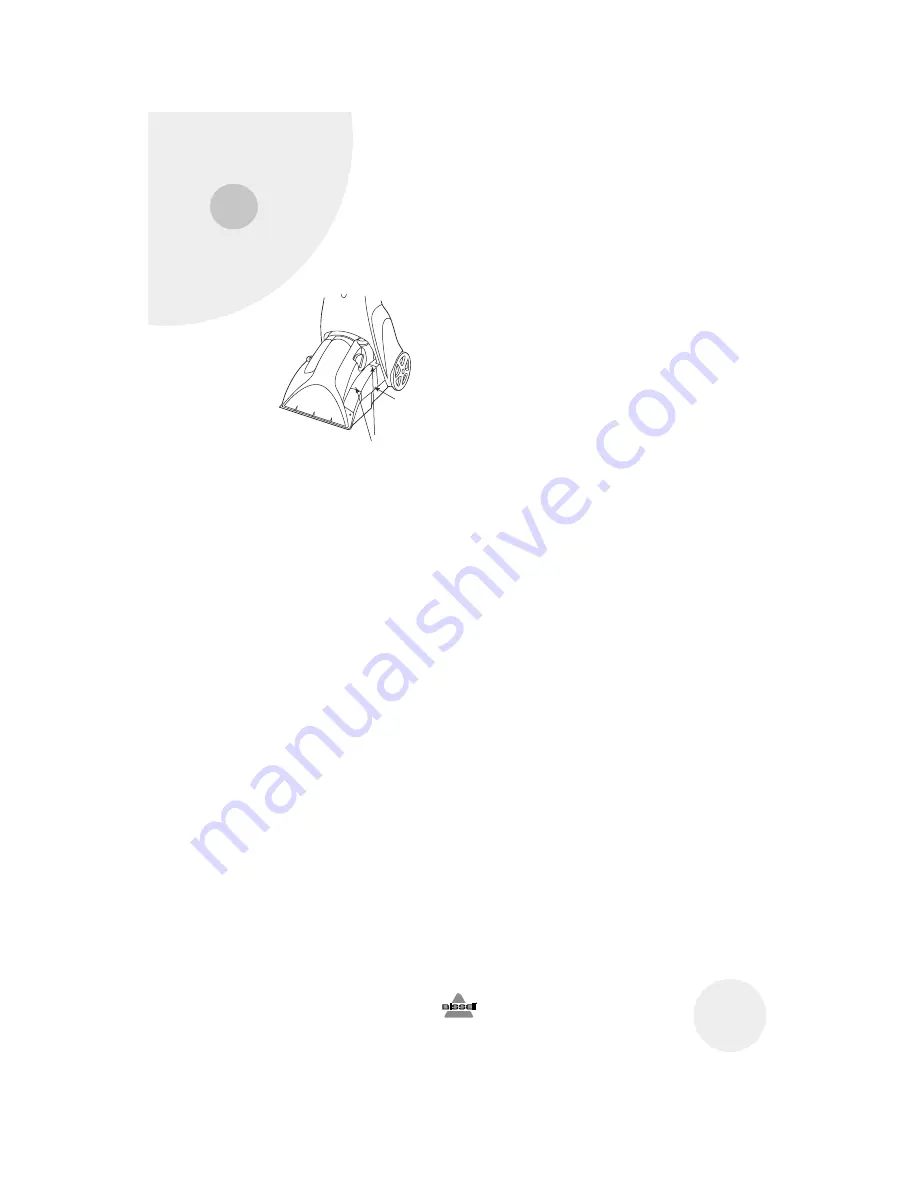
T
roubleshooting / User Maintenance (Continued)
Reduced spray or no spray. (Continued)
Possible Cause
Remedies
6.
The Pump Belt may be broken.
6.
Turn the machine
OFF (O)
and unplug
from the outlet. To check if a Pump
Belt has broken, you will need a flat
head screwdriver. Insert the blade
end into the lower slot of the Belt
Access door to release the lower
snap. If necessary, insert the blade
end into the upper slot to release the
upper snap. Examine the belt for
breakage. You should be able to
see the Pump Belt looped around the
motor shaft. If it is broken or missing,
please refer to Replacement Parts on
page 19 before calling Consumer
Services. Complete installation
instructions will accompany the
replacement
belt.
DirtLifter PowerBrush does not turn.
Possible Cause
Remedies
1. The Brush Belt or Pump Belt
1. Turn the machine
OFF (O)
and unplug
is off or broken.
from the outlet. To check if the Brush
Belt or Pump Belt has broken, you
will need a flat head screwdriver.
Insert the blade end into the lower
slot of the Belt Access door to release
the lower snap. If necessary, insert
the blade end into the upper slot to
release the upper snap. Examine the
belt for breakage. If broken, please
refer to Replacement Parts on page 19
before calling Consumer Services.
Complete installation instructions
will accompany the replacement belt.
Carpet Protector is not spraying. (Select Models Only)
Possible Cause
Remedies
1.
Cartridge not connected to the tool.
1.
Follow instructions on cartridge
assuring proper fit.
2.
Solution clogging the Spray Trigger.
2.
Soak applicator tool in hot water.
Spray without the cartridge attached to
purge any residual Solution left in the tool.
3.
Applicator tool spray is blocked.
3.
Soak applicator tool in hot
water. Spray without the cartridge
attached
to
purge any residual
Solution left in the tool.
Insert
Screwdriver
Blade Here
Lift Here
17
w w w . b i s s e l l . c o m 8 0 0 . 2 3 7 . 7 6 9 1
ug310-5868_1699_306.indd 17
ug310-5868_1699_306.indd 17
3/1/06 3:14:04 PM
3/1/06 3:14:04 PM