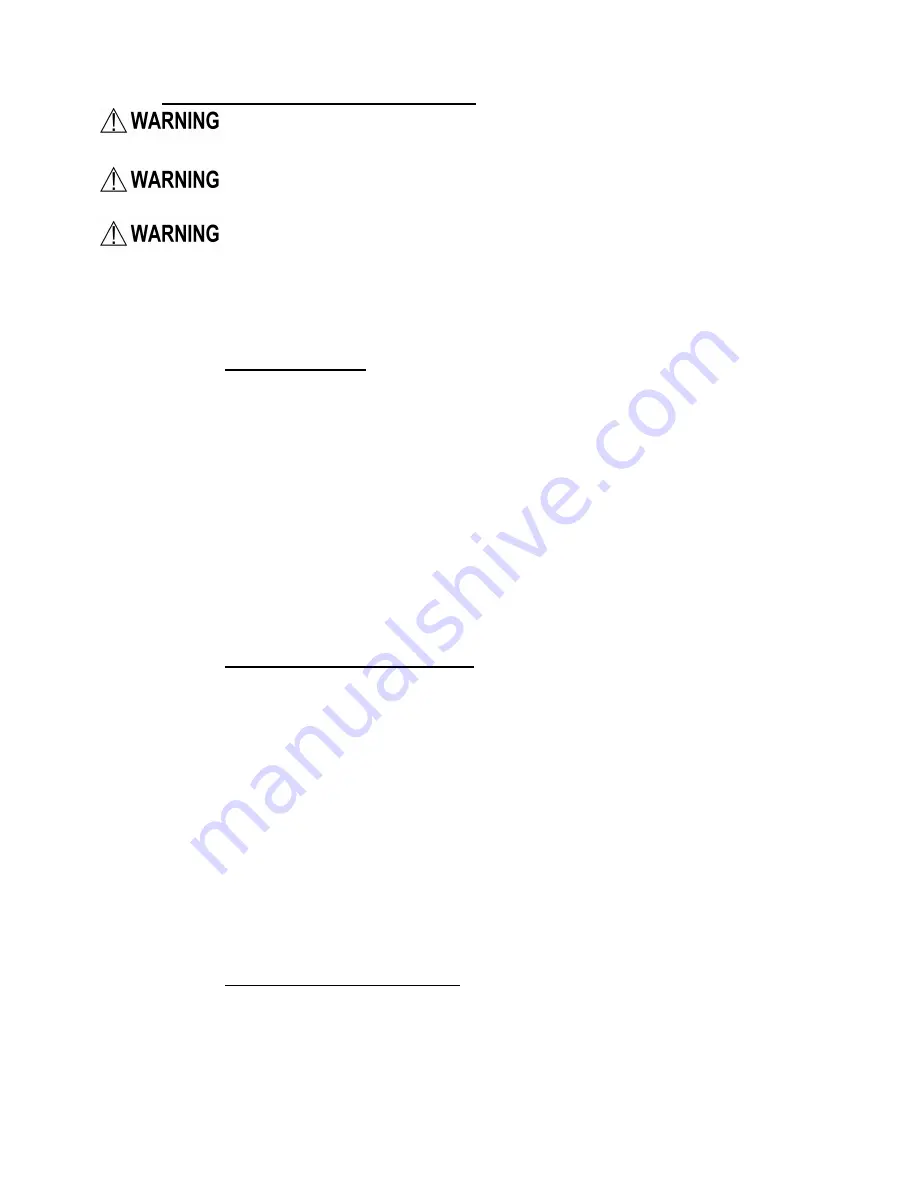
Copyright 2010 Biological Controls
2
8/19/2010
2.
INSTALLATION MECHANICAL
Turn off power at the facility fuse or circuit breaker panel before
proceeding with wiring or installation activities.
The system has more than one electrical-disconnect.
Always Support the Equipment Directly From Building Structure. Obtain an
approved fixture attachment design before proceeding with the installation. The
ceiling support system of the building must be checked to assure that it is
sufficient to carry the weight of the hardware
.
2.1.
System Ducting
Connect the ducting to the Blower Module, Filter Module(s), room diffusers, and transition boxes
per the system design. Secure the ducting to the inlet and exhaust collars making sure that no air-
leaks exist in the system. Ducts should run in straight lines whenever possible since elbows, bends,
and long runs will decrease the system airflow capacity (cfm).
When maximum CFM is desired, use twelve (12“) ducting wherever possible. Blower and Filter
Modules are typically equipped with 12” duct-collars. The exception is with the smaller 1/5 hp
Blower Module option that use 10” duct-collars. A 10”- 12” adaptor is added to systems that use
the 1/5hp blower module. The same adaptor may be fitted to the Filter Module if it is desired to use
10” ducting between the two components.
Solid-wall ducting is generally preferred over flex-ducting since it provides the lowest air
resistance and best CFM performance. Flex-ducting is used where the speed and ease of installation
is the priority. A combination of duct types and sizes is also an option.
2.2.
Blower Module-Mechanical
The Blower Module can be mounted on a platform or suspended. Typically it is mounted above a
suspending ceiling-grid and supported by the four corners of the chassis. The Blower Module is
designed to mount in any position depending upon the height restrictions within the ceiling area.
The unit may be supported using threaded rod, chain or perforated metal straps. All corners and
sides of the larger chassis are equipped with small depression marks in the sheet-metal to mark
standard support locations. Drill out at least four (4) of the chassis depressions to attach the desired
hardware. A set of four (4) eye-bolts eq/w nuts are provided with each Blower Module (1/4 x 20 w/
9/16” ID diameter loop) for a chain support system. The eye-bolts typically extend 1
5/16
inches off
the mounting surface of the chassis. To prevent air leaks, always calk air-gaps around holes or
mounting hardware attached to the chassis.
The 1/5 hp blower module chassis dimensions are smaller than the ½ and ¼ hp Blower Module
chassis. See the specifications for dimensions. In general, the 1/5 hp system is equipped for 10 inch
ducts and the ¼ and ½ hp systems utilizes 12” ducting. Adaptors may be equipped when required.
2.3.
Filter Module-Mechanical
The MICROCON® EXC7 and UV Filter Modules are designed to fit within the standard (nominal
24" x 24") T-bar hardware used to suspend ceiling tiles. Gasket each Filter Module onto the T-'bar
grid surface to provide an air-tight seal between the module and the T-bar channels.
Four (4) small brackets located on the top of the Filter Module chassis must be used to level and support the
weight of the unit using approved cable, wire, or chain hardware.