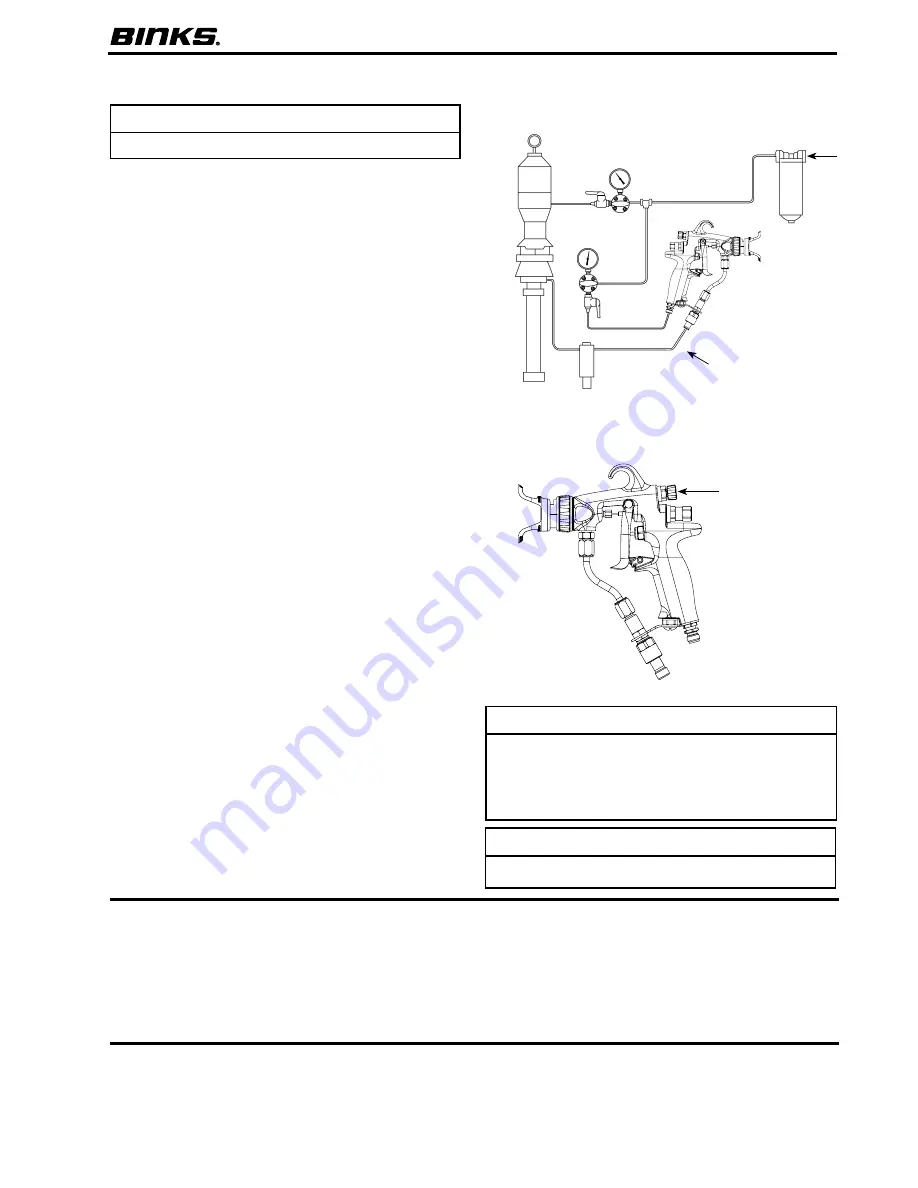
3
1. Connect your high-pressure fluid hose to the gun fluid
inlet and tighten securely.
2.
Connect your air hose to the gun air connection and tight-
en securely.
3. Slowly increase air to the pump to obtain a fluid pres-
sure at the gun’s lower end of the pressure range. A typi-
cal starting fluid pressure is 250 psi. Actual starting
pressure points may be higher or lower than 250 psi and
depend on the setup including the type of pump used,
the type of material sprayed, and the spray gun itself.
4. Using the control knob on the air regulator, set the air
pressure at zero.
5. To test the spraying pattern, spray a piece of wood or
cardboard with a fast pass about one foot away from the
surface. The results of the test will allow you to deter-
mine the uniformity of the particle size and spraying pat-
tern.
6.
If the spraying pattern develops tails or is not uniform,
gradually increase the air pressure as necessary to devel-
op a uniform spraying pattern. 14 psi is the maximum
inlet air pressure for HVLP (15 psi max. for HVLP twist
tip cap), or use 20-40 psi inlet air pressure for Trans-
Tech. The HVLP flat tip and twist tip air caps con-
sume 8.3 SCFM air at their respective maximum inlet
air pressures. The Trans-Tech flat tip and twist tip air
caps consume 13 SCFM at 30 psi inlet air pressure.
The air is used to assist the atomization of the coating.
7. If the quality of spray is acceptable, begin spraying. If
the spraying rate is too slow to keep up with the produc-
tion line speed, or if the quantity of material sprayed is
inadequate for acceptable coverage, gradually increase
the fluid pressure in 50 psi increments using the fluid
regulator control knob. However, note that as the fluid
pressure increases, more air is needed to eliminate the
tails.
Consistency in spraying can be increased across spray gun
operators and similar spraying jobs by developing pressure
standardization charts. Repeat step 6 until the required mate-
rial coverage and spraying speed are achieved. If the maxi-
mum fluid pressure is reached before the required material
coverage and spraying speed are achieved, you may need to
switch to a larger fluid tip.
tYPIcaL HooK-UP
Fan pattern adjustment: turn knob counterclockwise to
decrease pattern; clockwise to increase pattern (Fig. 2).
SPRaY GUn SEt-UP
Pump
Regulator
Regulator
Air
Air
Air
Fluid
Fluid Filter
Oil and Water
Extractor
figure 1
figure 2
Fan
Adjustment
Control Knob
When using the
twist tip air cap, the
primary purpose of
the fan pattern
adjustment knob is
to eliminate tails in
the spray pattern.
fLUID tIP SELEctIon
Factors to consider in selecting a fluid tip for an air-assist
airless spray gun include (1) the size of the parts being
sprayed; (2) the production line speed; (3) the material
flow rate and film thickness; (4) the viscosity of the
material applied; (5) the type of material applied; and (6)
the quality of atomization of the coating required.
The selection of a fluid tip necessary to perform a specif-
ic spraying job is best determined through a combination
of experimentation and expert advice from your material
and equipment suppliers.
fLUID HoSES
Air-assist airless spray guns operate at fluid pressures
higher than operating pressures of air spray guns. As a
result, when operating an air-assist airless spray gun, it is
critical to select the appropriate fluid hose that is rated for
the pressure range at which the airless gun is operated.
Air
In
notE
for HVLP spray, fan adjustment feature requires 14 psi max.
of air inlet pressure (15 psi max. for HVLP twist tip.) for
trans-tech spray, fan adjustment requires approximately
20-40 psi of air inlet pressure. Higher fluid pressure requires
higher air inlet pressures to accommodate pattern
adjustment.
notE
Before proceeding, make sure trigger lock is engaged.
notE
Do not hang gun by trigger. this will cause needle damage
or malfunction.
Gun