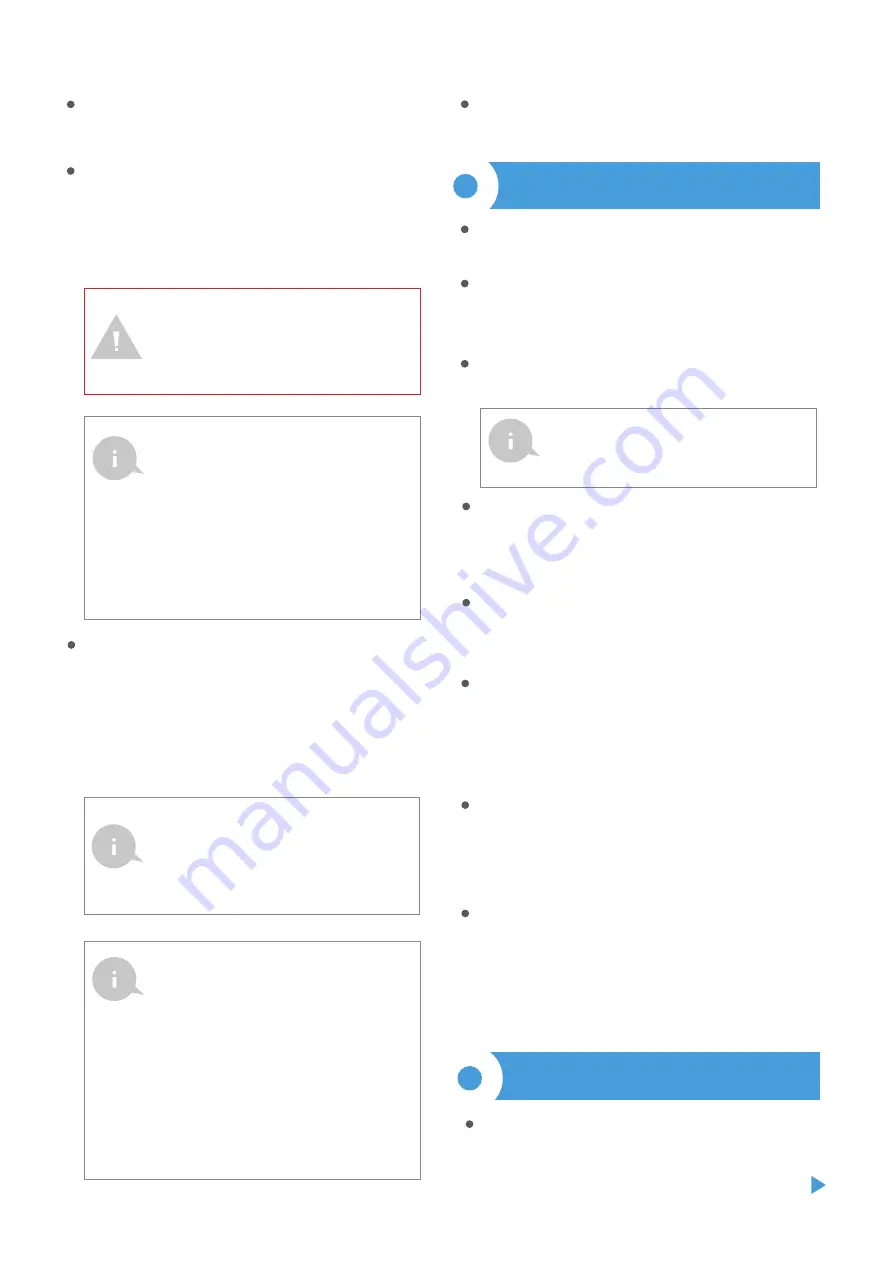
Go to "Settings" (icon in the upper right corner of the screen), go to the "Gate
settings" section and select the appropriate option in the "Gate type" field.
Then, depending on your control panel, select the function of the second
(auxiliary) output. After saving the settings, go to the main panel by clicking
the arrow in the upper left corner. Test the controller work of by clicking the
gate / door icon - the control panel should force the motor to move.
In the "Gate settings" section, in the field "Address (URL) of the MJPEG stream"
you can enter the URL stream of the camera IP which supervise the motor.
In case you need to make changes in the advanced controller settings,
click on "Show advanced" button. Will appear additional options.
In the "Gate output type" field, the output behavior can be changed between
the normally open output (NO - when the output is not shorten) or normally
closed (NC - in other words the contact pair is shorten, opens when the user
presses the control button). It is also possible to adjust the duration of the
impulse in the output - between 0.1 sec. to 15 seconds - after a single press of
the control button. The option "Outputs swap" allows you to correct the order
of pairs of wires without switching them again, for example when the gate
control wire has been connected to the O2 output instead of under O1.
Go to the main panel by clicking the arrow in the upper left corner. If the
motor position sensor circuit has been connected, test the gate work - click on
the gate / door icon, the control panel should force the motor to move. Note
the blue border around the icon. If the motor is in an intermediate position,
the icon's border will be half blue and half gray. The limit position in the
"Open" state is indicated by a gray border and in the "Closed" state by a blue
border.
If you need to change the advanced settings of the controller associated with
the inputs, return to the controller settings, go to the "Gate settings" section
and then click the "Show advanced" button. Will appear additional options. If
despite the correct wiring, the controller can not detect the motors position,
is possible to change the detection method of the limit switches connected to
IN1 / IN2 inputs. If the state of the motor position is detected inversely, i.e. the
motor is physically in the closed position and the visualization indicates that it
is open, it means that the pairs of wires in the IN1 / IN2 inputs have been
changed, so the option should be changed in the field "Inputs swap (IN1, IN2)"
to "Enabled".
Download the
free wBox application
. If you have an Android mobile device,
you will find the application in the Play Store. For iOS devices the application is
in the App Store.
By using your mobile phone or tablet, connect it to the device wireless
network. To do this, enter to your smartphone or tablet settings, then go to
setting of the WiFi network and find the network name "gateBoxPro-
-xxxxxxxxxx” where xxxxxxxxxx is the serial number of the device. Connect to
this network.
Open the wBox application. A device will appear at the top of the screen. To
add it to the application, click on "+" on the right side of the name. To pre-
configure the controller, click on the default device name.
2
FIRST START
You can also set the configuration using the web browser
of your phone / tablet. After connecting to the wireless
network of the controller, turn on the browser and go
website www.blebox.eu
The meaning states of the limits detected in the IN1 / IN2
inputs (it mean which of the IN1 or IN2 inputs indicates the
closed position and which the open position) can be
changed in the controller settings menu in the option
"Replace inputs".
The limit state is detected if there is a current flowing between the IN1
and COM connectors and between the IN2 and COM does not.
Analogously, the opposite state will be detected when there is no
current flowing between the IN1 and COM connectors, and will flow
between the IN2 and COM connectors. Any other configuration of the
current flow is equivalent to the motor position beyond the limit
positions. Inputs IN1, IN2 and COM have no specific polarity, they are
galvanically isolated from the rest of the controller. The range of
allowable voltages on the individual input pairs is 12 - 24V AC / DC.
Information advanced for installers regarding inputs,
when is connected to a motor control panel for which is
not available diagram.
Read the diagram and then proceed to install the controller. Pay particular
attention to the designation of the controller connectors. Start by connecting
the + 12V / + 24V power wires (red or black with a white dotted line) and GND
(black).
Paying attention to the polarity, connect the inputs controlling the engine
control panel. Depending on the control panel, will be necessary to connect
one or two inputs. The controller output O1 is destined for control in the open
/ stop / close mode. The O2 output is an auxiliary output, applicable in the
control panel requiring a connection stop circuit when the motor works, or
may be used as an additional function, e.g. "wicket" if the control panel is
equipped with this functionality.
After making sure that the device is connected in accordance with the
diagram and that there are no metal components near the controller which
may accidentally cause short-circuit, start the device by turning on the power
(turning on the mains fuse or connecting the power cord to the power outlet).
If the motor has electromechanical limits switch, it is possible to receive
feedback from the controller, indicating the position of the motor in the
positions "Open" (intermediate position) "Closed". To do this, connect input
IN1 of the controller to the connector of the motor control panel which
indicates the closed position of the motor (usually FTC, SWC, FC), the IN2 input
should be connected to the connector indicating the open position of the
motor (usually FCO, SWO, FA), while the common COM input of the controller
should be connected to the corresponding common signaling of the motor
control panel . The connection polarity of the controller inputs is not
significant.
It is necessary to connect the right pin of the given output
(O1 / O2) so that it has a higher potential than the left pin.
In case of an inverted connection, due to the internal
construction, it will connect the output which may cause
the movement of the motor even without control it. In this
situation, it is necessary to reverse the pair of wires
connected inside output.
Pay attention to the maximum output current
capacity - the control current cannot exceed 20mA
per output. Overloading the output will cause
irreparable damage to the controller.
Information advanced for installers in relation to the
output polarity, when is connected to engines control
panels for which the scheme is not available.
3
ACCESS POINT AND WIFI NETWORK SETTINGS
Once you turn on the controller for the first time, you can proceed to its
further configuration. Being connected to the WiFi network emitted by the
device, in the control panel of the wBox application select the device, then go
to “Settings” (icon at the top-right corner of the screen).