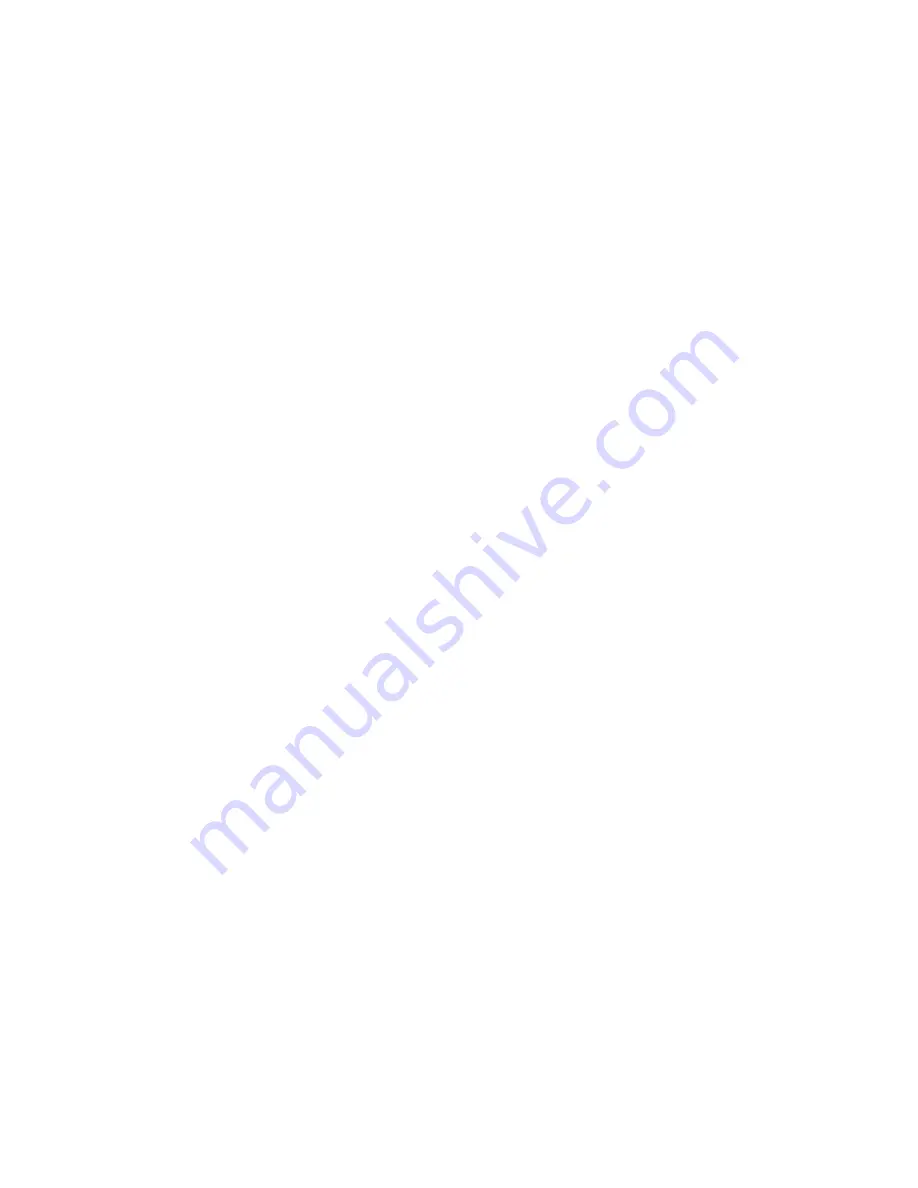
9-2
B
G-D40-0131
CAUTION:
Hydraulic oil can damage parts. Wipe off
any oil immediately. Provide a container
under the line or fitting before discon-
necting.
4.
and remove leaking line or fit-
ting and replace it with a new line or fitting. Check
level of hydraulic oil. With lift carriage fully low-
ered, fill reservoir with hydraulic oil to 1 inch below
opening. Use hydraulic oil listed in
5.
Turn on key switch (21,
) and emer-
gency disconnect (2,
6.
Operate the lift and lower buttons to refill the
cylinder and lines with hydraulic oil.
7.
Check level of hydraulic oil. Hydraulic oil must be
1 inch below opening. If required, add hydraulic
oil to bring to proper level. Use hydraulic oil listed
in
8.
Install the compartment covers as described in
paragraph
9-2. HYDRAULIC AND ELECTRICAL ASSEMBLY
REMOVAL
The hydraulic system and electrical system can be
removed as an assembly to provide additional clear-
ance for various maintenance procedures.
WARNING:
When forks are raised, pressure exists in
the hydraulic system lines and fittings. To
ensure release of pressure, forks must
be fully lowered and the batteries discon-
nected before performing any mainte-
nance on the hydraulic system.
9-2.1. Removal
1.
Lower forks fully.
2.
) and emer-
gency disconnect (2,
3.
Remove the compartment covers as described in
paragraph
4.
Disconnect hose (3,
) from pump and
motor assembly (4).
5.
Tag and disconnect all harnesses and cables from
electrical components on board (4,
).
6.
Support board (4) and remove four screws (1,
), four lock washers (2) and four flat
washers (3).
7.
Remove board (4).
9-2.2. Installation
1.
Position board (4,
) on frame and
secure with four screws (1,
), four
lock washers (2) and four flat washers (3).
2.
Reconnect hose (3,
) to pump and
motor assembly (4).
3.
Reconnect all harnesses and cables to electrical
components on board (4,
4.
Turn on key switch (21,
) and emer-
gency disconnect (2,
5.
Install the compartment covers as described in
paragraph
9-3. HYDRAULIC PUMP, MOTOR, AND RESER-
VOIR ASSY
The hydraulic pump/motor assembly can be disas-
sembled and repaired. However, a defective pump,
valve or motor requires replacement of that compo-
nent.
WARNING:
When forks are raised, pressure exists in
the hydraulic system lines and fittings. To
ensure release of pressure, forks must
be fully lowered and the batteries discon-
nected before performing any mainte-
nance on the hydraulic system.
9-3.1. Removal
1.
Lower forks fully.
2.
) and emer-
gency disconnect (2,
3.
Remove the hydraulic and electrical assembly as
described in paragraph
NOTE:
The reservoir will be filled with hydraulic oil.
Place a container under the pump assembly
to catch any hydraulic oil.
4.
Remove two screws (5,
), lock washers
(6) and flat washers (7) and remove pump and
motor (4).
9-3.2. Disassembly and Reassembly
1.
Remove the hydraulic pump/motor assembly as
described in paragraph
2.
Refer to
for disassembly and reassem-
bly.
Summary of Contents for EPJ-40
Page 6: ...1 2 PDM0495...
Page 11: ...B Figure 2 1 Sample of Operator Check List R6479...
Page 14: ...2 6 B NOTES...
Page 36: ...4 16 BG D40 0131 NOTES...
Page 44: ...5 8 BG D40 0131...
Page 47: ...BG D40 0131 7 1 SECTION 7 TRANSMISSION DRIVE WHEEL LOAD WHEEL...
Page 50: ...7 4 BG D40 0131 Figure 7 2 Transmission Motor Brake Mounting D40 5...
Page 55: ...BG D40 0131 9 3 Figure 9 2 Pump Motor Assy D40 15...
Page 57: ...BG D40 0131...
Page 58: ...9 6 BG D40 0131 NOTES...
Page 61: ...BG D40 0131 10 3 Figure 10 1 Electrical Components Sheet 1 D40 18...
Page 63: ...BG D40 0131 10 5 Figure 10 2 Electrical Components Sheet 2 D40 19...
Page 66: ...10 8 BG D40 0131 NOTES...
Page 67: ...BG D40 0131 11 1 SECTION 11 OPTIONAL EQUIPMENT...
Page 68: ...11 2 BG D40 0131 NOTES...
Page 70: ...12 2 BG D40 0131 Figure 12 1 Steering Arm D40 1...
Page 72: ...12 4 BG D40 0131 Figure 12 2 Control Head D40 2...
Page 74: ...12 6 BG D40 0131 Figure 12 2 Control Head Continued D40 2...
Page 76: ...12 8 BG D40 0131 Figure 12 3 Cap Assembly D40 3...
Page 78: ...12 10 BG D40 0131 Figure 12 4 Emergency Reverse Switch Assembly D40 4...
Page 80: ...12 12 BG D40 0131 Figure 12 5 Transmission Motor Brake Mounting D40 5...
Page 82: ...12 14 BG D40 0131 Figure 12 6 Transmission Transmission Used up to Serial E2219364 D40 6...
Page 84: ...12 16 BG D40 0131 Figure 12 6 Transmission Used up to Serial E2219364 D40 6...
Page 86: ...12 18 BG D40 0131 Figure 12 7 Transmission Used from Serial E2219365 D40 6...
Page 88: ...12 20 BG D40 0131 Figure 12 7 Transmission Used from Serial E2219365 D40 6...
Page 90: ...12 22 BG D40 0131 Figure 12 8 Compartment Covers D40 7...
Page 92: ...12 24 BG D40 0131 Figure 12 9 Load Backrest D40 22...
Page 94: ...12 26 BG D40 0131 Figure 12 10 Frame D40 11...
Page 96: ...12 28 BG D40 0131 Figure 12 11 Lift Link Assembly D40 12...
Page 98: ...12 30 BG D40 0131 Figure 12 12 Load Wheel D40 13...
Page 100: ...12 32 BG D40 0131 Figure 12 13 Caster D40 23...
Page 102: ...12 34 BG D40 0131 Figure 12 14 Hydraulic System D40 14...
Page 104: ...12 36 BG D40 0131 Figure 12 15 Pump Motor Assy D40 15...
Page 106: ...12 38 BG D40 0131 Figure 12 16 Lift Cylinder D40 16...
Page 108: ...12 40 BG D40 0131 Figure 12 17 Electrical System D40 17...
Page 110: ...12 42 BG D40 0131 Figure 12 18 Motor Assembly D40 8...
Page 112: ...12 44 BG D40 0131 Figure 12 19 Electrical Components Sheet 1 D40 18...
Page 114: ...12 46 BG D40 0131 Figure 12 20 Electrical Components Sheet 2 D40 19...
Page 116: ...12 48 BG D40 0131 Figure 12 20 Electrical Components Sheet 2 Continued D40 19...
Page 118: ...12 50 BG D40 0131 Figure 12 21 Wiring Harness D40 20...
Page 120: ...12 52 BG D40 0131 Figure 12 22 Wiring Cables D40 21...
Page 122: ...12 54 BG D40 0131 NOTES...
Page 123: ......