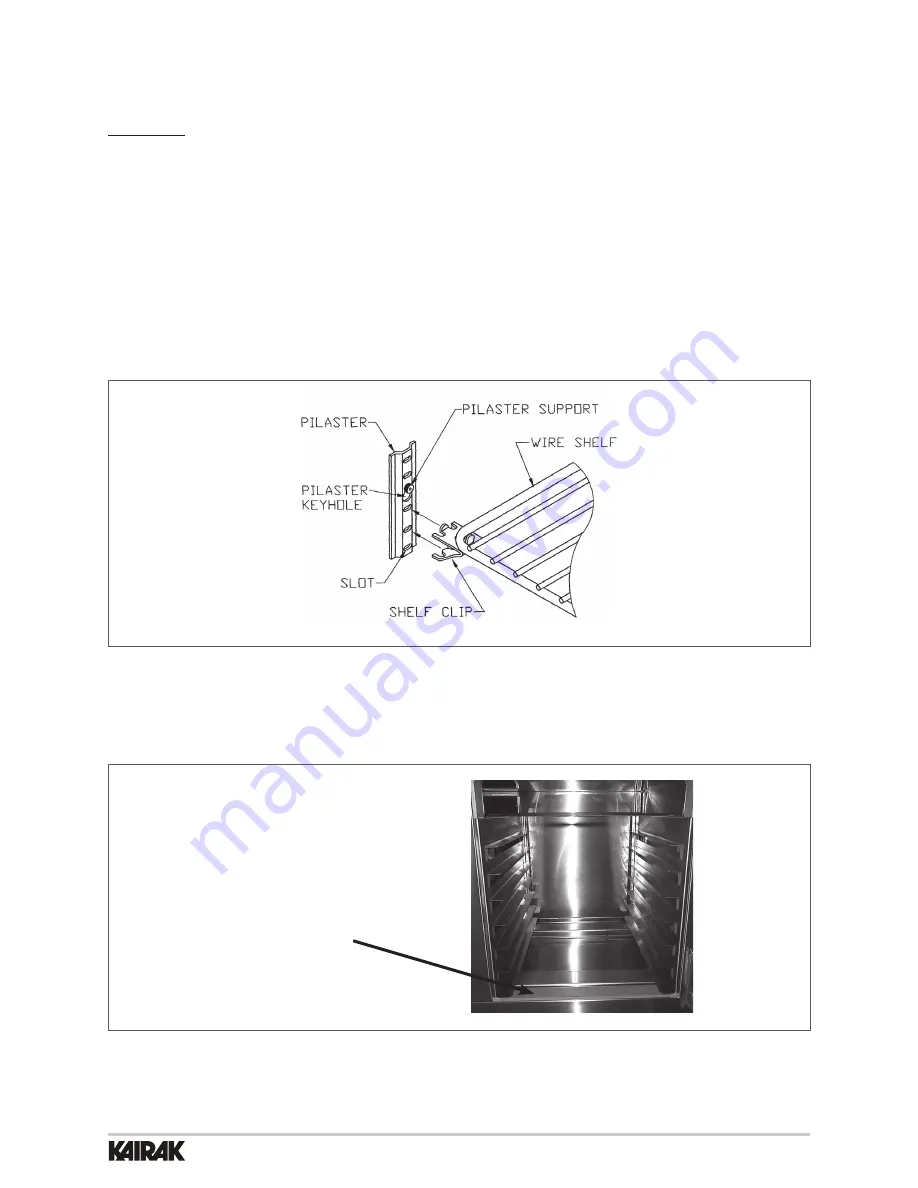
PAGE 12
PREP TABLE
8. MAINTENANCE PROCEDURES
WARNING:
DISCONNECT ELECTRICAL POWER SUPPLY BEFORE CLEANING ANY PARTS ON THE UNIT.
8A - CLEANING LOWER STORAGE CABINET
Use warm, soapy water to clean lower storage cabinet and doors. NEVER use cleaners containing grit,
abrasive materials, bleach or harsh chemicals. Rinse thoroughly and dry with a clean soft cloth. Always
rub in the same direction as the grain pattern on the stainless steel.
To clean the inside of the lower storage cabinet, remove wire shelves. All wire shelves are adjustable and
can be easily removed. Clean shelving in a sink. If shelf clips have been removed, make sure the four clips
per shelf are at same height in pilaster. The shelf clips have a small projection on top which holds the shelf
in position and prevents it from slipping forwards. The clip must be “snapped” in place by squeezing clip
together and inserting into slot in pilaster keyhole. (See Fig. 5)
FIG. 5
If equipped with tray slides, the tray slides can be removed by lifting up on the front of the tray slide
assembly to allow the front tray slide frame to clear the bottom of the door opening, then pull the frame
assembly out. (See Fig. 6)
FIG. 6
TRAY SLIDE FRAME
Summary of Contents for K99597F15
Page 1: ...INSTRUCTION MANUAL KBP PREP TABLE ...
Page 20: ...NOTES ...