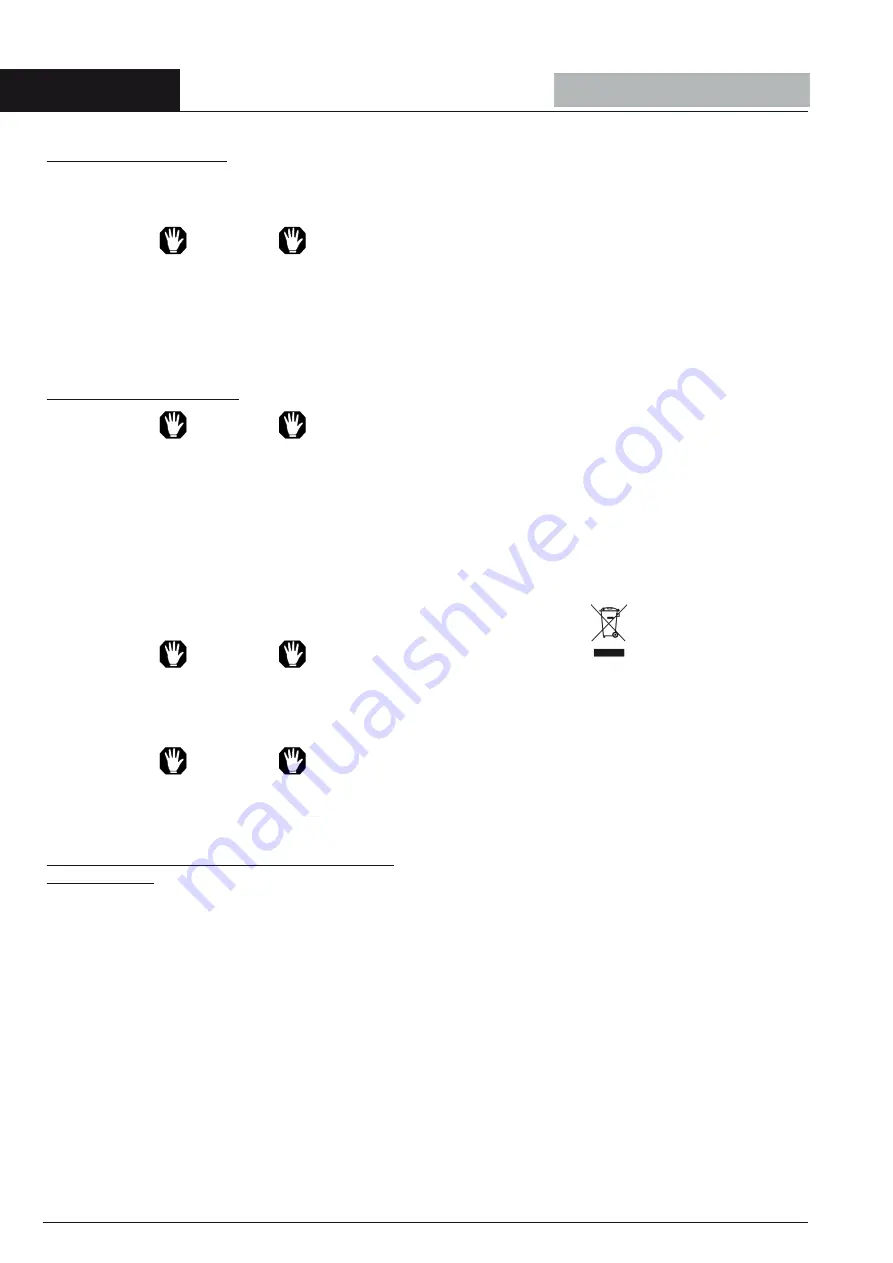
16
2.2. CLEANING (Fig.8)
2.2.a General information
Strict compliance with the maintenance instructions in this
section will keep your machine in a good working condition
and will notably reduce the need for repairs.
ATTENTION
If any machine component becomes faulty, FIRST CHECK
that all the instructions given in the previous paragraphs
have been complied with during use.
Repairs must be carried out immediately, as soon as the
fault occurs. This will prevent the trouble from becoming
worse and damaging other parts.
2.2.b Daily cleaning (Fig. 8)
ATTENTION
Daily operations to carry out when work has ended, with
the machine off, the main circuit-breaker disconnected,
the water cocks off and the wash tank empty.
1. Lift the overflow pipe (27) to completely drain the
water from the tank.
2. Remove the filters (26) on top of the tank.
3. Thoroughly clean the inside parts of the machine.
4. Remove the pump safety filter (30).
5. Wash the filters under running water and fit them cor-
rectly back in their housings.
ATTENTION
Never use corrosive or acid cleaning products, wire wool
or steel brushes since these could damage the machine.
2.3 PREVENTION MAINTENANCE (Fig. 8)
ATTENTION
The preventive maintenance operations must be carried out
with the machine off, the main circuit-breaker disconnected,
the water supply cocks off and the wash tank empty.
2.3.a Checking and cleaning the spray arms and
nozzles (Fig. 8)
Periodically check to make sure that the wash arms (25), the
rinse arms (23) and the relative nozzles are not clogged.
Cleaning the unit:
1. Unscrew the ring nut (28/29) and lift the spray arms
(23) and (25).
2. Wash the washing and rinsing arms.
Clean the nozzles (24) if they are clogged and then fit
the parts exactly back in their original positions.
3. Remount all parts by complying with the above instruc-
tions in reverse.
Part 2: For the operator
2.4 DESCALING
Where hard water is present lime scale deposits will
form in the machine and on dishes, which must, for rea-
sons of hygiene, be removed by descaling.
Advice on operation procedures and frequency for this
treatment are generally given by the detergent supplier,
who can provide suitable products.
In order to avoid damaging the machine, do not
exceed recommended doses, follow the detergent
producer’s directions scrupulously and, having fini-
shed operations, rinse thoroughly
2.5 TEMPORARY STOPPAGE
If the machine is to be left inactive for a period of some
weeks, it is advisable beforehand to load the tank and
run a few empty cycles with clean water then drain, so
as to avoid the formation of unpleasant odours.
If necessary, repeat the process several times until the
water is still clean after washing.
If the stoppage is to be very long, it is advisable to
drain the water from the boiler and from the electric
pump.
2.6 DEMOLITION and DISPOSAL.
When the machine is to be scrapped, drain the water
from the tank and from the boiler, as indicated in the
points above, and disconnect the machine from the
water and electricity supply networks, then dispose of
the components according to current regulations, res-
pecting national and local ecological and environmental
legislation, and taking care to separate the parts as
follows:
- metallic parts: body work, surfaces, panels, filters;
- electrical parts: motors, remote switches, micro-
switches, cabling;
- plastic parts: connectors, baskets;
- rubber parts: tubes, couplings
The producer declines all responsibility for any
printing errors contained in this booklet.
The instructions, drawings, tables and everything else
in this manual are of a confidential technical nature.
For this reason, none of the information may be either
completely or partially duplicated or disclosed to
third parties without prior written authorization from
BLUE SEAL which is the sole proprietor and which
reserves the right to make any modifications as may
be considered necessary without advance warning.
ENGLISH