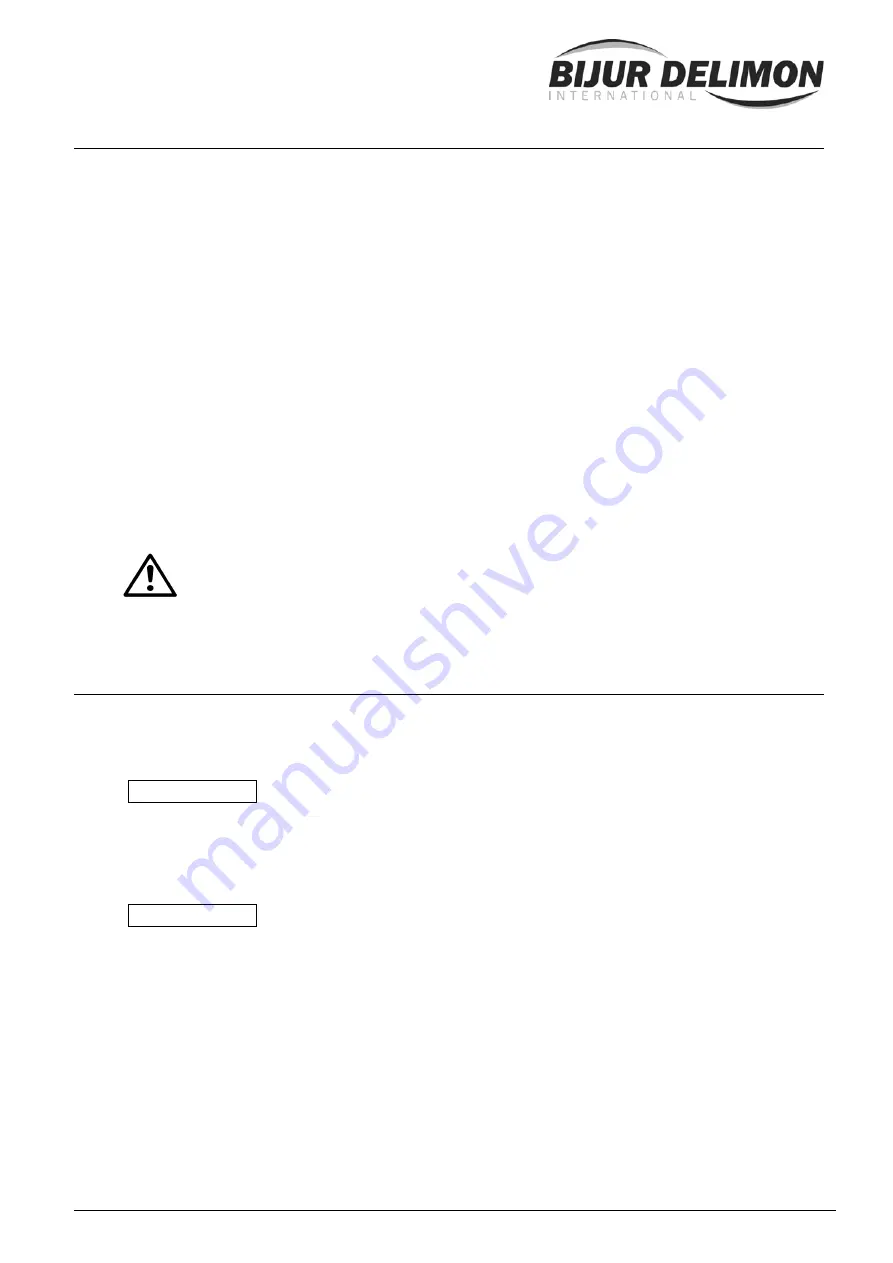
Page 10 of 11
BA_2005_5_GB_BSB
7. Start-up
Pump installation
Install the pump vertically. Then connect the motor to the control panel (refer to wiring diagram). The motor
may rotate in either directions, but with the view to the gearing of the transmission gear box, it is
recommended that is should run clockwise.
Filling the reservoir and pipe lines
Efficient operation demands the use of only clean lubricant! Contamination of the lubricant can lead to
operation trouble and damage. To shorten the time of the initial start-up it is advisable to fill the grease using
a barrel pump or a press via the R-outlet. Containers should only be re-charged via the filler plug provided,
preferably by use of a filling pump or grease gun, or from the works bulk supply system. The container must
always be kept closed and care taken in ensuring that the lubricant is kept free from dirt and other
contamination. Recharging of the container at the correct time is most important, otherwise there is a risk of
air finding its ways into the pump and main lines. In contrast to other pumps, no oil is required to be charged
for initial start-up. To ensure trouble-free functioning the pump itself should be de-aerated by running it for a
period without back pressure. As soon as the lubricant is discharged free of air from pressure connection (P),
the feed lines can be connected. Run the pump then and continue to bleed all main lines, then make the
connection to the metering elements.
Connecting the pressure and relief lines
The pressure outlet port at the flange (52) (section A-B) has a pipe connection of G 3/8" BSP female thread.
When using the pump in a dual-line system, this branch is used to connect the 4/2-way reversing valve (or
3/2-way valve respectively). On the pump housing (17) there is the pressure relief port of G 3/8" BSP to
connect the 4/2-way valve. In filling or greasing systems without a change-over valve, this port should be shut
by a plug.
WARNING!
Make
sure
to
fill
tube
(44)
(section
A
‐
B)
correctly
otherwise,
and
in
the
event
of
failing
to
provide
it
at
all,
there
is
a
danger
to
life
and
limb
to
everybody
involved.
8. Maintenance
Strainer
The strainer (51) (section A-B) should retain any contamination, which, by carelessness, has been allowed
to get into the lubricant. Therefore, check and clean with petrol or spirit the strainer at regular intervals. Any
dirt therefore is retained inside the strainer (51). When disassembling the impurities are removed.
ATTENTION
A blinding filter due to pollution is leading to the bursting of the strainer.
Pressure relief valve
The integral pressure relief valve (54-62) (section A-B) is adjustable from 0 up to 400 bar. Turning the square
spindle (62) clockwise the pressure is increased, and turning it anti-clockwise it is decreased. The pressure
relief valve is set by the manufacturer’s to a pressure of 400 bar.
ATTENTION
The
pressure
rating
adjusted
at
relief
valve
must
not
be
higher
than
max.
admissible
operating
pressure
of
the
elements
installed
downflow.
Bursting discs
The respond of the burst plates protects the components of the system (e. g. pipes, fittings etc.) for
overpressure.
Two burstings discs (47) are fitted in the stud (48) (section A-B) below the bush (46) which will rupture in the
event of failure, or excessive pressure beyond 500 bar building up in the pressure channel in flange (52), e.g.
if the relief valve (54-62) is clogged. When these discs burst, the lubricant issues out of the tube (44). In this
case, first remedy the cause of failure and replace two new burst discs. Under the plug (53) in the flange (52)
there are ten spare discs. When replacing new bursting discs take care that the curved face shows towards
the bushing (46). If incorrectly fitted, the burst pressure is apt to be increased to such an extent causing the
pump drive to be damaged.