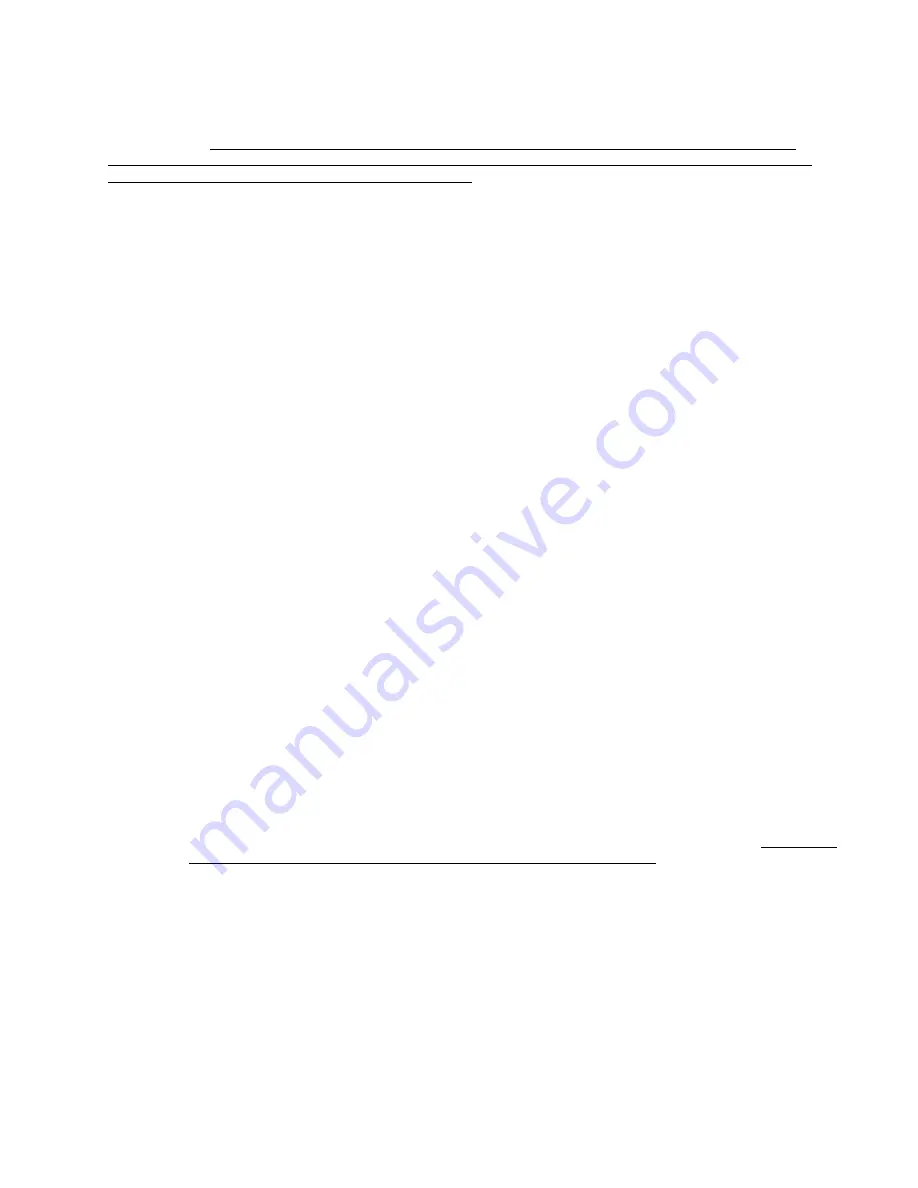
VIII.
M A I N T E N A N C E A N D S E R V I C E - C O N T .
53
The steps in these procedures are divided into two parts. The first part is “TO TEST”. This describes the procedure used to
test each specific component of the unit to determine its condition. The second part is “TO CALIBRATE”. This part
describes the calibration procedure of that component if it did not pass the preceding test.
IMPORTANT:
The calibration steps need only be performed on those components that fail the “TO TEST”
procedure. Generally, calibration is only required when parts are serviced or replaced so be sure to troubleshoot
any failed test thoroughly prior to resorting to calibration.
CAUTION:
With the PC Board and/or Solenoid Board removed, great care should be
taken to protect the board from stray voltages, static electricity, and any other environmental
concerns that may damage the board. Always handle the board with care and be sure you
and your work surface are properly grounded.
1.
GAS SOURCE - 60% O
2
/ 100% O
2
a.
If this Crossvent is used with an air/oxygen blender, then to ensure the most accurate calibration
throughout all settings, a low flow blender set to 60% O
2
should be used.
b.
If it is used only with oxygen, then use 100% oxygen.
2.
SUPPLY PRESSURE – 17 - 55 PSI (117 – 380 kPa)
a. The pressure at the supply input(s) to the ventilator should be maintained between 17 - 55 PSI (117 – 380 kPa)
at all times.
3.
PEEP VALVE ZERO -
[
20 ML/M
TO TEST:
a. Connect the exhalation valve port on the back of the CV-2i+ to a low flow test instrument.
b. Using hemostats or a similar tool, clamp off the blue PEEP line between the small cross fitting and the white
bleed manifold mounted to the top of the D.A.R.V.. Also clamp off the yellow line between the PEEP
Variable Resistor (131) and the bleed manifold.
c. Turn the PEEP Valve (18) shaft fully CCW until a flow
20 ML/M is obtained as observed on the test
instrument (Slight resistance in the valve at this point is normal, however, do not force the valve. If abnormal
resistance is felt prior to the valve closing to within this specification, it should be replaced.)
IF IT FAILS THE ABOVE TEST, CALIBRATE AS FOLLOWS:
d. Clamp off the blue PEEP line between the small cross fitting and the white bleed manifold mounted to the
top of the D.A.R.V. Also clamp off the yellow line between the PEEP Variable Resistor (131) and the bleed
manifold.
e. Remove the shaft extender from the valve shaft by loosening the two setscrews. Turn the valve shaft until the
specification stated in step “c” is met. Position the shaft extender on the PEEP Valve shaft with its stop pin
against the left side of the stop. Tighten the setscrews in this position.
f. Remove hemostats.
4.
PIP VALVE ZERO -
[
20 ML/M
TO TEST:
a.
Connect the exhalation valve port on the back of the CV-2i+ to a low flow test instrument.
b.
Using hemostats or similar tool, clip off the yellow tube coming off the side of the DARV.
CAUTION:
Failure to do this could result in damage to the ventilator in the steps that follow
c. Using hemostats or a similar tool, clamp off the orange line between the D.A.R.V. Variable Resistor (130) and
the white bleed manifold mounted to the top of the D.A.R.V. Also clamp off the orange line between the PIP
Variable Resistor (130) and the bleed manifold.
d. In the Calibration menu, activate valves, and turn on valve B.
e. Turn the MAX Valve (22) shaft fully CCW until a flow
20 ML/M is obtained as observed on the test
instrument. (Slight resistance in the valve at this point is normal, however, do not force the valve. If abnormal
resistance is felt prior to the valve closing to within this specification, it should be replaced.)
IF IT FAILS THE ABOVE TEST, CALIBRATE AS FOLLOWS:
e. Remove the D.A.R.V. orange test plug from the cross next to the D.A.R.V. Variable Resistor (130) and
connect this barb to a low flow test instrument.
f Clamp off the orange tube between the D.A.R.V. Variable Resistor and the white bleed manifold as well as the
orange tube between the PIP Variable Resistor and the bleed manifold.
g. Remove the shaft extender from the valve shaft by loosening the two setscrews.
h. Turn the valve shaft until the specification stated in step “e” is met. Position the shaft extender on the MAX
Valve shaft with its stop pin against the left side of the stop. Tighten the setscrews in this position.