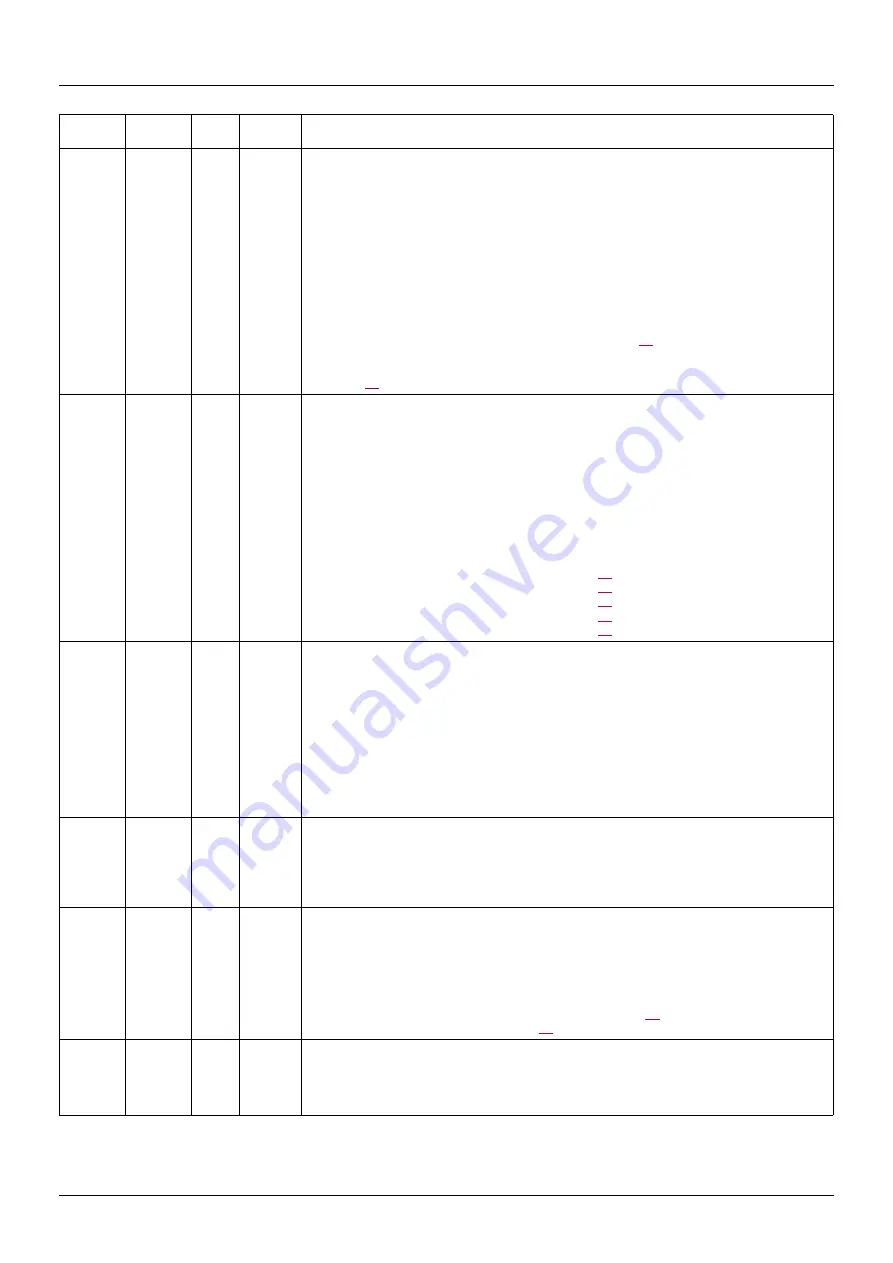
52
Configuration and adjustment variables
Modbus
address
CANopen
address
Code
Read/
Write
Name/Description/Possible values
3110
2001 / B
FLr
R/WS
Flying restart (automatic catching a spinning load on ramp)
Factory setting: 0
Used to enable a smooth restart if the run command is maintained after the following events:
- Loss of line supply or disconnection
- Reset of current detected fault or automatic restart
- Freewheel stop
The speed given by the drive resumes from the estimated speed of the motor at the time of the
restart, then follows the ramp to the reference speed.
This function requires 2-wire control (tCC = 2C) with tCt = LEL or PFO.
0 = "nO": Function inactive
1 = "YES": Function active
When the function is operational, it activates on each restart following one of the above events,
resulting in a slight delay (1 second max).
FLr is forced to nO if brake control (bLC) is assigned (page
).
Note: Do not use the flying restart function (FLr = YES) with auto-tuning on power-up (rSC or
POn page
).
7131
2029 / 20
EtF
R/WS
External fault
Factory setting: 0
0 = "nO": Not assigned
129 = "LI1": Logic input LI1
130 = "LI2": Logic input LI2
131 = "LI3": Logic input LI3
132 = "LI4": Logic input LI4
133 = "LI5": Logic input LI5
134 = "LI6": Logic input LI6
If LAC = L3 and LEt = HIG, the following assignments are possible:
171 = "Cd11": bit 11 of the CMD control word (page
) written by Modbus or CANopen
172 = "Cd12": bit 12 of the CMD control word (page
) written by Modbus or CANopen
173 = "Cd13": bit 13 of the CMD control word (page
) written by Modbus or CANopen
174 = "Cd14": bit 14 of the CMD control word (page
) written by Modbus or CANopen
175 = "Cd15": bit 15 of the CMD control word (page
) written by Modbus or CANopen
7090
2028 / 5B
LEt
R/WS
Configuration of external fault detection
Factory setting: 1
0 = "LO": The external fault is detected when the logic input assigned to EtF changes at state 0.
Note: In this case, the external fault can not be assigned to a bit of Modbus or CANopen control
word.
1 = "HIG": The external fault is detected when the logic input or the CMD control word bit
assigned to EtF changes at state 1.
Note: If LEt = HIG, EtF is assigned to a bit of Modbus or CANopen control word and there is
no EtF detected fault, the change to LEt = LO causes an EtF external detected fault.
In this case, It is necessary to switch off then to switch on the drive.
7006
2028 / 7
EPL
R/WS
Stop mode in the event of an external fault EPF
Factory setting: 1
0 = "nO": External fault ignored
1 = "YES": Freewheel stop
6 = "rMP": Stop on ramp
7 = "FSt": Fast stop
9611
2042 / C
OPL
R/WS
Configuration of motor phase loss detection
Factory setting: 1
0 = "nO": Function inactive
1 = "YES": Triggering of OPF detected fault
2 = "OAC": No OPF fault triggered but management of the output voltage in order to avoid an
overcurrent when the link with the motor is re-established and flying restart even if FLr = nO.
To be used with downstream contactor.
OPL is forced to YES if brake control bLC is assigned (page
).
If OPL = OAC, bLC is forced to nO (page
).
7002
2028 / 3
IPL
R/WS
Configuration of line phase loss detection
Factory setting: 1 except for ER23
ppp
M2: 0
This parameter is only active on 3-phase drives.
0 = "nO": Ignored
1 = "YES": Fast stop