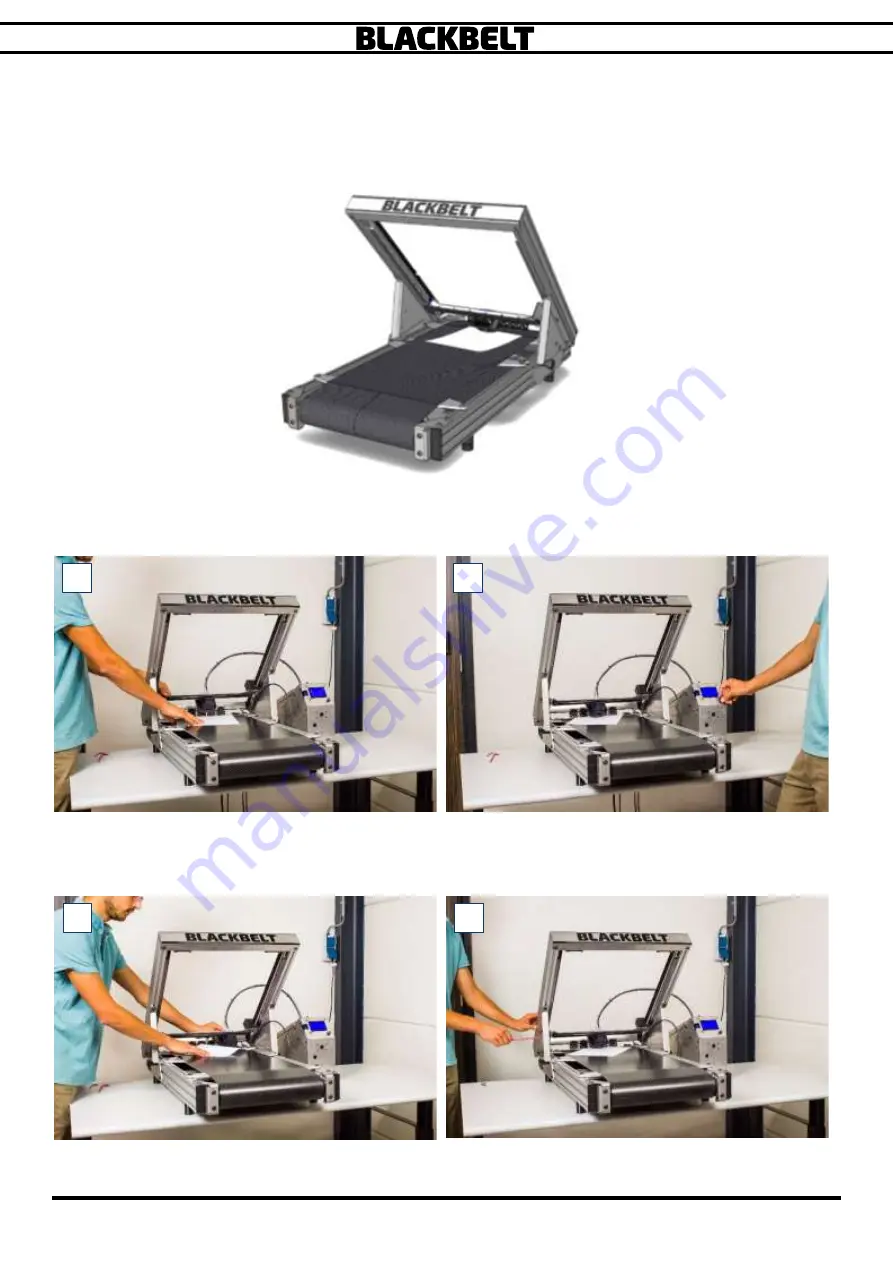
Version 2020-5.0_ENG
56
5.3
Calibration Y axis
You’ll need a 5
mm and 3mm
Hexagon
key and a sheet of paper
5.
Set the gantry to 45° and mount a printhead.
6.
Take a piece of paper, put it on the conveyor belt and place the printhead onto it:
7.
Turn the printer on, press the jog wheel, select by rotating and pressing
Prepare
→
Move axis
→
Move Y
→
Move 0.1mm
8.
Turn the jog wheel to the right until you can move the paper freely
9.
Now carefully move the printhead by hand to the left and right side, while constantly checking with the
piece of paper if you can still move it freely. Do not move any further when you notice a resistance. [3]
10.
If you start noticing a resistant at one side, move the printhead to the opposite side.
11.
Loosen the following 3 screws for ½ rotation at one side of your choice, using the 5mm Hexagon key:
1
2
3
4
Summary of Contents for Blackbelt
Page 1: ...Installation User Manual Bowden varioDrive Original document Version 2020 5 0 ...
Page 2: ...Version 2020 5 0_ENG 1 Intentionally left blank ...
Page 4: ...Version 2020 5 0_ENG 3 Intentionally left blank ...
Page 8: ...Version 2020 5 0_ENG 7 Intentionally left blank ...
Page 9: ...Version 2020 5 0_ENG 8 1 Safety and compliance ...
Page 14: ...Version 2020 5 0_ENG 13 Intentionally left blank ...
Page 15: ...Version 2020 5 0_ENG 14 2 Introduction ...
Page 19: ...Version 2020 5 0_ENG 18 3 Installation ...
Page 40: ...Version 2020 5 0_ENG 39 Intentionally left blank ...
Page 41: ...Version 2020 5 0_ENG 40 4 Design Guide ...
Page 54: ...Version 2020 5 0_ENG 53 Intentionally left blank ...
Page 55: ...Version 2020 5 0_ENG 54 5 Maintenance ...
Page 72: ...Version 2020 5 0_ENG 71 Intentionally left blank ...
Page 73: ...Version 2020 5 0_ENG 72 6 Additional hardware ...
Page 92: ...Version 2020 5 0_ENG 91 5 6 7 8 9 10 11 12 ...
Page 99: ...Version 2020 5 0_ENG 98 7 Additional technical info ...
Page 107: ...Version 2020 5 0_ENG 106 7 3 3 BlackBelt PCB v1 3 For legacy machines sold in 2018 ...