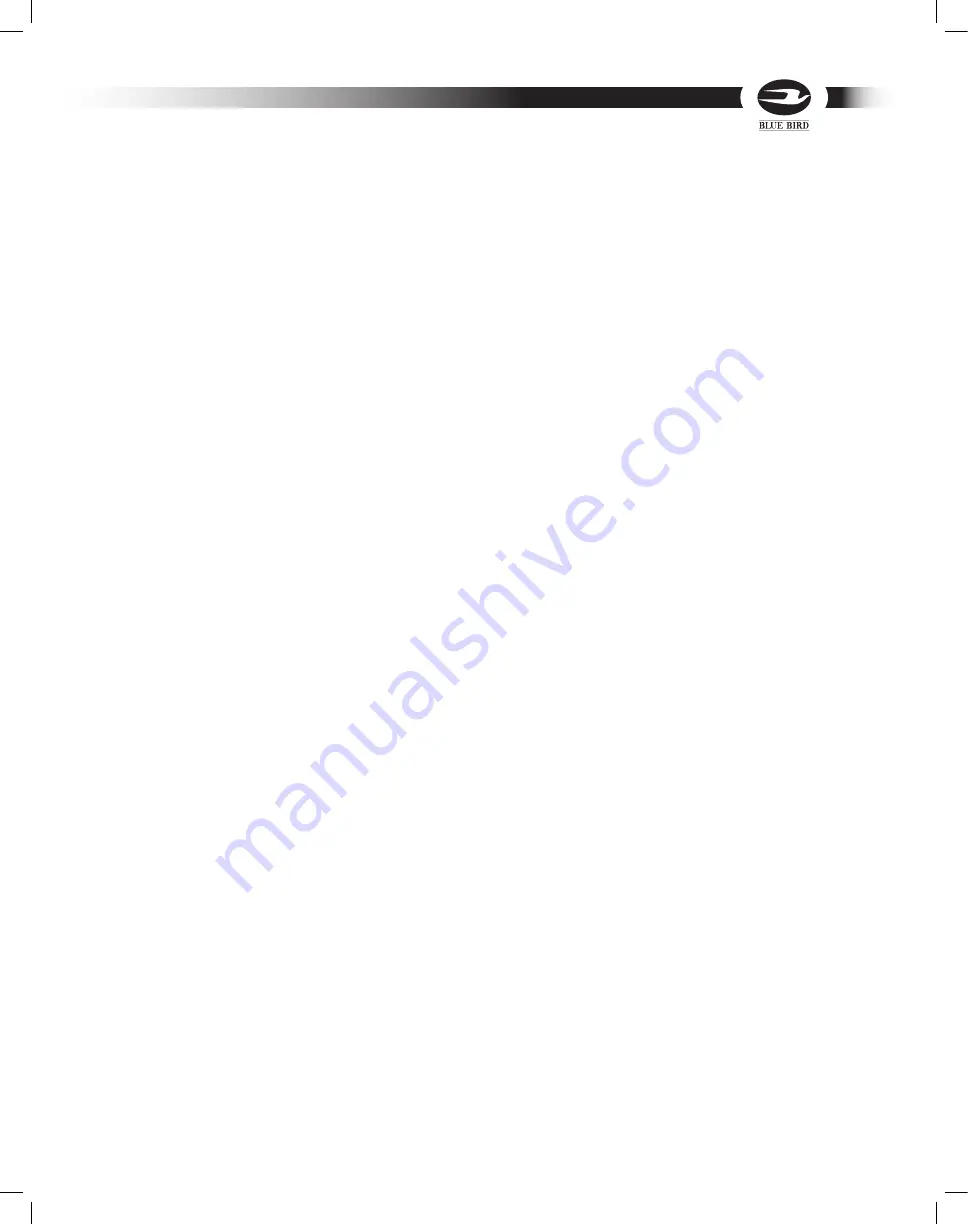
95
r o u t i n e
o p e r a t i o n
Allison Automatic Transmission driving Tips
Accelerator control.
The pressure of your foot on the accelerator pedal influences
the automatic shifting. An electronic signal tells the ECU how far the driver has de-
pressed the pedal, and the transmission adjusts its shifting for maximum perfor-
mance.
downshift or reverse inhibitor Feature with Allison 3000 PTs Transmission.
Al-
though there is no limitation on upshifting, there is a limit on downshifting and shifts
from neutral into drive or reverse. If a downshift or neutral-to-range shift is selected
when the engine speed or throttle position is too high, the ECU/TCM will not allow
the shift until reaching a lower speed. If idle speed is too high, shifts to range are pro-
hibited. A continuous “beep” tone sounds when reverse is selected during forward
movement or if a neutral-to-range shift is selected at too high an engine speed.
cold Weather starts.
Most Allison transmissions are programmed to restrict opera-
tion until operating temperature is reached. When the transmission fluid tempera-
ture is below -25° F (-32° C), the transmission will not shift into an operating range,
and the “Check Transmission” light illuminates. When the transmission fluid tem-
perature is between -24° F and 20° F (-31° C to -7° C), the transmission will operate
in 1st, 2nd, or Reverse only. If there is no other problem with the transmission, the
“Check Transmission” light will not be illuminated. For transmission fluid tempera-
tures above 20° F (-7° C), the transmission shifts and operates normally. Read the cold
weather operation instructions in the Allison Transmission™ Operator’s Manual sup-
plied with the bus.
using the engine to slow the Vehicle.
To use the engine as a braking force, shift
the range selector to the next lower range. If the vehicle is exceeding the maximum
speed for a lower gear, use the service brakes to slow the vehicle to an acceptable
speed where the transmission may be downshifted safely. After reaching the lower
speed, the ECU will automatically downshift the transmission. Engine braking pro-
vides good speed control for going down grades. When the vehicle is heavily loaded,
or the grade is steep, it may be desirable to select a lower range before reaching the
grade. If engine-governed speed is exceeded, the transmission will upshift automati-
cally to the next range.
[CAUTION]
The transmission incorporates a hold feature to prohibit upshift-
ing above the range selected during normal driving. For downhill operation,
select a lower transmission range. However, if engine governed speed is ex-
ceeded, the transmission may upshift to the next higher range. Use the vehicle
brakes to prevent exceeding engine governed speed in the held range.
Summary of Contents for VISION 2011
Page 1: ...10013333 2011 BBCV D R I V E R S H A N D B O O K 10013333 BBCV BLUE BIRD VISION 2011 ...
Page 2: ......
Page 3: ...10013333 Revision B ...
Page 8: ...VISION D R I V E R S H A N D B O O K 6 ...
Page 26: ...VISION D R I V E R S H A N D B O O K 24 ...
Page 70: ...VISION D R I V E R S H A N D B O O K 68 ...
Page 137: ...135 Notes n o t e s ...
Page 138: ...VISION D R I V E R S H A N D B O O K 136 Notes ...
Page 139: ......
Page 140: ...10013333 2011 BBCV D R I V E R S H A N D B O O K 10013333 BBCV BLUE BIRD VISION 2011 ...