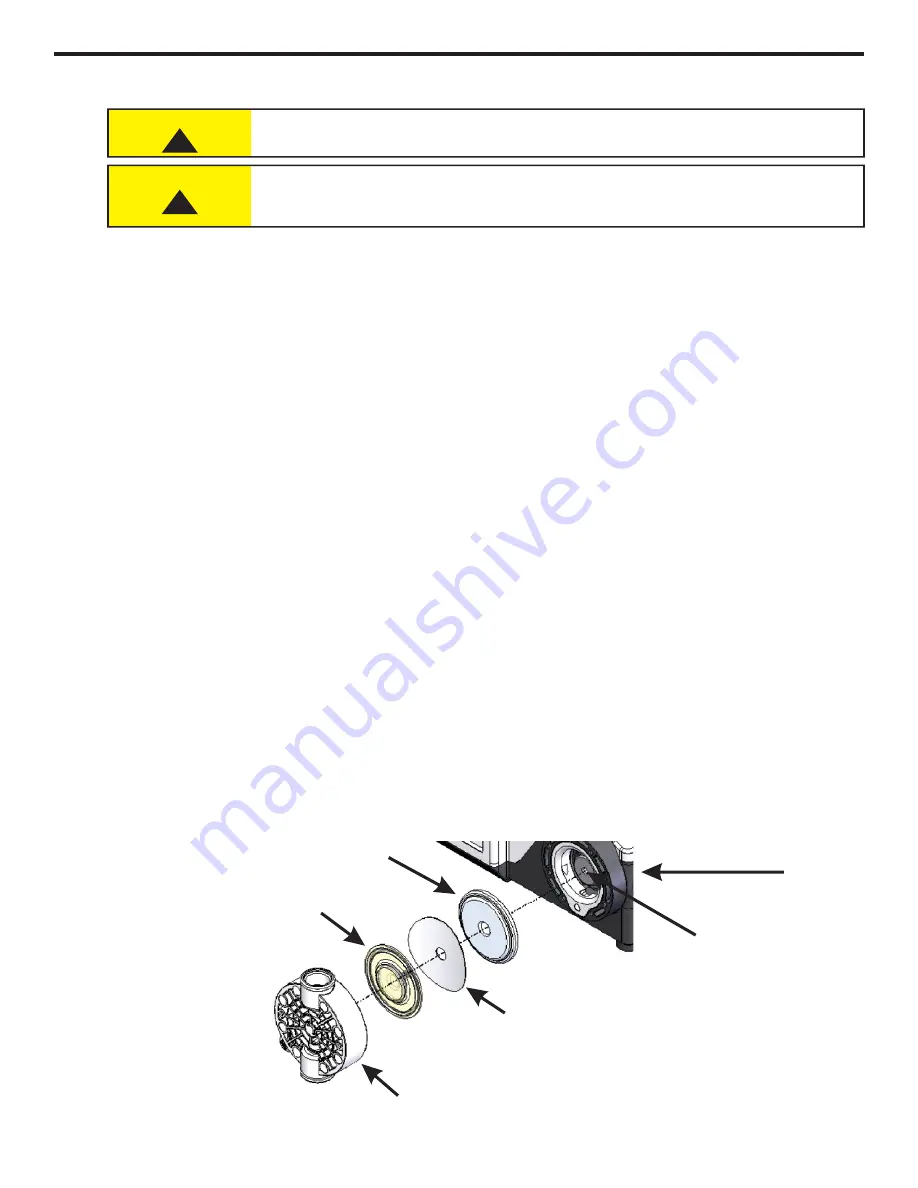
Page 14
8.0
OUTPUT ADJUSTMENT
The speed of the pumping mechanism is adjustable from 0.05 to 100 % motor speed (0.05 RPM to 100 RPM).
9.0
DFD (Diaphragm Failure Detection)
This system is capable of detecting presence of a large number of chemicals including Sodium Hypochlorite
(Chlorine), Hydrochloric (muriatic) Acid, Sodium Hydroxide, and many others. System will not be triggered by
water (rain, condensation, etc.) or lubricants.
If system has detected chemical, pump diaphragm must be replaced and pump head must be thoroughly cleaned.
Failure to clean pump head will void warranty.
If DFD alarm occurs, pump will stop, close an alarm output, and screen will flash DFD with an alarm icon.
DFD
DFD Sensors
Diaphragm
Diaphragm
Outlet
(discharge)
Inlet
(suction)
Pump
Head
Built -In DFD
Diaphragm Failure
Detection
CHEM-FEED CD1
Page 15
Prior to service, pump clean water through pump and suction / discharge line to remove
chemical.
Always wear protective clothing, face shield, safety glasses and gloves when working on or
near your metering pump. Additional precautions should be taken depending on solution
being pumped. Refer to MSDS precautions from your solution supplier.
!
CAUTION
!
CAUTION
10.0 Pump Maintenance
10.1 Routine Inspection and Maintenance
Pump requires very little maintenance. However, pump and all accessories should be checked weekly. This is
especially important when pumping chemicals. Inspect all components for signs of leaking, swelling, cracking,
discoloration or corrosion. Replace worn or damaged components immediately.
Cracking, crazing, discoloration during first week of operation are signs of severe chemical attack. If this occurs,
immediately remove chemical from pump. Determine which parts are being attacked and replace them with parts
that have been manufactured using more suitable materials. Manufacturer does not assume responsibility for
damage to pump that has been caused by chemical attack.
10.2 Cleaning Pump
Pump will require occasional cleaning, especially Injection fitting, Footvalve / Strainer, and pump head valves.
Frequency will depend on type and severity of service.
]
Inspect and replace pump head valves as required.
]
Periodically clean injection / check valve assembly, especially when injecting fluids that calcify such as sodium
hypochlorite. These lime deposits and other build ups can clog fitting, increase back pressure and interfere with
check valve operation.
]
Periodically clean suction strainer.
]
Periodically inspect pump housing (enclosure) for chemical attack. Protect pump housing from continuous
exposure to chemicals, such as drips or fumes from surrounding equipment and plumbing.
10.3 Replacing the Pump Diaphragm
]
When changing the diaphragm, the pump head chamber and pump head cover should be wiped free of any dirt
and debris. The pump stroke must be FORWARD when installing the diaphragm, and BACK when installing
and tightening the pump head.
]
When replacing the pump diaphragm, note the order of parts per the illustration below:
Piston
Backup washer
PTFE reinforcement ring
Diaphragm
Pump head
Pump
CHEM-FEED CD1