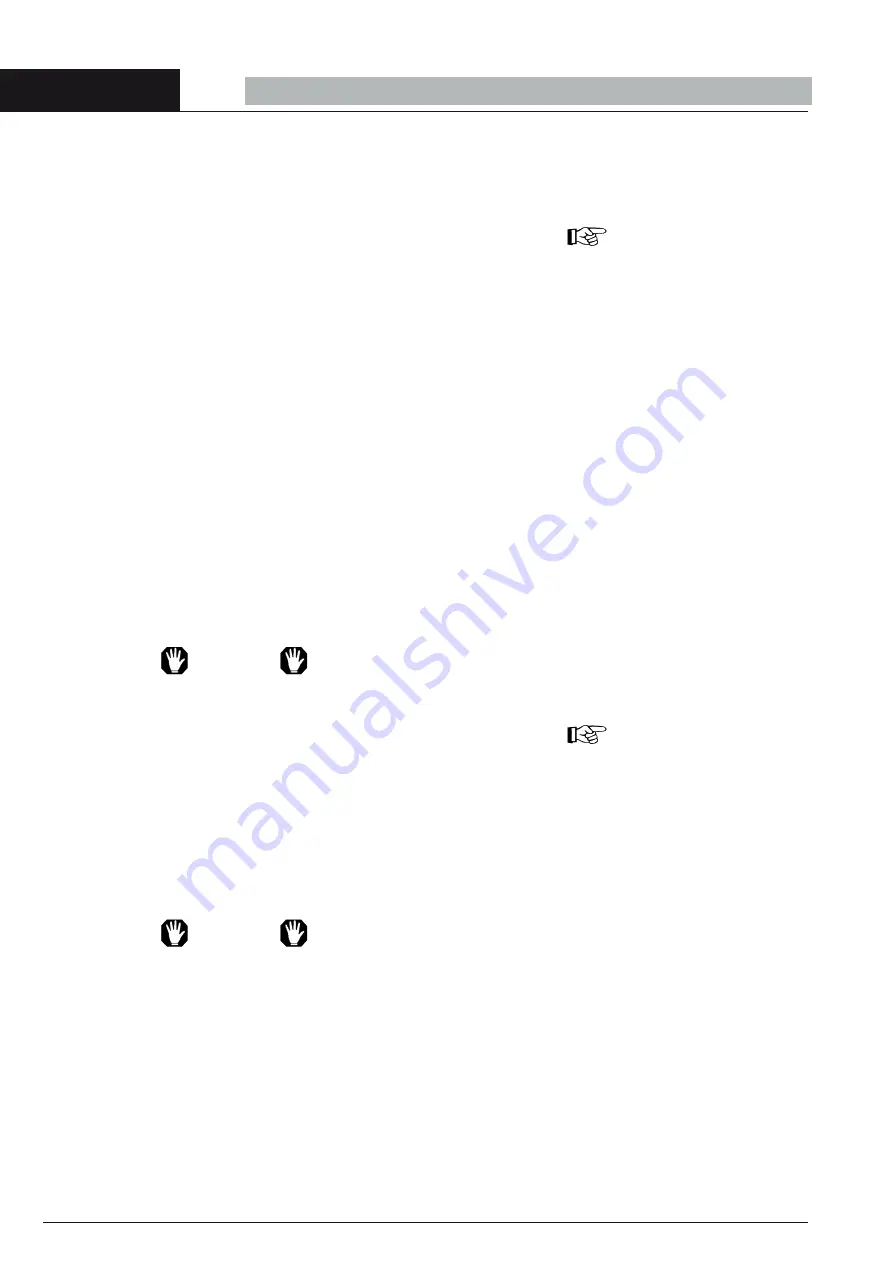
10
ENGLISH
Part 1: GENERAL DESCRIPTION and SAFETY DEVICES
1.1 GENERAL DESCRIPTION
The dishwashers of the SH 120 E BT line give an excellent
idea of the know-how achieved by Hoonved in the field of
machines for catering sector.
They are true professional washing systems that can be
integrated by the use of shelves, tables, etc.
The washing degree is unrivalled for plates, cutlery, glas-
ses, cups, trays and crockery. Model SH 120 E BT can
wash up to as many as 1200 plates in an hour.
The models feature different productive capacities.
The electronic controls, with touch-panel commands
and a display giving machine temperature and status
readings, make use easy. Compatible with the HACCP
hygiene control system, this machine is in line with the
most rigorous hygiene standards.
1.2 TYPE OF USE AND IMPROPER USE
These machines have been designed and built to wash
crockery placed in special baskets and using detergent
and rinsing agent.
• Permitted crockery: glasses, teacups, trays, coffee
cups, saucers, cutlery made of materials suitable for
dishwashers and of a size able to fit into the basket
and machine.
• Use of specific detergents and rinsing agents for in-
dustrial purposes normally available in the shops is
permitted.
ATTENTION
Any improper use of the machine relieves the manufacturer
from all and every responsibility for accidents or damage
to persons and property, also voiding all conditions of
guarantee.
1.3 TRANSPORT, SHIPMENT AND
STORAGE (Fig. 2)
- The machine is normally shipped in a cardboard box
closed by straps.
- When transporting the packed machine, use a lift truck
or transpallet, positioning the box on the relative forks.
ATTENTION
The machine must be sheltered from the weather when
shipped and stored.
1.4 INSPECTIONS ON ARRIVAL
When the machine arrives, check that the packaging is in
a perfect condition and that there is no visible damage.
If everything is in order, remove the packaging (unless
other instructions have been received from the manufac-
turer) and check that the machine is free from damage
caused by transport.
Now check whether there has been any damage to the
structure, crushing or breakages.
If damage or imperfections are discovered:
1 -
Immediately notify the haulage contractor both
by phone and in writing by registered letter with return
receipt attached;
2 - Inform the manufacturer by registered letter (with return
receipt attached).
IMPORTANT
Norification of damage or faults must be immediate, in any
case within 3 days from the date on which the machine
is received.
1.5 UNPACKING (Figs 2-3)
Proceed in the following way in order to remove the
packing:
1. Cut the straps (10) that hold the cardboard in place.
2. Remove the box (11) by lifting it upwards.
3. Remove the protective film from the machine.
4. Remove the machine from the base by lifting it from the
lower part of the casing.
5. All packing must be collected and not left within children’s
reach since it could become a source of danger. The
packing can be disposed of in the same way as solid
urban waste.
Lift the machine by raising the lower part of the casing using
a lift truck or transpallet.
1.6 MACHINE IDENTIFICATION (Fig. 4)
- The serial number and machine data are stamped on
the data plate (12) affixed to the rear part of the machine
itself.
IMPORTANT
Always state the model and serial number of the machine
when requesting technical assistance or ordering spare parts.
1.7 DESCRIPTION OF THE SAFETY
DEVICES
• Models SH 120 E BT are equipped with a safety mi-
croswitch that blocks the washing pump if the tub access
door is accidentally opened, and of other electronic safety
devices.
• The electrical parts are enclosed by panels locked by
screws.
• The machine is fitted with an equipotential ground con-
ductor.
• Safety overflow to prevent water from spilling.
1.8 REFERENCE STANDARD
• The machine and its safety devices has been built in
compliance with the following standards:
• Essential safety requisites established by Directive
2006/95/CE (LVD) and 2004/108/CE (EMC)
.
• Essential requisites established by Directive 2002/95/
CEE (RoHS).