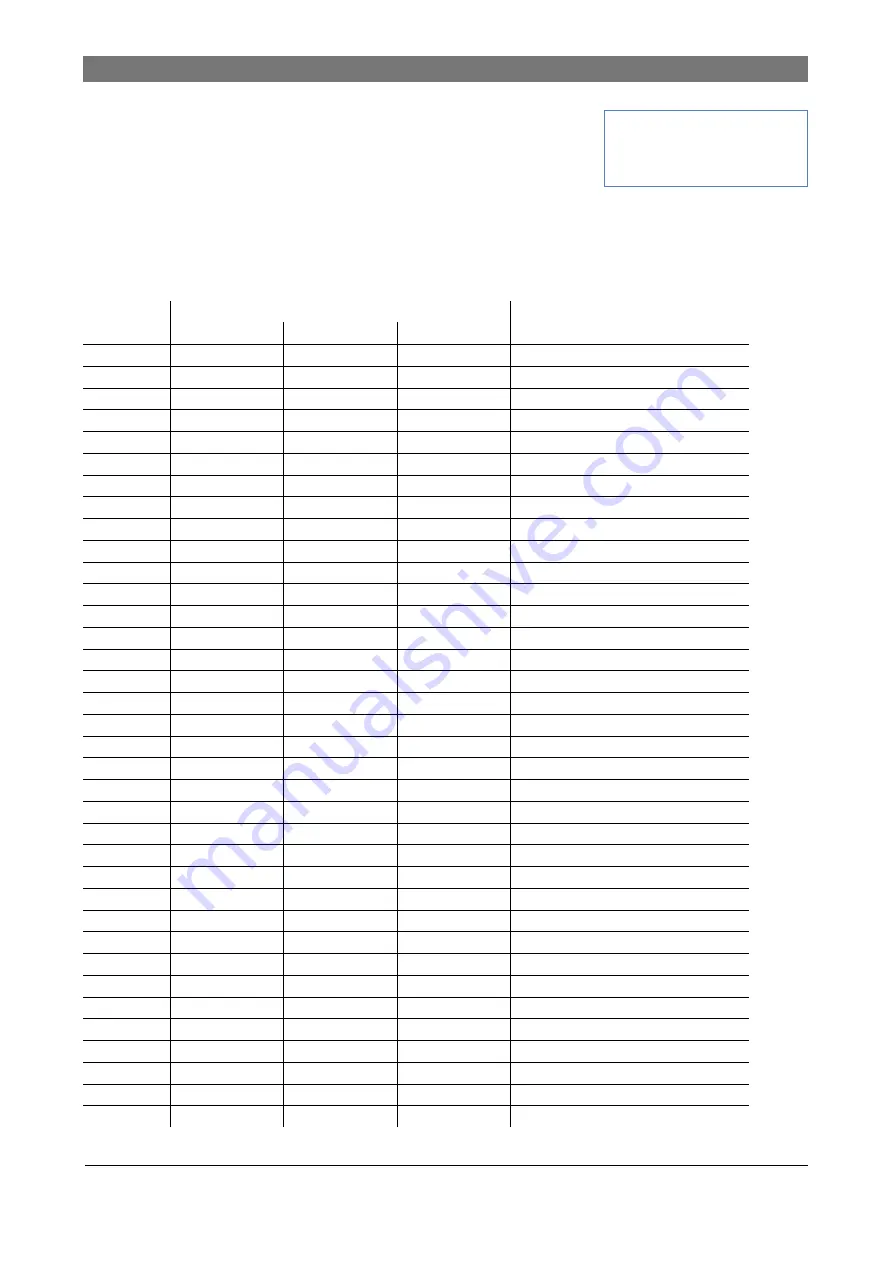
INSPECTION BOOK DUPLEX-S2
45
117127
● 07/2011
Maintenance report
Always record carried out
maintenance work.
Tick if appropriate.
Date
Maintenance report
carried out by
monthly
annually
biannually
Keep completed form
in inspection book
(Annex)!
Type ……………………………….
Serial number:
…………………………………….
Summary of Contents for DUPLEX S2
Page 2: ......
Page 4: ......
Page 14: ...3 The lift 8 117127 07 2011 ...