flowing back through pump during tube replacement or during tube rupture.
NOTE
: It is recommended to have a pressure relief valve at the discharge side of the of pump to prevent
premature wear and damage to the pump tube, in the event that the discharge line becomes blocked.
NOTE
: The
does not require back pressure. Keep the discharge pressure as low as possible to maximize
pump
the tube life.
5.0
INSTALLATION
All diagrams are strictly for guideline purposes only. Always consult an expert before installing
metering pump on specialized systems. Metering pump should be serviced by qualified persons
only.
Always wear protective clothing, face shield, safety glasses and gloves when working on or near
your metering pump. Additional precautions should be taken depending on solution being
pumped. Refer to MSDS precautions from your solution supplier.
Risk of chemical overdose. Be certain pump does not overdose chemical during backwash and
periods of no flow in circulation system.
!
CAUTION
!
CAUTION
Be sure that installation does not constitute a cross connection with drinking water supply.
Check your local plumbing codes.
The pump should be serviced by qualified persons only. If equipment is used in a manner not
specified in this manual, the protection provided by the equipment may be impaired.
The pump should be supplied by an isolating transformer or RCD (operating current less or
equal 30 mA).
!
CAUTION
!
CAUTION
!
CAUTION
!
CAUTION
CD1 Multi-Diaphragm Pump
Instruction Manual
Wall Mounting Bracket
Suction Tubing (3/8”x5’)
Discharge Tubing (3/8”x5’)
Parts Kit
!Injection Fitting
!Foot Valve
!Screws
!Ceramic Weight
!Tube Nuts