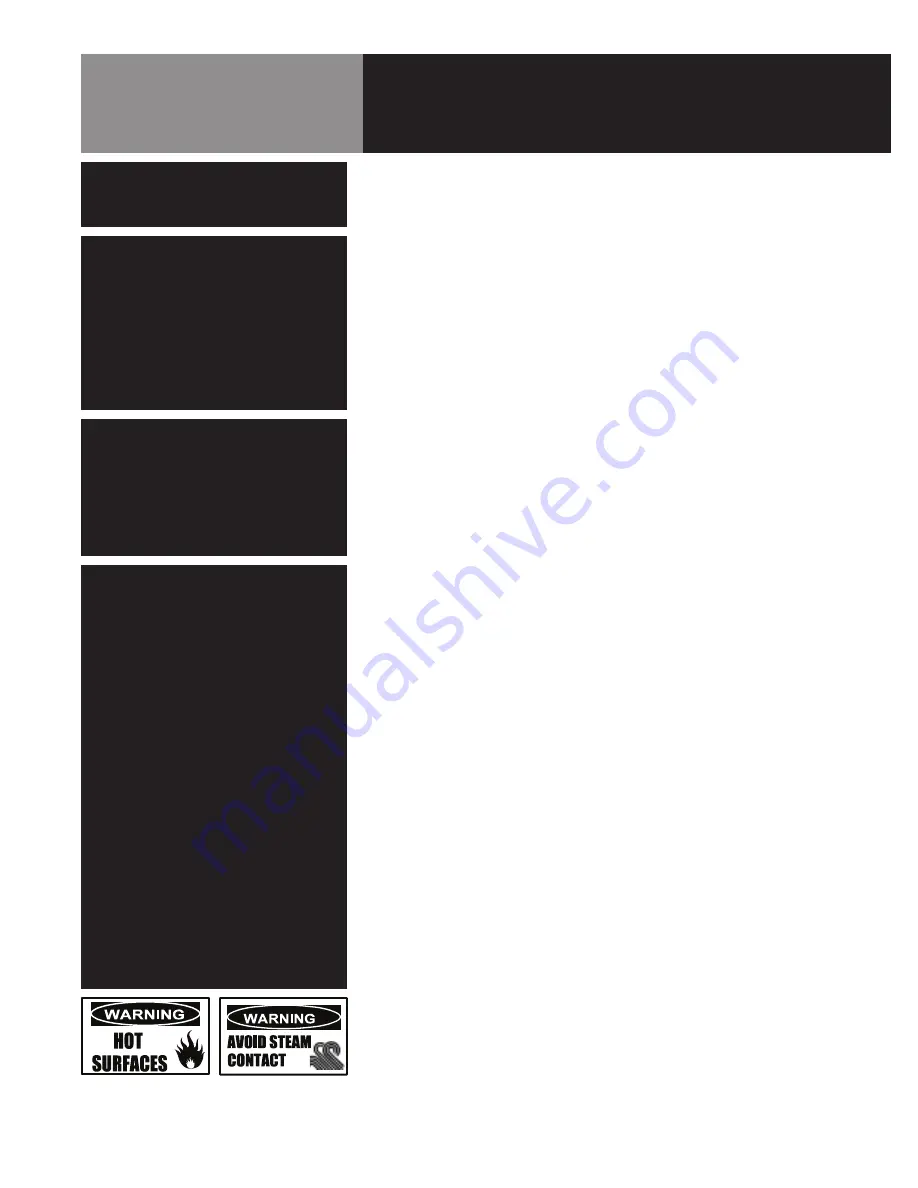
OM-KPT/KLT-DS 9
Operation
Before operating a cold kettle, open the petcock at the bottom of the jacket to drain
any water left by condensing steam. Close the petcock before you open the steam
inlet valve. Draining this water decreases the “hammering” you hear when steam
enters a cold jacket.
To heat the kettle, open the steam inlet valve. Adjusting the inlet valve allows the
operator to control the heating rate. Opening the valve more allows steam to flow into
the jacket faster, and thereby heats the product faster.
The kettle operates efficiently with steam pressures from five PSI to the maximum
working pressure for which the kettle was designed. The maximum allowable
pressure is stamped on the kettle nameplate. It is 25 PSI for standard units.
Once a day, while there is still steam pressure in the jacket, bleed off any entrapped
air and double check the operation of the safety valve. Pull out on its chain, or lift the
lever far enough to let steam escape. Then let it snap back into place to reseat the
valve so that it will not leak.
Tilting the Kettle
To transfer product or empty the kettle: turn the handwheel counterclockwise. The
kettle will hold its position when you stop turning the wheel. If the tilting mechanism
seems to be locked, do not use force to free the kettle. Call for assistance from a
Certified Service Agency, or refer to the Troubleshooting section of this manual.
WARNING
AVOID EXPOSURE TO ESCAPING STEAM,
WHICH CAN CAUSE SEVERE BURNS.
WARNING
AVOID ALL DIRECT CONTACT WITH HOT
FOOD OR WATER IN THE KETTLE. DIRECT
CONTACT COULD RESULT IN SEVERE BURNS.
TAKE SPECIAL CARE TO AVOID CONTACT
WITH HOT KETTLE BODY OR HOT PRODUCT,
WHEN ADDING INGREDIENTS, STIRRING OR
TRANSFERRING PRODUCT TO
ANOTHER CONTAINER.
CAUTION
DO NOT OVERFILL THE KETTLE WHEN
COOKING, HOLDING OR CLEANING. KEEP
LIQUIDS AT LEAST 2-3” (5-8 cm) BELOW
THE KETTLE BODY RIM TO ALLOW
CLEARANCE FOR STIRRING, BOILING
PRODUCT AND SAFE TRANSFER.
WARNING
WHEN TILTING KETTLE FOR PRODUCT
FOR PRODUCT TRANSFER:
1) WEAR PROTECTIVE OVEN MITT AND
PROTECTIVE APRON.
2) USE CONTAINER DEEP ENOUGH TO
CONTAIN AND MINIMIZE PRODUCT
SPLASHING.
3) PLACE CONTAINER ON STABLE, FLAT
SURFACE, AS CLOSE TO KETTLE AS
POSSIBLE.
4) STAND TO LEFT OR RIGHT SIDE OF
KETTLE WHILE POURING – NOT
DIRECTLY IN POUR PATH OF HOT
CONTENTS.
5) POUR SLOWLY, MAINTAIN CONTROL
OF KETTLE AT ALL TIMES, AND
RETURN KETTLE BODY TO UPRIGHT
POSITION AFTER CONTAINER IS
FILLED OR TRANSFER IS COMPLETE.
6) DO NOT OVERFILL CONTAINER. AVOID
DIRECT SKIN CONTACT WITH HOT
CONTAINER AND ITS CONTENTS.