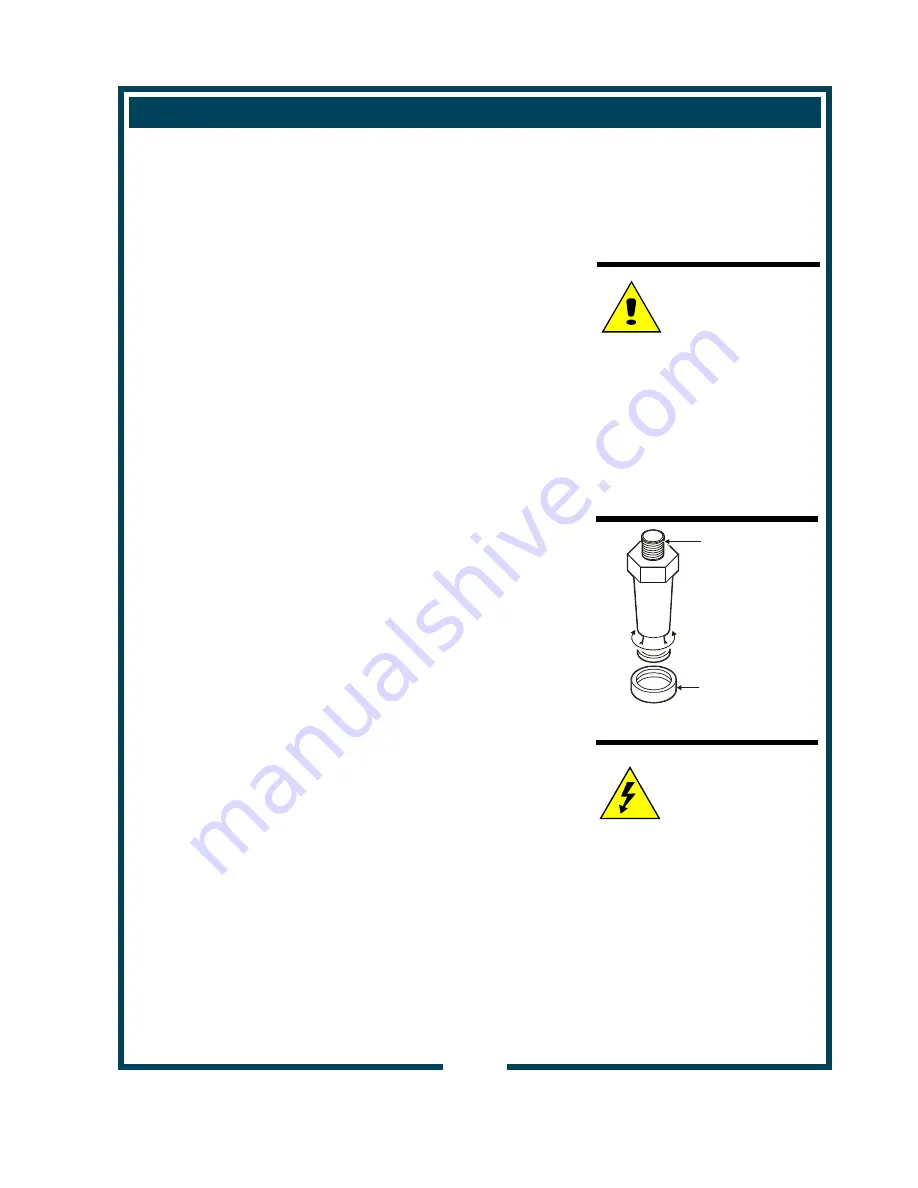
5
INSTALLATION INSTRUCTIONS
INSTALL LEGS
The brewer is provided with 4" adjustable legs and rubber feet. Be
sure the legs are securely screwed into the base of the brewer, and
that the rubber feet are properly installed.
LEVEL THE UNIT
The adjustable legs allow the brewer to be leveled. Set the brewer
in its ultimate operating location and check for level with a spirit
level Adjust the brewer for level from front-to-rear, and from side-
to-side. Be sure all four feet rest firmly on the counter.
PLUMBER’S INSTALLATION INSTRUCTIONS
IMPORTANT:
This equipment must be installed in accordance with the Basic
Plumbing Code of the Building Officials and Code Administrators
International (BOCA), and the Food Service Sanitation Manual of
the Food and Drug Administration (FDA). Also, this equipment
installation must comply with all local plumbing codes and
ordinances.
IMPORTANT:
Brewer must be installed on a water line with a full-flow pressure
between 20 psi and 90 psi.
NOTE:
If water pressure varies greatly, or exceeds 90 psi at any
time, a water pressure regulator must be installed. Plumbing
installer must supply the regulator.
Brewer must be connected to a potable water supply. Bloomfield
recommends not less than 1/4” copper tubing for installations of 12’
or less, and not less than 3/8” copper tubing for installations
exceeding 12’. Brewer must be connected to a COLD water line.
NOTE:
DO NOT use a saddle tap for this water line connection.
A shut-off valve must be installed between the main water supply
and the brewer. Plumbing installer must supply the shut-off valve.
A 1/4-turn ball valve is recommended.
Bloomfield highly recommends the use of the provided water
strainer to help prevent deposits in the brewing system.
Flush the water line before connecting to the brewer.
ELECTRICIAN’S INSTALLATION INSTRUCTIONS
Brewer requires a dedicated single-phase circuit:
Model 9220 120/208 Volt AC, 60 Hz 30 Amp circuit
3-Wire (L1, L2, N plus Gnd)
Model 9221 120/240 Volt AC, 60 Hz 30 Amp circuit
3-Wire (L1, L2, N plus Gnd)
NOTE:
To enable the installer to make
a quality installation and to
minimize installation time, these
tests and suggestions should
be completed before the actual
installation is begun.
CAUTION:
Hazard from
Unstable Equipment
Rubber feet must be installed
on each leg of the brewer.
Legs must be adjusted so that
all four feet rest firmly on the
counter. Failure to properly
install the feet can result in
movement of the brewer, which
can cause personal injury and/
or damage to the brewer.
Fig. 2 Adjustable Legs
CAUTION:
Electric Shock
Hazard
Brewer must be properly
grounded to a reliable earth
ground to prevent possible
shock hazard. Do not assume
a plumbing line will provide
such a ground. Electrical shock
may cause serious injury.
SCREW INTO
BREWER
FRAME
ADJUST
FOR
HEIGHT
ATTACH
RUBBER
FEET
Summary of Contents for 9220
Page 20: ...EXPLODED VIEW CABINET AND EXTERIOR COMPONENTS 18 ...
Page 22: ...EXPLODED VIEW INTERIOR COMPONENTS 20 ...
Page 24: ...22 WIRING DIAGRAM ...
Page 25: ...23 NOTES ...