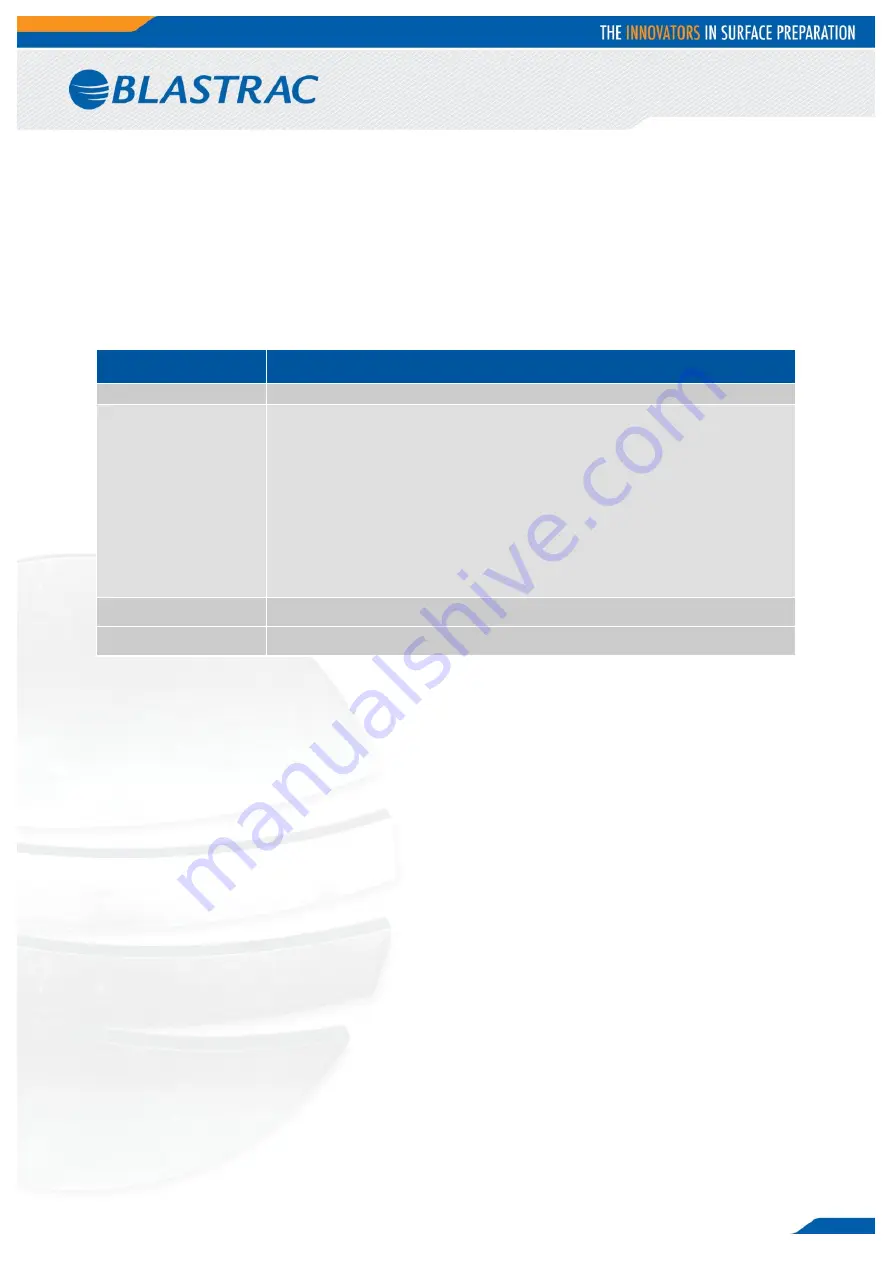
31
6. Maintenance
Pay attention to Chapter 3
"Safety"
during maintenance and repair works.
Failures due to inadequate or incorrect maintenance may generate very
high repair costs
and long standstill
periods of the machine.
Regular
maintenance therefore is imperative.
Operational safety and service life of the machine depends, among other things, on proper maintenance.
The following table shows recommendations about time, inspection and maintenance for the normal use of the
machine.
Operating hours/
time period
Inspection points, maintenance instructions
12 h after repairing
Check all accessible screw connections for tight seat.
Daily and prior to
starting work
Check that all safety devices working adequate.
Check whether there is any foreign matter between the sawing blades.
Clean the sawing blades especially in case of moist surfaces.
Check the sawing blades, lateral axles, tools and housing for wear.
Check the tension of the belt, stretch again if necessary.
Check the electric connections for sediments of dirt or foreign bodies.
Check the electric motors for dirt and other contaminants.
Check the function of the residual current operated device.
Check the hose connections for tightness and fixed seat.
Make sure that the dust bin is emptied.
Check the oil level in the hydraulic reservoir.
Every month
Grease the bearing.
Annually
Full overhaul and cleaning of the complete machine.
The time indications are based on uninterrupted operation. When the indicated number of working hours is not
achieved during the corresponding period, the period can be extended. However a full overhaul must be
carried out at least once a year.
Due to different working conditions it can’t be foreseen how frequently inspections for wear check’s,
inspection, maintenance and repair works ought to be carried out. Prepare a suitable inspection schedule
considering your own working conditions and experience.
Pay attention to unusual noises or strong vibrations. Check for the cause of every big change. Call a technician
if you have doubts about the cause or when a repair without a technician seems not possible without damages.
Only use genuine Blastrac spare parts.
Our specialists will be happy to assist you with more advice.
Prior to any repair works on the machine and its drives, secure the machine against unintentional
switching on. Put the machine to its safety off position.
The machine is in a safe condition when it cannot generate any hazard.
Follow additional operating and maintenance of instructions of original equipment manufacturer if
included during your service and maintenance work.
Further is advised:
Store the cleaned and dry machine in a dry and humid free room. Protect the motors from moisture, heat,
dust and shocks.
All repair work must to be done by qualified Blastrac personnel, this to guarantee a safe and reliable machine.