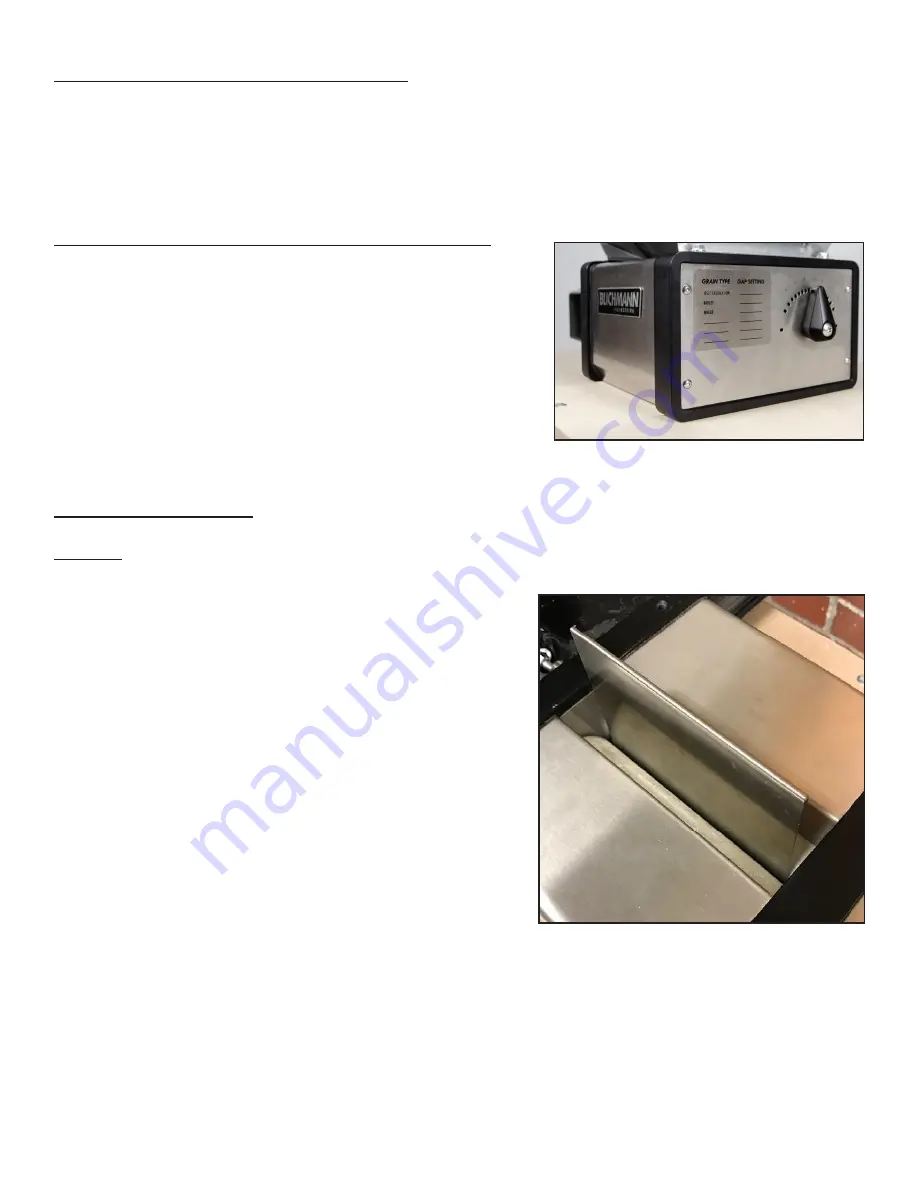
Grain Mill
© Blichmann Engineering, LLC 2020
For replacement parts, visit: blichmannengineering.com/genuine-replacement-parts
2
Custom Mounting Solutions:
See the attached drawing for mounting your mill on a custom stand, cabinet, or grain handling system.
The bolt pattern is the same for the top and bottom of the mill. Use M6x1 hardware for mounting the mill
or custom hopper or grain handling equipment. Ensure there is at least 10mm (7/16”) of the bolt engaged
with the threads. For example, if you are mounting to 3/4” plywood (19mm), use at least 30mm long bolts.
Temporary thread lock applied to threads is acceptable if preferred.
Sticker installation and instruction:
Place the included gap setting sticker on the adjustment side of
the mill. There are 3 types of malt listed for you. The .055” gap is
the setting that produces a proven “Normal” rating crush with
fresh two row barley. See the calibration instructions for how to
determine this gap setting. Document your preferred setting on
the space provided for your records. Use the other open spaces
for your own preferred gap setting for other grain.
Gap Calibration:
Warning: Moving parts can crush and cut. Do not operate the mill without hopper and guard
installed. Unplug or lockout device before servicing.
Ensure the unit is un-plugged, and the guard is removed before
proceeding. Included with your grain mill is a calibration plate
to be used for finding the proper gap setting that produces
an ASBC “normal” grist crush. You will be able to produce a
“normal” crush at 0.055” (1.4mm). The Blichmann mill operates
with synchronized rollers with a large diameter which does
not require a close gap to produce a desirable crush. To set the
mill at this gap, pull the adjustment knob and rotate clockwise
to the widest setting (18). Insert the plate into the top of the
mill between the rollers. Pull the adjustment knob and rotate
counterclockwise until rollers contact the gap tool. Document
this number with permanent marker on the label provided.
Measure the performance of the mash and make small gap
adjustments to the gap setting if needed to improve efficiency
without sacrificing sparge and recirculation rates.