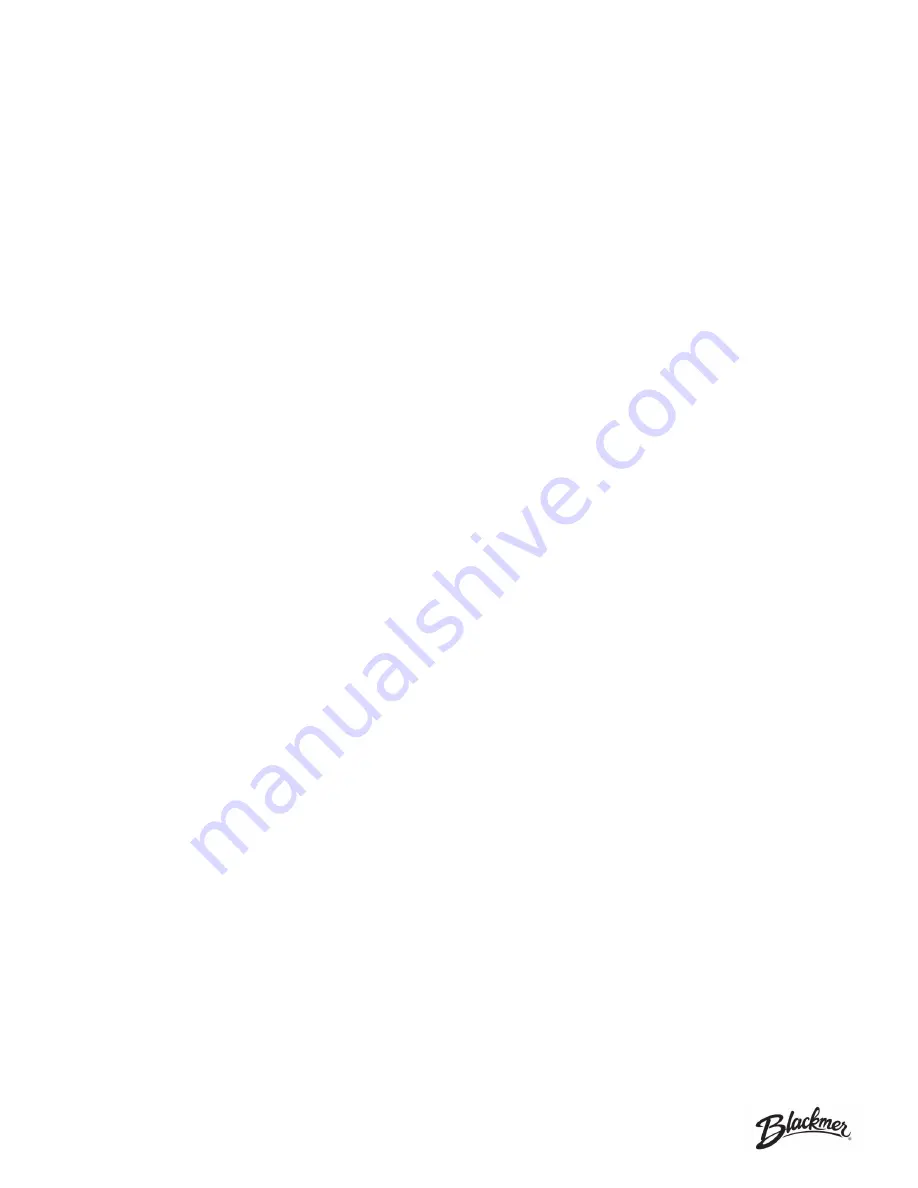
1901-a00
19
START UP
Check to ensure that the pressure/vacuum gauges are installed on inlet and discharge side of the pump.
Check to ensure that installation and piping are correctly fastened and supported.
Check to ensure that the pump and driver are properly aligned. Refer to
Alignment
section.
Verify that the motor is wired correctly. Check to ensure that the thermal overload relays are properly sized and set for
operation.
With motor/driver locked out, check that the pump rotates by hand.
Jog motor to validate correct rotation.
Check to ensure that the coupling guard and all other safety-related devices and instrumentation are in place and in
working order.
Check to ensure that the pressure relief valve is installed correctly.
Open suction, discharge and any auxiliary valves, such as in-line PRV loops, to ensure proper flow into and out of pump.
Prime pumping chamber if possible.
If pump handles pumpage at temperature greater than 93°C (200°F), the pump should be gradually warmed until its
temperature is within 38°C (100°F) of intended operating temperature.
Start pump. If flow is not achieved in 30 seconds shut off immediately. “Dry” running a pump for extended periods of time
will damage the pump. If fluid does not start to flow in 30 seconds, revisit the previous steps. If every step has been
followed, manually fill the pump with the process fluid or a lubricating fluid compatible with the process and restart the
pump. If no fluid is flowing within 30 seconds shut the pump down and proceed to troubleshooting section of this
document.
Once pump is operational, listen for any untoward noise, check for any significant vibration or indications of binding. If any
of these are observed, the pump should be stopped immediately and a thorough check of the installation should be made
to determine the cause. Correct any fault(s) prior to re-starting the pump.
Summary of Contents for IOM E Series
Page 9: ...1901 a00 9 TEMPERATURE RATINGS...
Page 10: ...1901 a00 10 MAGNETIC COUPLING STRENGTHS...
Page 49: ...1901 a00 49 Notes...
Page 50: ...1901 a00 50 Notes...