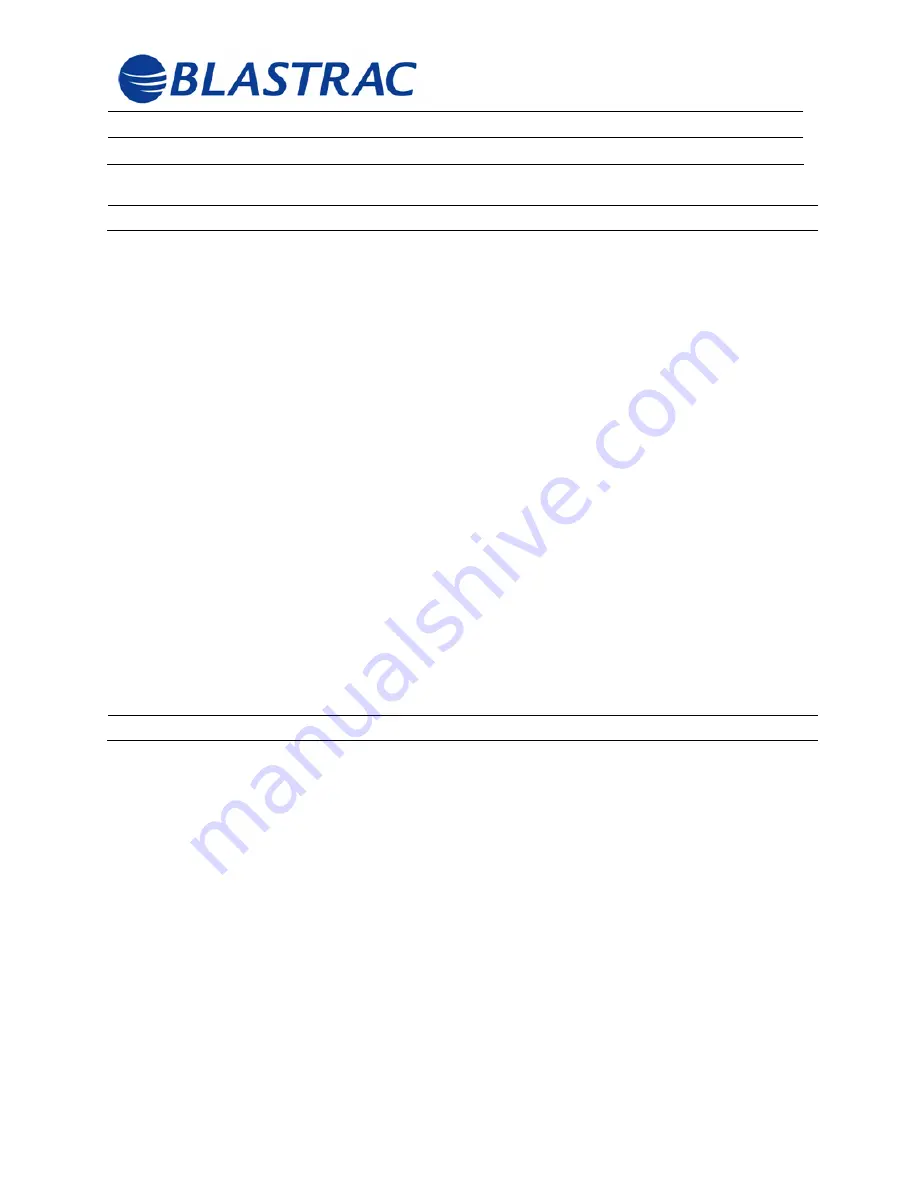
Operating Instructions
1-9DEZ
Description and Function
August 2005
11
3.2 Blast Unit – Abrasive Cleaning Head
This section (3.2) refers to 3.1.2 on page 14.
The center of the patented abrasive cleaning head is the four bladed, six-inch blast
wheel that accelerates the abrasive towards the surface being cleaned. This center fed
blast wheel propels the abrasive by centrifugal force at a speed of more than 200 mph.
This blast wheel is enclosed in an abrasion resistant housing that is also lined with
abrasion resistant liners. These liners are located in areas where the most wear is
present. The operator must change them periodically to protect the housing. The blast
wheel is directly connected to an 8,000 RPM (no-load), 110V angle grinder.
The blast wheel is equipped with a cast in place impeller for easy maintenance. This
impeller pre-accelerates the abrasive to the wheel blades in controlled portions. The
impeller also acts as a timing device to ensure proper placement of abrasive on the
blade face. Abrasive that is gravity fed to the center of the wheel is pre-accelerated by
impeller segments and directed through the control cage. The control cage determines
where the abrasive is introduced onto the rotating blades of the wheel which in turn
determines where the abrasive is being “aimed”. The setting of the control cage is very
important when setting up the “blast pattern.” Refer to Section 5 for setting the correct
blast pattern.
3.3 Blast Unit – Abrasive Control Valve
This section (3.3) refers to Figure 3.1.3 on page 15.
The abrasive control valve regulates the amount of abrasive delivered to the blast
wheel. The main component of this device is a butterfly valve surrounded by a
magnetic strip. A slight gap exists between the disk on the butterfly assembly and the
inner wall of the valve. When the disk is horizontal, the magnetic strip provides a seal
that closes the gap with steel shot and stops the flow of abrasive. The valve is manually
operated with the actuator below the handle. Should the abrasive valve need to be
replaced, the lever arm should be oriented at approximately 45 degrees when the valve
is closed (see figure 3.1.3) after inserting the new valve.
Summary of Contents for 1-9 DEZ
Page 1: ...MODEL 1 9 DEZ 8 17 05...
Page 4: ...i...