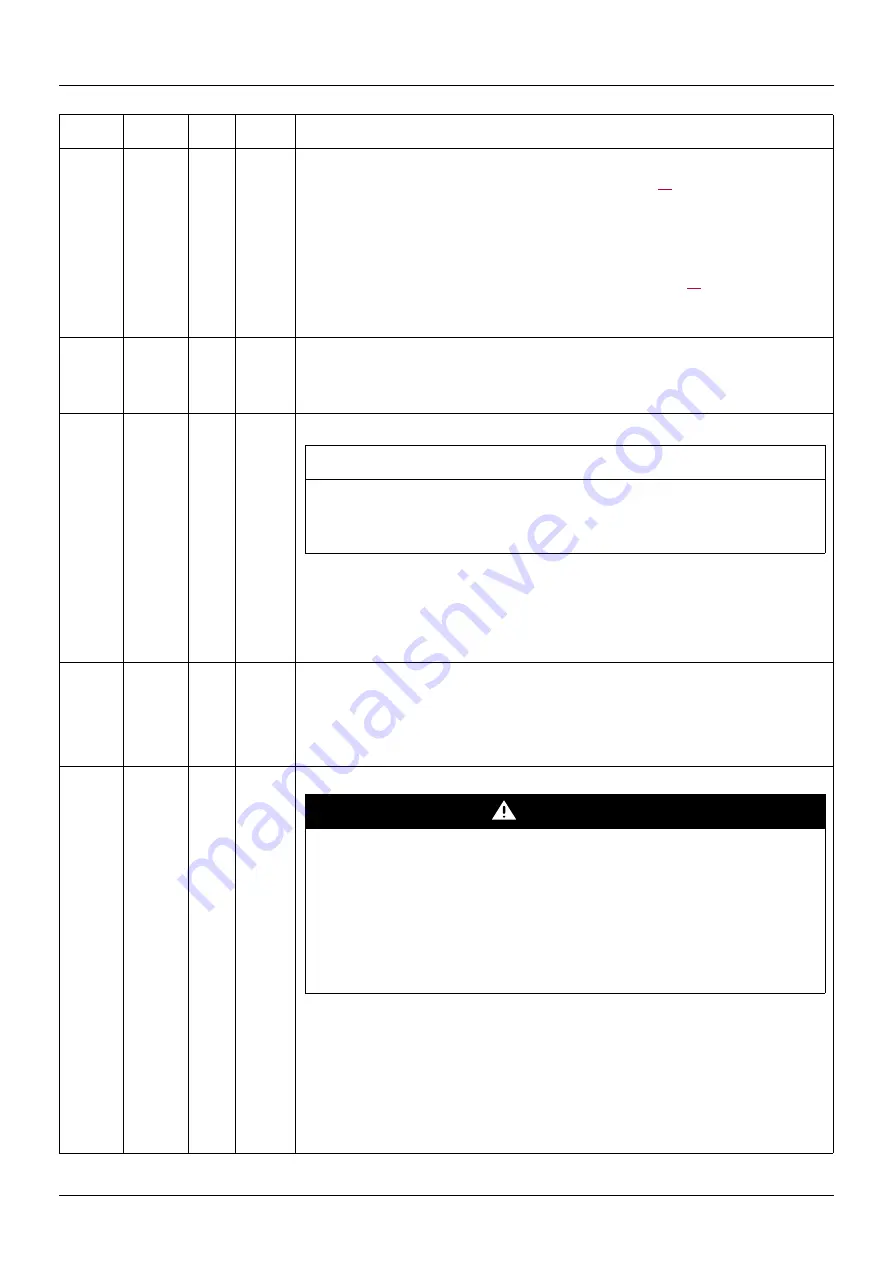
54
Configuration and adjustment variables
Modbus
address
CANopen
address
Code
Read/
Write
Name/Description/Possible values
7003
2028 / 4
LFL
R/WS
Stop mode in the event of a loss of 4 - 20 mA signal (LFF)
Factory setting: 0
0 = "nO": Ignored (only value possible if CrL3
y
3 mA, see page
)
1 = "YES": Freewheel stop
4 = "LFF": The drive switches to the fallback speed (LFF parameter)
5 ="rLS": The drive maintains the speed at which it was operating when the loss occurred, and
this speed is saved and stored as a reference until the signal is restored.
6 = "rMP": Stop on ramp
7 = "FSt": Fast stop
The factory setting of LFL is forced to YES if CrH3 < CrL3 (see page
) and nO is impossible.
Note: Before setting LFL to YES, rMP or FSt, check the connection of input AI3. Otherwise, the
drive may immediately switch to an LFF fault detection code.
7080
2028 / 51
LFF
R/WS
Fallback speed
Unit: 0.1 Hz
Factory setting: 100
Adjustment range: 0 to 5000
Fallback speed setting for stopping in the event of a detected fault.
7007
2028 / 8
drn
R/WS
Derated operation in the event of an overvoltage
CAUTION
RISK OF DAMAGE TO THE DRIVE
If drn is set to YES, use a line choke (see catalog).
Failure to follow these instructions can result in equipment damage
Lowers the trip threshold of the USF fault detection in order to operate on line supplies with 50%
voltage drops.
Factory setting: 0
0 = "nO": Function inactive
1 = "YES": Function active
In this case, a line choke must be used and the performance of the drive may be derated.
7004
2028 / 5
StP
R/WS
Controlled stop on mains power break
Factory setting: 0
0 = "nO": Locking of the drive and freewheel stopping of the motor
1 = "MMS": This stop mode uses the inertia to maintain the drive power supply as long as
possible.
2 = "rMP": Stop according to the valid ramp (dEC or dE2)
3 = "FSt": Fast stop, the stopping time depends on the inertia and the braking ability of the drive.
7125
2029 / 1A
InH
R/WS
Fault detection inhibition assignment
DANGER
LOSS OF PERSONNEL AND EQUIPMENT PROTECTION
• Enabling the fault inhibition parameter (InH) will disable the drive controller protection
features.
• InH should not be enabled for typical applications of this equipment.
• InH should be enabled only in extraordinary situations where a thorough risk analysis
demonstrates that the presence of adjustable speed drive protection poses a greater risk
than personnel injury or equipment damage.
Failure to follow these instructions will result in death or serious injury
Disables all the drive protection devices.
Factory setting: 0
0 = "nO": Not assigned
129 = "LI1": Logic input LI1
130 = "LI2": Logic input LI2
131 = "LI3": Logic input LI3
132 = "LI4": Logic input LI4
133 = "LI5": Logic input LI5
134 = "LI6": Logic input LI6
Fault monitoring is active when the input is at state 0. It is inactive when the input is at state 1.