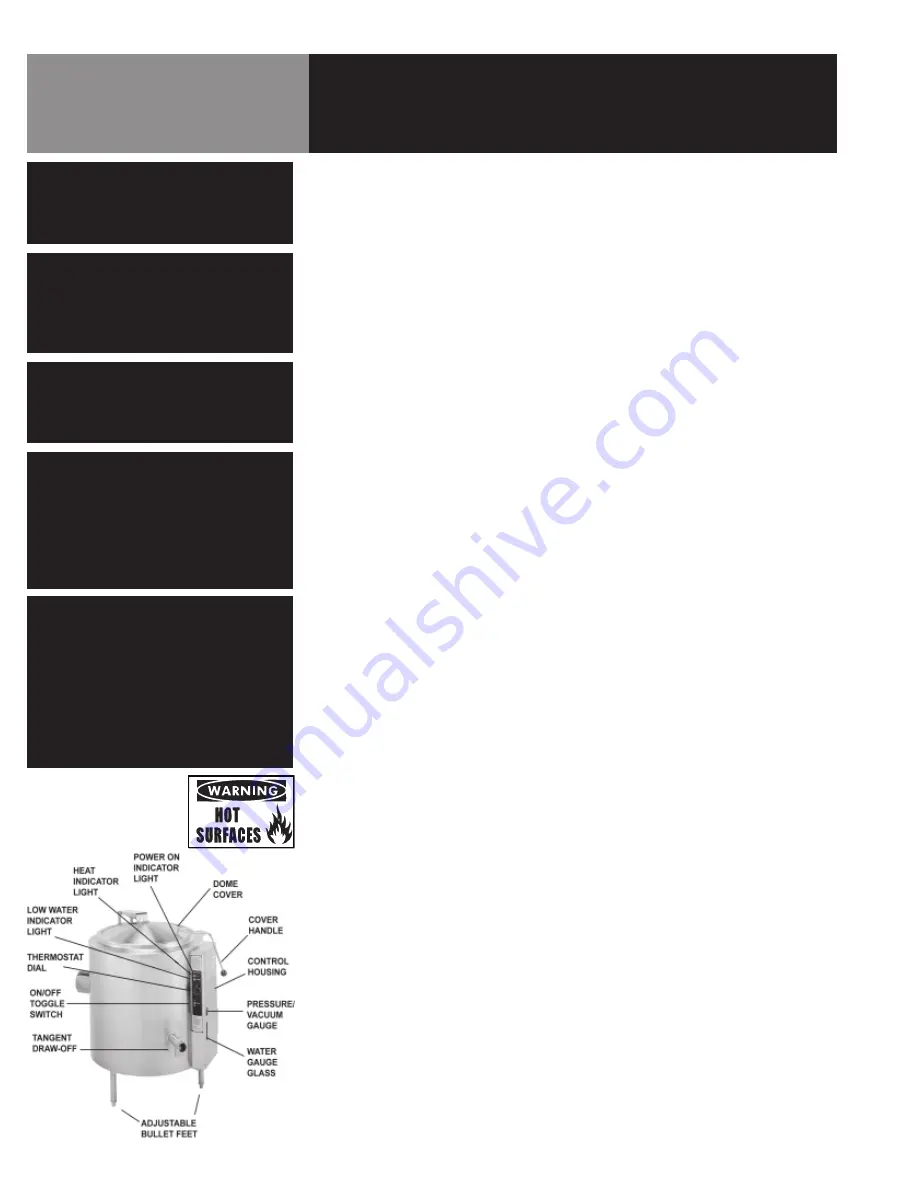
10
OM-40GS-KLS
Operation
A. Controls
Operator controls for the kettle are:
1. Manual gas valve which controls the supply of gas from the main line to
the unit.
2. On-Off (toggle) switch. This switch turns the control circuit power supply on
or off.
3. Thermostat dial, which turns the thermostat on or off, and sets the kettle
operating temperature.
4. Indicator Lights to alert operator of unit conditions:
a. Power On Indicator - shows that the unit is turned on
b. Heat Indicator - indicates that main gas is on to produce steam in the
kettle jacket.
c. Low Water indicator - shows that jacket water is low
d. Unit gas pressure regulator adjustment - located behind the access
door in the kettle skirt.
B. Operating Instructions
1. To Start Kettle
a. CHECK THE WATER LEVEL IN THE JACKET EVERY DAY. The level should
be at the middle of the sight glass. If the level is low, see Jacket
Filling in the Maintenance section of this manual
b. Check the pressure/vacuum gauge. If the gauge does not show 20
to 30 inches of vacuum (i.e. a reading of 20 to 30 below zero), see
Jacket Vacuum in the Maintenance section of this manual.
c. DO NOT attempt to light any burner with a flame.
d. Open main supply gas valve (handle in line with the pipe).
e. Turn the toggle switch to ON. For 90 seconds, or until it succeeds, the
electronic ignition control will attempt to light the pilot.
f. Once the pilot is lit, turn the thermostat to the desired setting.
g. If the pilot does not light, turn it off and wait five minutes. At that time
follow the instructions for starting once again.
h. If the unit repeatedly fails to light, contact an authorized Service
Agency.
WARNING
ANY POTENTIAL USER OF THE EQUIPMENT
MUST BE TRAINED IN SAFE AND CORRECT
OPERATING PROCEDURES.
WARNING
KEEP AREA AROUND KETTLE FREE
AND CLEAR OF ALL COMBUSTIBLE
MATERIALS. DO NOT ATTEMPT TO LIGHT
ANY BURNER WITH A FLAME.
CAUTION
HEATING AN EMPTY KETTLE MAY
CAUSE THE RELEASE OF STEAM FROM
THE SAFETY VALVE.
CAUTION
DO NOT OVERFILL THE KETTLE WHEN
COOKING, HOLDING OR CLEANING. KEEP
LIQUIDS 2-3” (5-8 cm) BELOW THE
KETTLE RIM TO ALLOW CLEARANCE FOR
STIRRING, BOILING PRODUCT
AND SAFE TRANSFER.
WARNING
AVOID ALL DIRECT CONTACT WITH
HOT FOOD OR WATER IN THE KETTLE.
DIRECT CONTACT COULD RESULT IN
SEVERE BURNS. TAKE CARE TO AVOID
CONTACT WITH HOT KETTLE BODY OR HOT
PRODUCT, WHEN ADDING INGREDIENTS,
STIRRING OR TRANSFERRING
PRODUCT TO ANOTHER CONTAINER.
Summary of Contents for 40GS-KLS Series
Page 24: ...22 OM 40GS KLS Parts List...
Page 25: ...OM 40GS KLS 23 Parts List...
Page 27: ...OM 40GS KLS 25 Electrical Schematic...
Page 30: ...28 OM 40GS KLS...
Page 31: ...OM 40GS KLS 29...