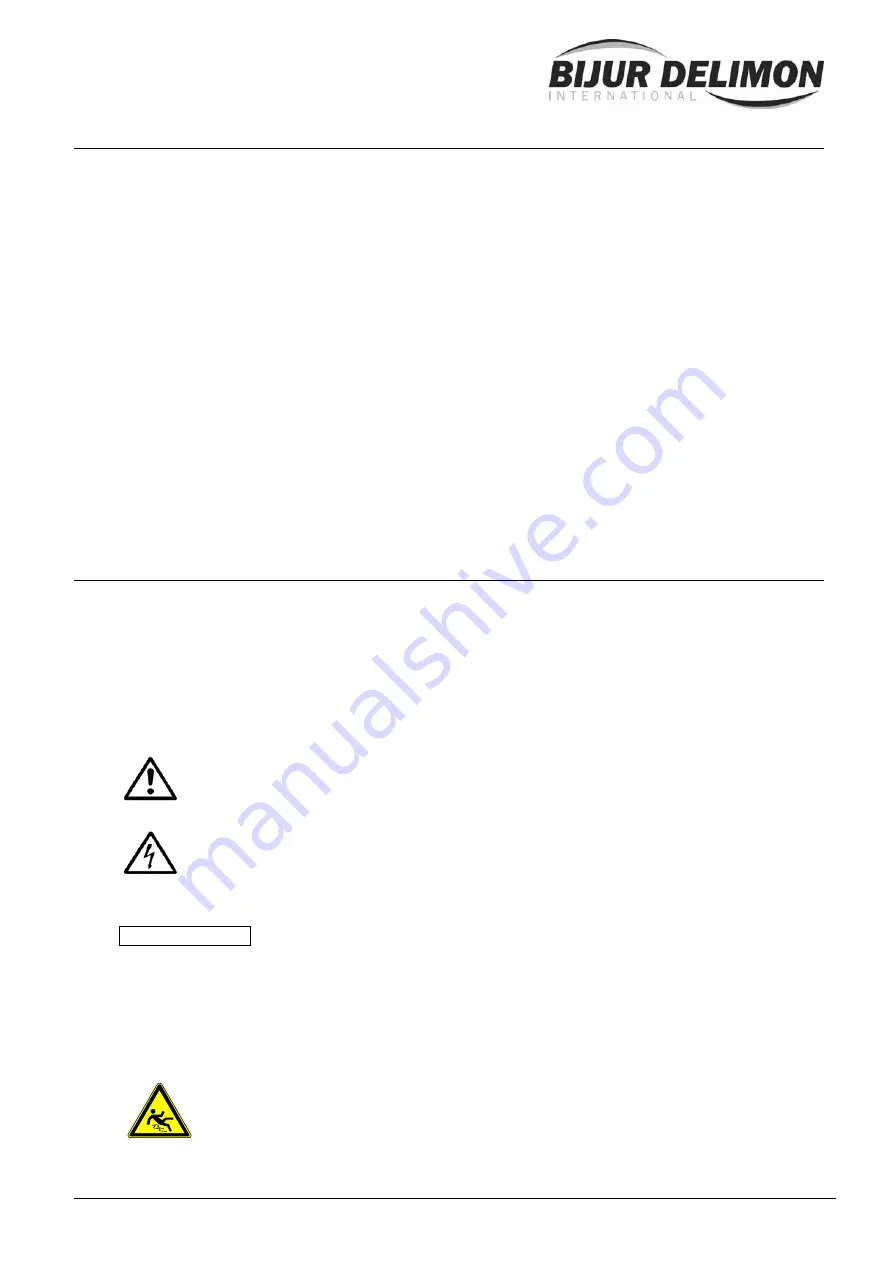
Page 2 of 16
BA_2005_2_GB_D2
Replacement for BA_2005_1_GB_D2
1. General
Prior to start up, we recommend to read these operating instructions carefully as we do not assume any
liability for damages and operating troubles which result from the nonobservance of these operating
instructions!
Any use beyond the applications described in these operating instructions is considered to be not in
accordance with the product’s intended purposes. The manufacturer is not to be held responsible for any
damages resulting from this: the user alone bears the corresponding risk.
As to figures and indications in these operating instructions we reserve the right to make technical changes
which might become necessary for improvements.
The copyright on these operating instructions is kept reserved to the company DELIMON. These operating
instructions are intended for the erecting, the operating and supervising personnel. They contain
regulations and drawings a technical nature which must not – completely or partially - be distributed nor
used nor communicated to others without authorization for competition purposes.
Company address, spare parts and service address
DELIMON Branch
office
Arminstraße 15
Am Bockwald 4
D-40277 Düsseldorf
D-08344 Grünhain-Beierfeld
Phone
: +49 211 77 74-0
E-mail : [email protected]
Fax
: +49 211 77 74-210
www.delimon.de
2. Safety
These operating instructions contain fundamental instructions which are to be observed during erection,
operation and maintenance. Therefore it is absolutely necessary for the fitter and the competent qualified
staff/user to read these operating instructions before installation and start-up. The operating instructions
must be available at all times at the place of use of the machine/system.
Not only the general safety instructions stated under this main point “safety“ are to be observed, but also
the other specific safety instructions stated under the other main points.
2.1
Identification of safety warnings in the operating instructions
The safety warnings contained in these operating instructions which, if not observed, may cause dangers to
people, are specially marked with general danger symbols
safety sign according to DIN 4844-W9, warning about a danger spot ,
in case of warning about electric voltage with
safety sign according to DIN 4844-W8, warning about dangerous electric voltage.
In case of safety instructions which, if not observed, may cause damage to the machine and its function,
the word
ATTENTION
is inserted.
Instructions that are directly attached to the machine, as for example
•
rotational direction arrow
•
identifications for fluid connections
must be observed at all events and maintained in a fully legible condition.
•
Note: There is an increased skid risk in case of spilled/leaked out lubricants. They are to be removed
at once properly.
Safety sign according to DIN 4844-2, W28, warning about skid risk.