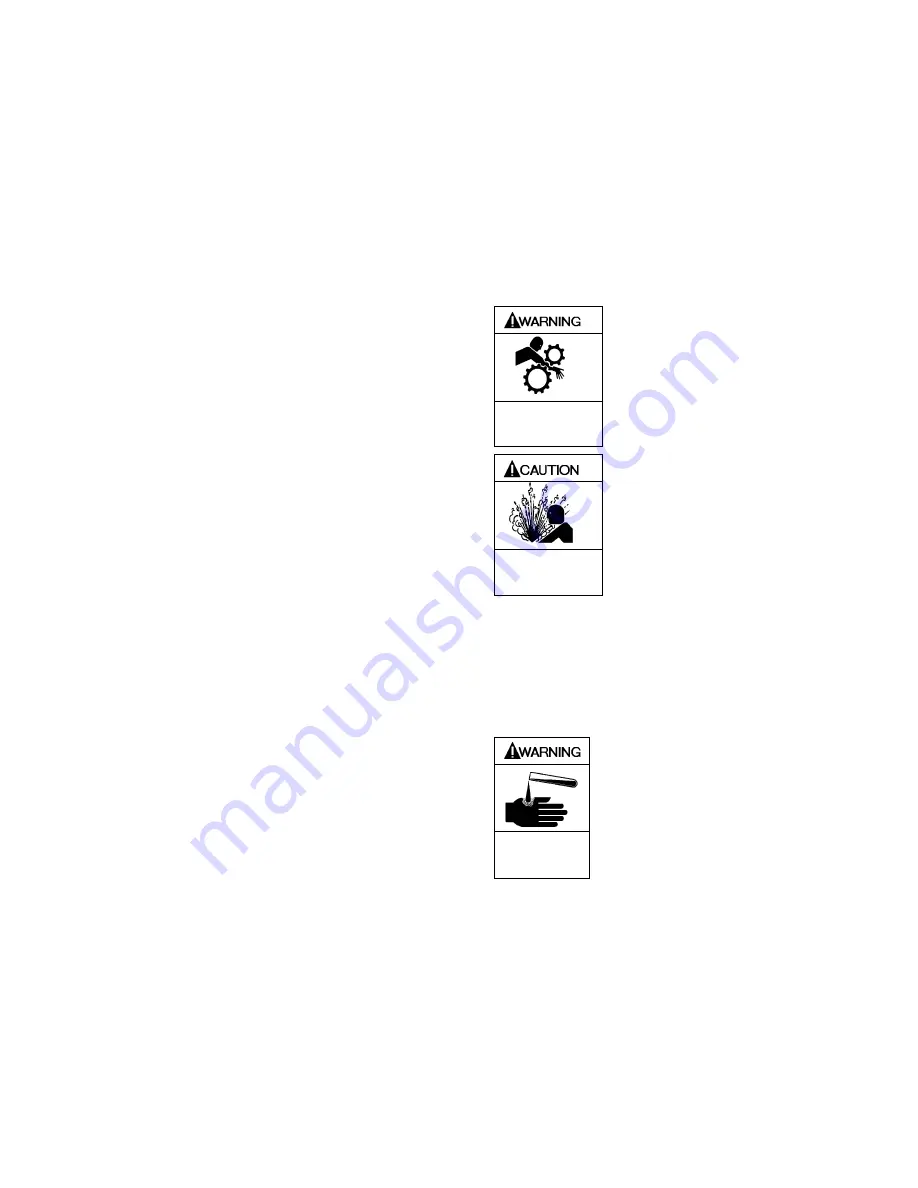
205-B00 page 5/12
OPERATION
PUMP SPEED
PTO and hydraulically driven units MUST contain speed
control devices to prevent pump speeds above the maximum
RPM specifications, regardless of the truck engine unloading
speeds. If fluid delivery is less than expected, see the
"General Pump Troubleshooting" section
REVERSE ROTATION
NOTICE:
When pumps are operated in reverse a separate pressure
relief valve must be installed to protect the pump from
excessive pressure.
It may be desirable to run the pump in reverse rotation for
system maintenance. The pump will operate satisfactorily in
reverse rotation for a LIMITED time, at a reduced
performance level. When operating the pump in reverse, a
separate bypass valve MUST be installed to protect the pump
from excessive pressure.
FLUSHING THE PUMP
NOTICE:
If flushing fluid is to be left in the pump for an extended
time, it must be a lubricating, non-corrosive fluid. If a
corrosive, non-lubricating fluid is used, it must be
flushed from the pump immediately.
To flush the pump, use the following procedure:
1. Allow the pump to evacuate as much fluid as possible.
2. Run cleaning fluid through the pump intake. The cleaning
fluid should be compatible with the pump O-rings and
vane material. When handling "sticky" fluids that solidify
within the pump (i.e., waxes, adhesives, resins, asphalts,
etc.), use a fluid that will prevent solidification of the fluid
being transferred and facilitate flushing.
3. Operate the pump against a closed discharge for 15
seconds to allow the cleaning fluid to recirculate through
the internal relief valve.
NOTICE:
After flushing the pump some residual fluid will remain in
the pump and piping.
NOTICE:
Properly dispose of all waste fluids in accordance with
the appropriate codes and regulations.
RELIEF VALVE
NOTICE:
The pump internal relief valve is designed to protect the
pump from excessive pressure and must not be used as
a system pressure control valve.
Pumping volatile liquids under suction lift may cause
cavitation. DO NOT partially close the discharge valve. This
WILL result in internal relief valve chatter. For these
applications, install an external bypass valve, and any
necessary piping, back to the storage tank. Use a bypass
system when operating for extended periods (more than 1
minute) against a closed discharge valve.
Failure to disengage pto before
adjusting pump relief valve can cause
severe personal injury or death
Hazardous Machinery
can cause severe
personal injury or death
Incorrect settings of the pressure
relief valve can cause pump
component failure, personal injury,
and property damage.
Hazardous pressure can
cause personal injury or
property damage
RELIEF VALVE SETTING AND
ADJUSTMENT
The relief valve pressure setting is marked on a metal tag
attached to the valve cover. Generally, the relief valve should
be set at least 15 - 20 psi (1.0 - 1.4 Bar) higher than the
operating pressure, or the external bypass valve setting (if
equipped).
Relief valve cap is exposed to pumpage
and will contain some fluid
Hazardous or toxic
fluids can cause
serious injury.
DO NOT remove the R /V Cap OR adjust the relief valve
pressure setting while the pump is in operation.
1.
To INCREASE the pressure setting,
remove the relief
valve cap, loosen the locknut, and turn the adjusting
screw
inwar
d, or clockwise. Replace the valve cap.
2.
To DECREASE the pressure settin
g, remove the relief
valve cap, loosen the locknut, and turn the adjusting
screw
outwar
d, or counterclockwise. Replace the valve
cap.
Refer to the individual Blackmer pump parts lists for various
spring pressure ranges. Unless specified otherwise, pumps
are supplied from the factory with the relief valve adjusted to
the mid-point of the spring range.