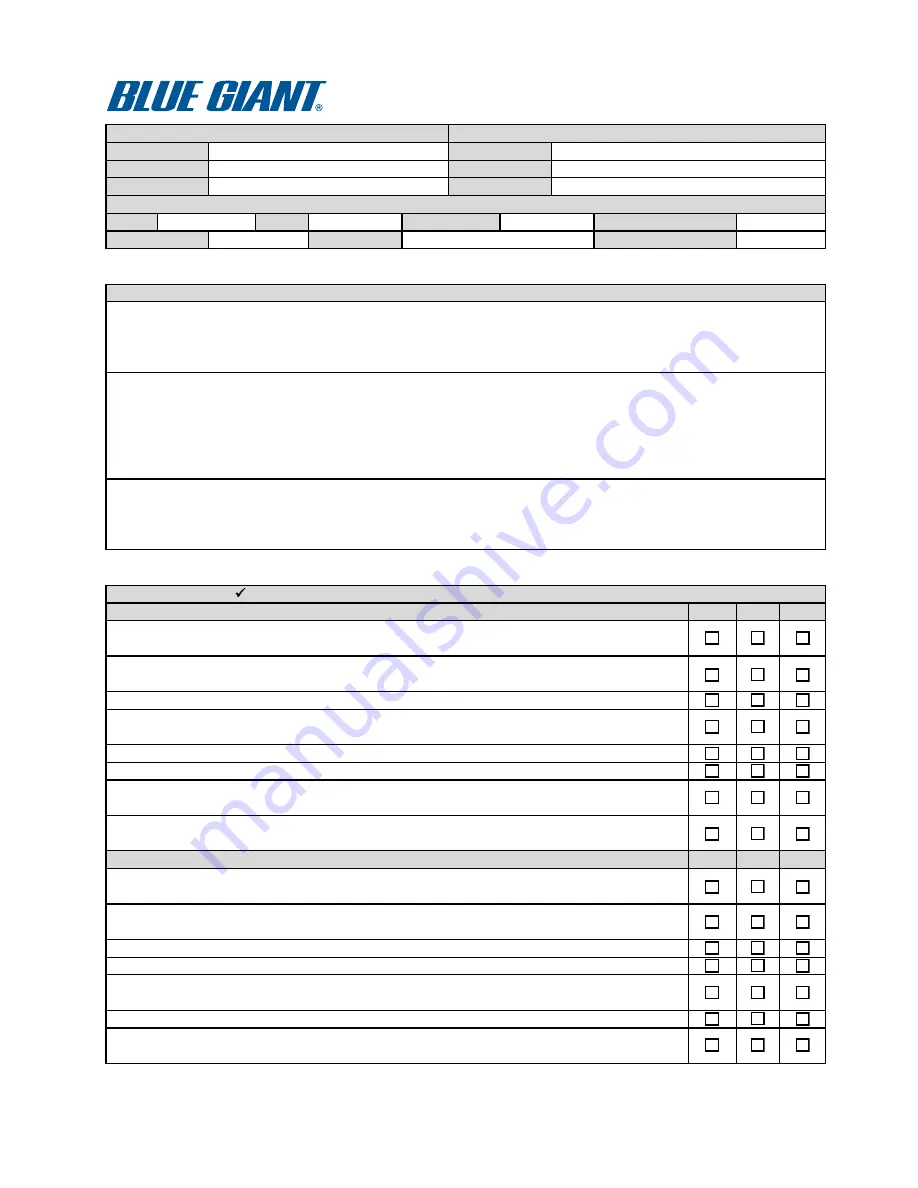
VERSION G
PAGE 1 OF 2
MODEL:
SERIAL:
P
F
C
P
F
C
Instrument panel is clean and free of debris and dash display is func
�
onal.
Operator le
�
side control arm steering wheel func
�ons
properly.
Emergency lower bu
�
on operates properly.
Ensure gate switches disable travel/li
�
and lower func
�
ons and
flashin
g lights on the front and rear of
the vehicle.
HOUR METER:
BATTERY SPEC.:
OPTIONS:
PREVIOUS INSPECTION:
Pla
�o
rm guard rails are undamaged and gates open / close freely.
Chains are adequately lubricated and are not dry or rusty.
Mast cover plates are in place and securely
a�ac
hed for each sec
�
on.
Con
�nu
ed on page 2
FREQUENT INSPECTIONS:
The owner and user are required by ANSI A92.6 to ensure frequent inspec
�ons
of the
BG Zero
Task
Support Vehicle occur and are performed in accordance with the following points: 1. If purchased used unless it's determined
that the frequent and annual inspec
�ons
are current. 2. The
BG Zero
Task Support Vehicle has been in service for three (3)
months or 150 hours, whichever comes
fi
rst. 3. The
BG Zero
Task Support Vehicle has been out of service for a period longer
than three (3) months. inspec
�on
is to be performed by a mechanic that is
qualifi
ed and authorized to perform service on the
BG Zero
Task Support Vehicle. All service records must be maintained.
INSPECTION REQUIREMENTS per ANSI A92.6 (ANNUAL AND FREQUENT)
ANNUAL INSPECTION:
The owner and user are required by ANSI A92.6 to ensure annual inspec
�ons
of the
BG Zero
Task Support
Vehicle occur and are performed no later than 13 months from the date of prior annual inspec
�on
or every 700 hundred hours
of use, whichever occurs
fi
rst. This annual inspec
�on
is to be performed by a mechanic that is
qualifi
ed and authorized to
perform service on the
BG Zero
Task Support Vehicle. All service records must be maintained.
N
O
I
T
A
M
R
O
F
N
I
R
E
S
U
D
N
E
/
R
E
N
W
O
N
O
I
T
A
M
R
O
F
N
I
R
E
L
A
E
D
COMPANY:
ADDRESS:
Annual Inspec
�
on Report
INSTRUCTIONS:
Refer to service/maintenance manuals for spec
ifi
c informa
�on
regarding inspec
�on
procedures and criteria.
Indicate in the appropriate space as each item has been performed. If the item is found to be not acceptable, describe each
discrepancy on an addi
�onal
page and a
�
ach to the form. Immediate ac
�
on must be taken to correct all discrepancies. The
vehicle shall not be placed in service un
�l
all discrepancies have been corrected.
CITY/STATE/ZIP:
COMPANY:
ADDRESS:
CITY/STATE/ZIP:
MAST SIZE:
VEHICLE INFORMATION:
Operator right side control arm func
�
ons properly. Horn / travel / li
�
/ lower / accelerator bu
�
ons are
func
�onal
.
Put a in the column that applies: P = Passed Insp
ec�o
n , F = Failed Insp
ec�o
n, C = Corrected
Drive and operate machine to test all func
�
ons. Ensure controls operate properly and return to "
off
" or
neutral when released.
Ensure emergency power disconnect switch deac
�va
tes all movement and power and that the deadman
foot switch operate properly.
FUNCTIONS and CONTROLS
Mast sec
�ons
are free of visual evidence of damage. Mast chains and cables are inspected per the
Service and Maintenance Manual.
OPERATOR PLATFORM ASSEMBLIES
The drive wheel returns to "neutral" (straight forward) when powering up the vehicle and is accurately
depicted on the LCD display.
All nuts, bolts, pins, sha
�
s, covers, bearings and wear pads are checked for proper installa
�on
, and do
not have excessive wear, cracks or distor
�
on.
Mast wiring harnesses are properly installed, seated in their pulleys and that there are no frayed or
broken strands.
Mast operates smoothly to full height and descends smoothly. Ensure speed cutbacks occur at
appropriate heights per the maintenance manual.
Page 2-6
14
Summary of Contents for BG ZERO
Page 4: ...4...
Page 20: ...Table 3 3 Troubleshooting Chart Traction Lift Controller 20...
Page 21: ...Figure 3 2 Troubleshooting Chart Traction Lift Controller Continued 21...
Page 22: ...Table 3 3Troubleshooting Chart Traction Lift Controller Continued 22...
Page 23: ...Figure 3 2 Troubleshooting Chart Traction Lift Controller Continued 23...
Page 24: ...Figure 3 2 Troubleshooting Chart Traction Lift Controller Continued 24...
Page 28: ...NOTES 28...
Page 30: ...Figure 5 1 Drive System EC_0003 30...
Page 33: ...Figure 6 2 Frame EC_0001 33...
Page 34: ...Figure 6 3 Transmission Motor Brake Assembly EC_0004 34...
Page 37: ...Figure 7 2 Elevation System Overview EC_0013 37...
Page 38: ...Figure 7 3 Elevation System Breakdown EC_0014 38...
Page 39: ...Figure 7 4 Platform EC_0017 39...
Page 40: ...40...
Page 42: ...Figure 8 1 Hydraulic System EC_0007 42...
Page 45: ...Figure 8 4 Elevation System Overview EC_0013 45...
Page 46: ...Figure 8 5 Elevation System Breakdown EC_0014 46...
Page 48: ...Figure 9 1 Electrical System EC_0009 48...
Page 52: ...Figure 9 3 Elevation System Breakdown EC_0014 52...
Page 53: ...Figure 9 4 Platform EC_0017 53...
Page 54: ...Figure 9 5 Operating Control Assembly Left EC_0005 54...
Page 55: ...Figure 9 6 Operating Control Assembly Right EC_0006 55...
Page 56: ...NOTES 56...
Page 58: ...NOTES 58...
Page 60: ...Figure 11 1 Frame EC_0001 60...
Page 62: ...Figure 11 2 Caster Assembly EC_0002 62...
Page 64: ...Figure 11 3 Drive System EC_0003 64...
Page 66: ...Figure 11 4 Transmission Motor Brake Assembly EC_0004 66...
Page 68: ...Figure 11 5 Operating Control Assembly Left EC_0005 68...
Page 70: ...Figure 11 6 Operating Control Assembly Right EC_0006 70...
Page 72: ...Figure 11 7 Hydraulic System EC_0007 72...
Page 74: ...Figure 11 8 Hydraulic Pump Assembly EC_0008 74...
Page 76: ...Figure 11 9 Electrical System EC_0009 76...
Page 78: ...Figure 11 10 Wiring Harness 1 EC_0010 78...
Page 80: ...Figure 11 11 Wiring Harness 2 EC_0011 80...
Page 82: ...Figure 11 12 Wiring Cables EC_0012 82...
Page 84: ...Figure 11 13 Elevation System Overview EC_0013 84...
Page 86: ...Figure 11 14 Elevation System Breakdown EC_0014 86...
Page 88: ...Figure 11 14Elevation System Breakdown Continued EC_0014 88...
Page 90: ...Figure 11 15 Lift Cylinder EC_0015 90...
Page 92: ...Figure 11 16 Lift Cylinder Assembly Tray EC_0019 92...
Page 94: ...Chain Assembly Figure 11 17 Chain Assembly EC_0016 94...
Page 96: ...Figure 11 18 Operator Platform EC_0017 96...
Page 98: ...Figure 11 18Operator Platform Continued EC_0017 98...