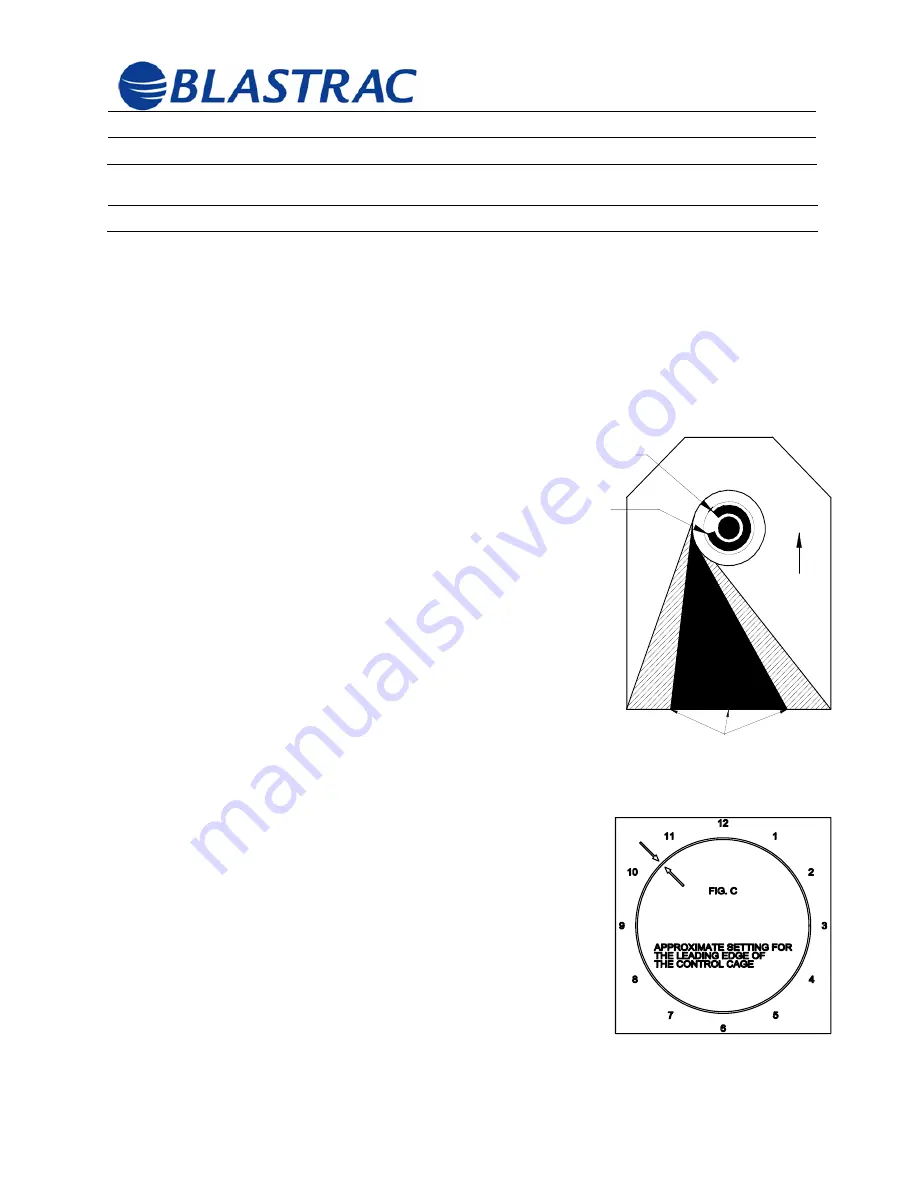
Operating Instructions 1-9DEZ
Setting The Correct Blast Pattern August 2005
5.1 Cont’d
5. The initial setting of a machine rotating in a counter-clockwise direction should be
between 8:30 and 10:30 as indicated in Figures B and C. The resultant-cleaning
path will determine the final setting.
These settings will vary with the abrasive size and the surface being cleaned. Once
the proper control cage setting is obtained, the blast pattern should remain
consistent. If the pattern begins to vary, check the blast wheel components for wear.
Control Cage “Trial & Error” Setting
The initial setting of the control cage for a machine
that has the blast wheel rotating in a counter-
clockwise direction is between 8:30 and 10:30.
The leading edge should be at 10:30. Refer to
Figures A, B and C. Place a 3/16” or 1/4” steel
plate beneath the machine and blast with the
abrasive control valve at full open for about 45
seconds. Do not move the machine during this
test. The resulting “hot spot” should be centered
as it appears on Figure B. If the “hot spot” is too
far to the left, rotate the control cage in a counter-
clockwise direction about 1/4” and recheck the
blast pattern on the test strip. Small changes in the
rotation of the control cage can move the “hot spot
“significantly. If the “hot spot” is too far to the right,
rotate the control cage in a clockwise direction. Once
again, move the control cage in small increments until the
blast pattern (“hot spot”) is centered.
Note:
If the blast pattern cannot be centered, check the
blast wheel and be sure it is properly mounted and seated
on the wheel hub located behind the blast wheel. The two
pins on the hub must be seated on the back of the blast
wheel before the wheel can be secured. This check must
be made whenever the blast wheel is changed.
"HOT SPOT"
PRIMARY CLEANING AREA DIRECTED AT SURFACE.
PROPER SETTING REQUIRED.
LEADING EDGE OF CONTROL CAGE
SET AT APPROXIMATELY 10:30
LEADING
EDGE
TRAILING
EDGE
WHEEL
ROTATION
FIG. B
22
Summary of Contents for 1-9 DEZ
Page 1: ...MODEL 1 9 DEZ 8 17 05...
Page 4: ...i...